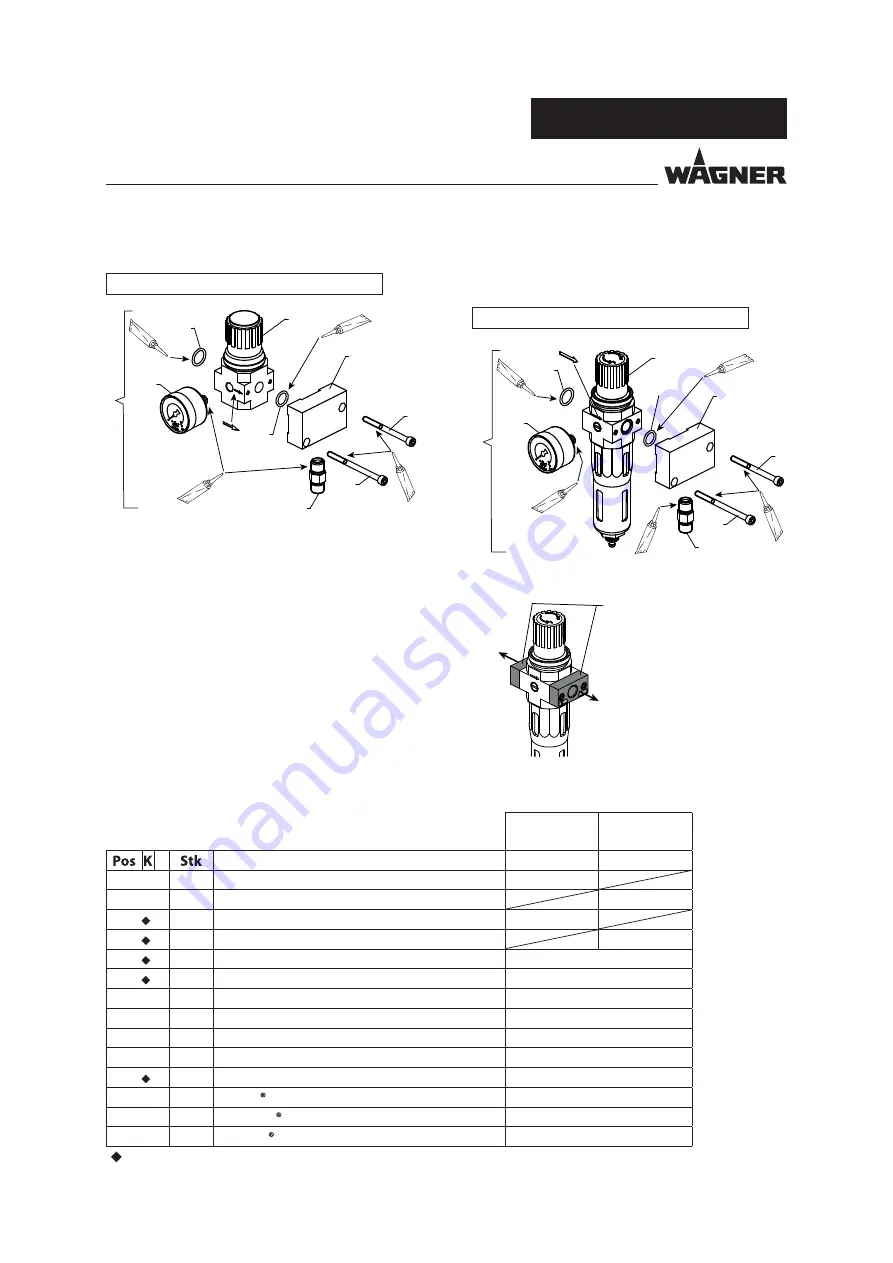
72
Wildcat & Puma 40 cm
3
B_05400
1
8
3
5
6
7
9
10
11
*
13
14
12
14
B_05402
B_05401
2
8
4
5
6
7
9
10
11
*
13
14
12
14
12
OPERATING MANUAL
VERSION 05/2015
ORDER NUMBER DOC2303659
13.11
AIRCOAT REGULATOR AND AIRCOAT FILTER REGULATOR
Spare parts list AirCoat regulator and AirCoat fi lter regulator
AirCoat
Regulator
AirCoat fi lter
regulator
Designation
Order No.
Order No.
1
1
AirCoat regulator set
2328611
2
1
AirCoat fi lter regulator set
2333478
3
1
Pressure regulator, LR-1/4-D-O-l-Mini
2309972
4
1
Filter control valve
2331950
5
1
Pressure gauge, 0-10 bar RF40 (d40)
9998677
6
1
O-ring
9974166
7
1
Holding plate
2325527
8
1
Hexagon socket head cap screws
9906021
9
1
Hexagon socket head cap screws
9900320
10
1
Double fi tting R1/4-R1/4
9994627
11
1
O-ring
9971313
12
1
Loctite 542
9992831
13
1
Molykote DX grease
9992616
14
1
Mobilux EP 2 grease
9998808
= Wearing parts
Pos 3 or 4:
* Observe the fl ow direction
(direction of arrow to the housing)
Pos. 5:
Screw in the pressure gauge until
the white sealing ring is completely
in the fi lter control valve. Thereafter
continue turning the pressure gauge
only to align the display scale.
Pos. 4:
Before assembling,
remove both threaded
plates and four screws.
AirCoat Regulator
AirCoat fi lter regulator
Summary of Contents for Wildcat 18-40
Page 2: ......
Page 47: ...47 Wildcat Puma 40 cm3 OPERATING MANUAL VERSION 05 2015 ORDER NUMBER DOC2303659...
Page 53: ...53 Wildcat Puma 40 cm3 OPERATING MANUAL VERSION 05 2015 ORDER NUMBER DOC2303659...
Page 74: ...74 Wildcat Puma 40 cm3 OPERATING MANUAL VERSION 05 2015 ORDER NUMBER DOC2303659...
Page 79: ......