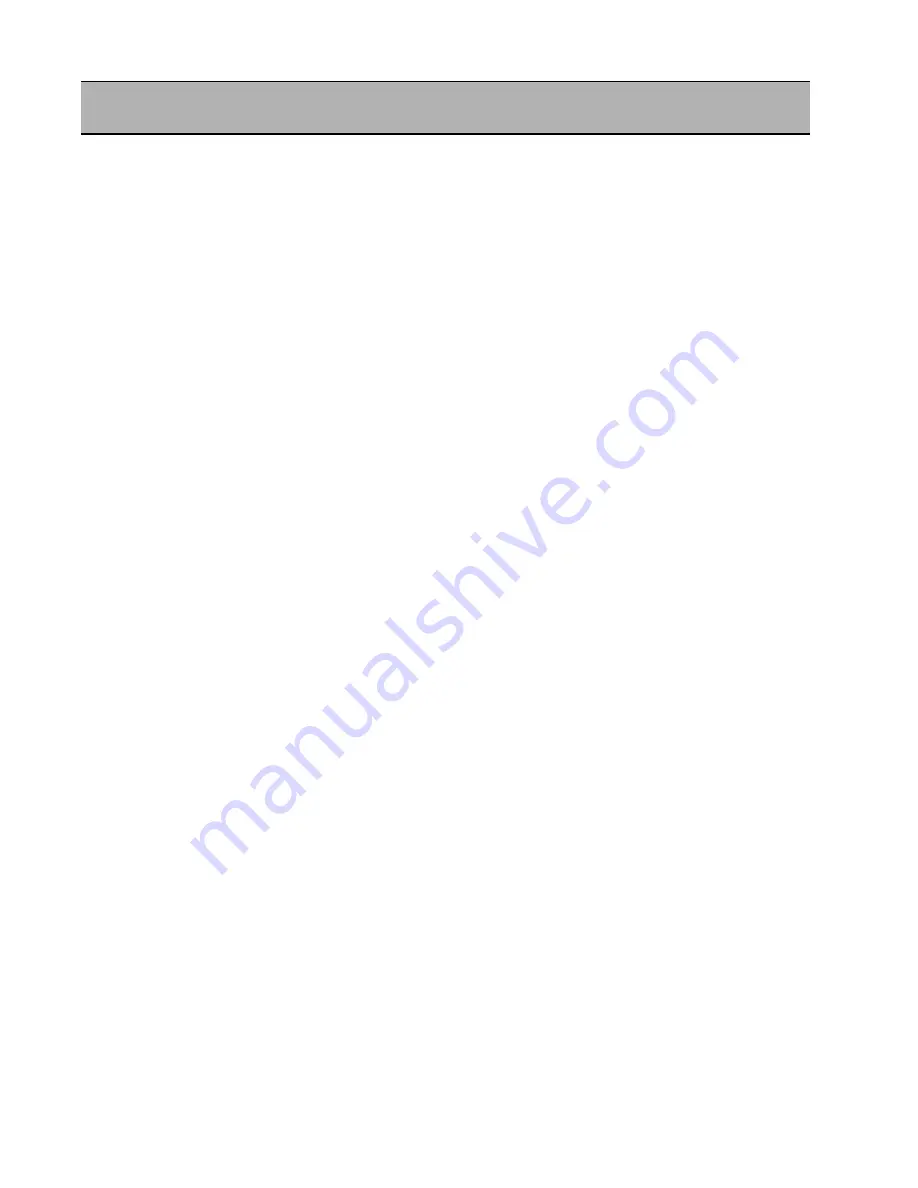
SDB 412/2 SMALL DIAMETER BEVELER
SECTION VI
MAINTENANCE
Under normal operating conditions, the bevel gear sets and roller bearing should be inspected every 100
hours of operation and lubricated as needed. If exceptionally difficult work has been performed or if excessive
coolant used, inspection and lubrication should be done much more frequently.
The bore of the cutting head, feed nut and mandrel must be kept cleaned and oiled.
After the first ten hours of operation, the mainshaft bearing preload should be checked. Remove the air motor.
Remove the 6, 1/4-20x 7/8 SHCS to remove feed nut housing (66-002-00). Bend the Iockwasher (66-034-00) tab
clear from the locknut (66-033-00). Insert and tighten an old, used tool bit into one of the slots on the cutting head.
Clamp machine into a bench vise. Using the lock nut tool and a torque wrench, tighten locknutto 150ft lbs. while
rotating the main housing. Once tight, secure lock washer tang into the closest locknut slot. Replace feed nut
housing and fasteners. Replace and secure air motor.
After every ten hours of operation, inspect the mandrel guide bushing for wear. Replace as necessary.
NOTE
:
Excessive chatter may indicate a worn mandrel guide bushing
After 40 hours of operation, flush the air motor with a solution of three parts cleaning solvent and one part air
motor oil. After flushing, add I oz. (30 cc) air motor oil into air line and run air motor for one minute. It is very
important that the components of the mandrel assembly remain clean and free from corrosion. The legs and
machine surfaces should be cleaned and oiled on a daily basis.
MANDREL STRESS INSPECTION PROCEDURE:
1. The mandrel should be removed from the machine body and inspected after every twenty hours of
operation.
2. Remove the drawbar nut (#66-025-00) and the collar nut (# 66-024-00).
3. Remove the mandrel from the machine body by rotating the feed handles counter clockwise.
4. Physically examine the mandrel and threads, look for any signs of wear or damage.
5. Measure the length of the threaded drawbar. If the draw bar length is 21-1/2”, the drawbar may remain
in use. If the length of the drawbar is equal to or exceeds 22W in length the drawbar is no longer safe
and should be replaced.
18
Summary of Contents for FF 424
Page 2: ......
Page 6: ...SDB 412 and FF 424 4 Part No 66 MAN 01 Rev A E H Wachs...
Page 12: ...SDB 412 and FF 424 10 Part No 66 MAN 01 Rev A E H Wachs...
Page 24: ...22...
Page 40: ...SDB 412 and FF 424 38 Part No 66 MAN 01 Rev A E H Wachs SDB 412 Air Drive 66 000 01 NOTE...
Page 48: ...SDB 412 and FF 424 46 Part No 66 MAN 01 Rev A E H Wachs...
Page 66: ...SDB 412 and FF 424 66 Part No 66 MAN 01 Rev A E H Wachs...
Page 69: ......
Page 70: ...600 Knightsbridge Parkway Lincolnshire IL 60069 847 537 8800 www ehwachs com...