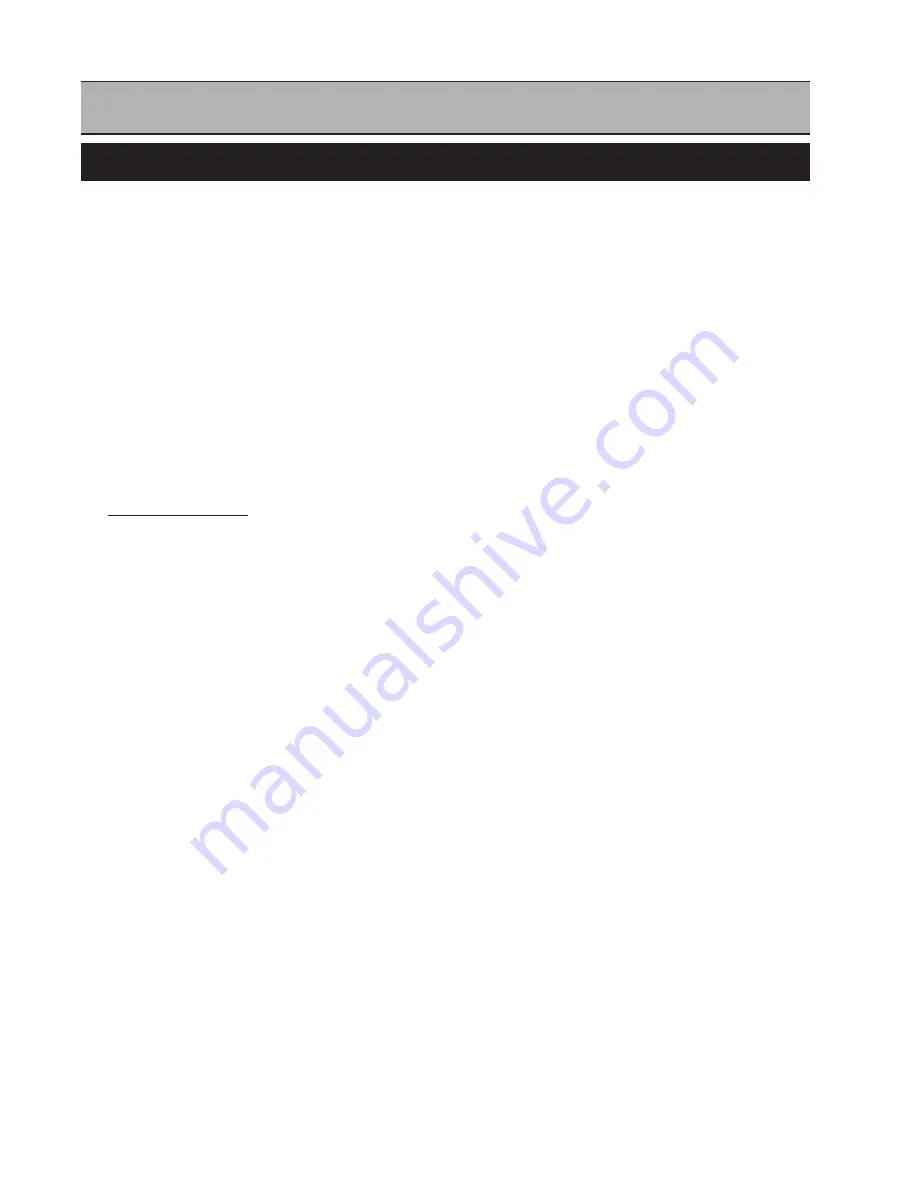
FF 424 FLANGE FACING SYSTEM
2. Start machine and turn feed nut in until
cutting tool contacts the pipe. Continue
facing until pipe has a clean finish. Retract
the beveling head. Turn off machine and
insert O.D. beveling tool.
3. Start machine again and feed beveling tool
into the pipe until facing tool touches again.
Adjust O.D. beveling tool in or out radially
depending on the land thickness desired.
4. The last tool bit to install is the I.D. deburring
tool. It should be placed in the slot opposite the
beveling tool. It may also require adjustment, in
or out, to produce the desired height and depth.
NOTE: If only two tools are to be used, place
them in opposite slots to offset cutting load.
Continuous Operation: Once the cutting tools are
in place, the machine can be moved from one pipe to
another of the same size without resetting the tool
bits.
F. Tips For a Good Finish
1. Always place mandrel as close to pipe end as
possible.
2. Use a cutting oil or other coolant generously.
This will also increase cutter life.
3. Adjust cutting head RPM for material. A good
rule of thumb is the harder the material, the
slower the speed.
4. Always keep a lot of pressure on the feed nut
and pull out of cut quickly when prep is finished.
Tips for a good finish:
SINGLE POINT FLANGE FACING BEVELING
MODULE
1.
Always place mandrel as close to pipe end as
possible.
2.
Use a cutting coolant generously. This will also
increase cutter life.
3.
The feed rate for each trip is .005 per revolution.
4.
CHATTER: Tool chatter occurs when the tool
begins to vibrate during a cut. Excessive tool
chatter can cause poor quality surface finishes.
Chatter can be caused by any one of a number
SECTION V
FF 424 SET UP AND OPERATING PROCEDURES
of variables inherent in a portable machine of this
type. Check tooling:
•
To high of an operating speed or to great of a
radial feed rate for the material being machined.
5. INTERMITTENT CUTS: When working on a rough
cut end of a piece of pipe or a warped flange, the
need to do an intermittent cut does exist. In order
to prolong tool life and reduce shock loads on the
machine and inserts, intermittent cuts should be
done at a slower speed and feed rate. Once a full
cut is achieved, operating speeds can be in
creased to normal machining procedures.
6. As you finish a pass, note your location on
the indiced axial feed gauge. Then, to take your
next pass, rotate the feed handle backwards 1 full
turn to your noted location and retract your tool
slide. Once retracted, rotate the feed handle in
the amount you wish for the cut depth of your
next pass. This will allow you to retract the slide
with out damaging the tooling, remove all back
lash in the feed handle, and give you an exact
depth of cut on your next pass.
7. To produce a 500 RMS or record groove finish, the
best results are achieved with a finish cut depth of
.007” to .008”.
16.
36
Summary of Contents for FF 424
Page 2: ......
Page 6: ...SDB 412 and FF 424 4 Part No 66 MAN 01 Rev A E H Wachs...
Page 12: ...SDB 412 and FF 424 10 Part No 66 MAN 01 Rev A E H Wachs...
Page 24: ...22...
Page 40: ...SDB 412 and FF 424 38 Part No 66 MAN 01 Rev A E H Wachs SDB 412 Air Drive 66 000 01 NOTE...
Page 48: ...SDB 412 and FF 424 46 Part No 66 MAN 01 Rev A E H Wachs...
Page 66: ...SDB 412 and FF 424 66 Part No 66 MAN 01 Rev A E H Wachs...
Page 69: ......
Page 70: ...600 Knightsbridge Parkway Lincolnshire IL 60069 847 537 8800 www ehwachs com...