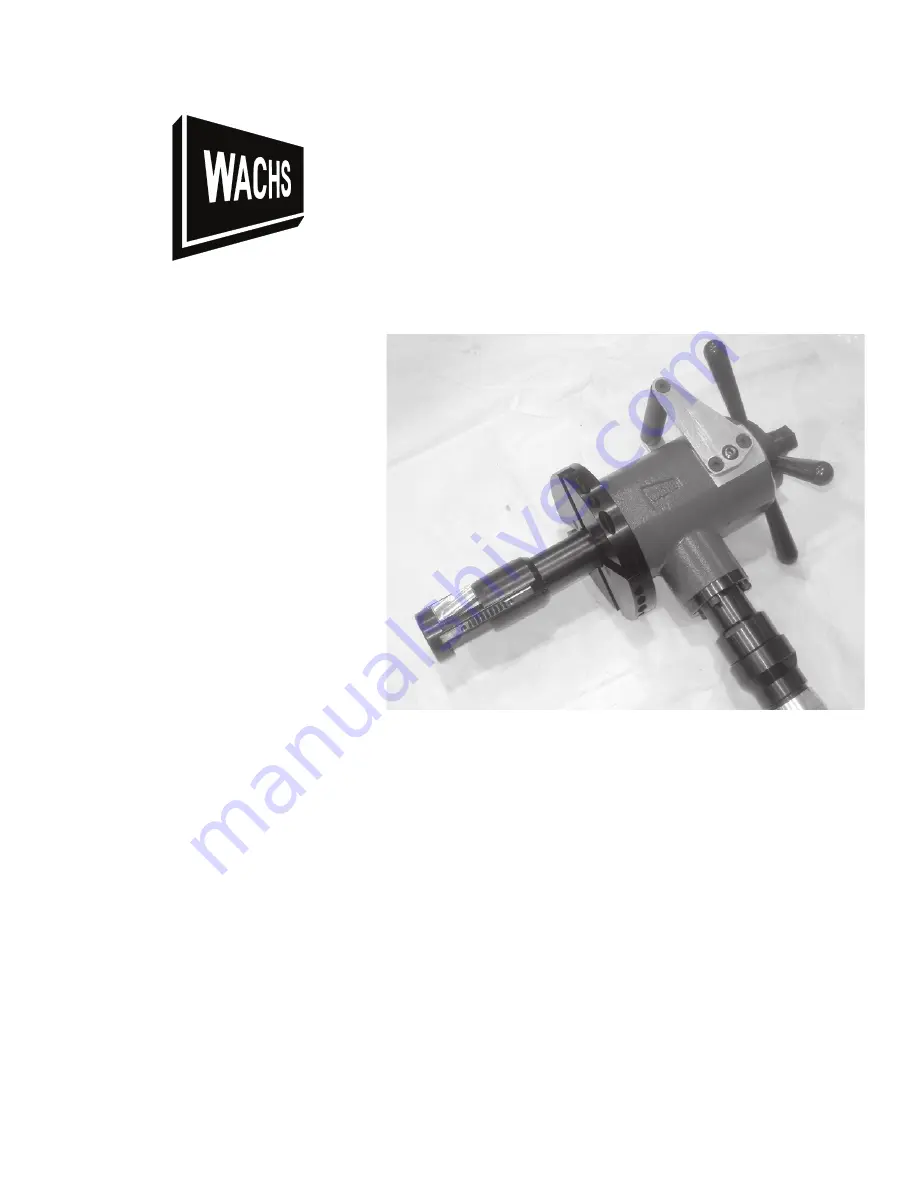
SDB 206 and FF 313
User’s Manual
Copyright © 2013 E.H. Wachs. All rights reserved.
This manual may not be reproduced in whole or in part
without the written consent of E.H. Wachs.
E.H. Wachs
600 Knightsbridge Parkway
Lincolnshire, IL 60069
www.ehwachs.com
E.H. Wachs Part No. 56-MAN-01
Revision B
September 2013
Summary of Contents for SDB 206
Page 10: ...SDB 206 and FF 313 8 Part No 56 MAN 01 Rev B E H Wachs...
Page 12: ...SDB 206 and FF 313 10 Part No 56 MAN 01 Rev B E H Wachs SDB 206 Electric Drive 56 000 02 NOTE...
Page 18: ...SDB 206 and FF 313 16 Part No 56 MAN 01 Rev B E H Wachs...
Page 26: ...SDB 206 and FF 313 24 Part No 56 MAN 01 Rev B E H Wachs...
Page 75: ......