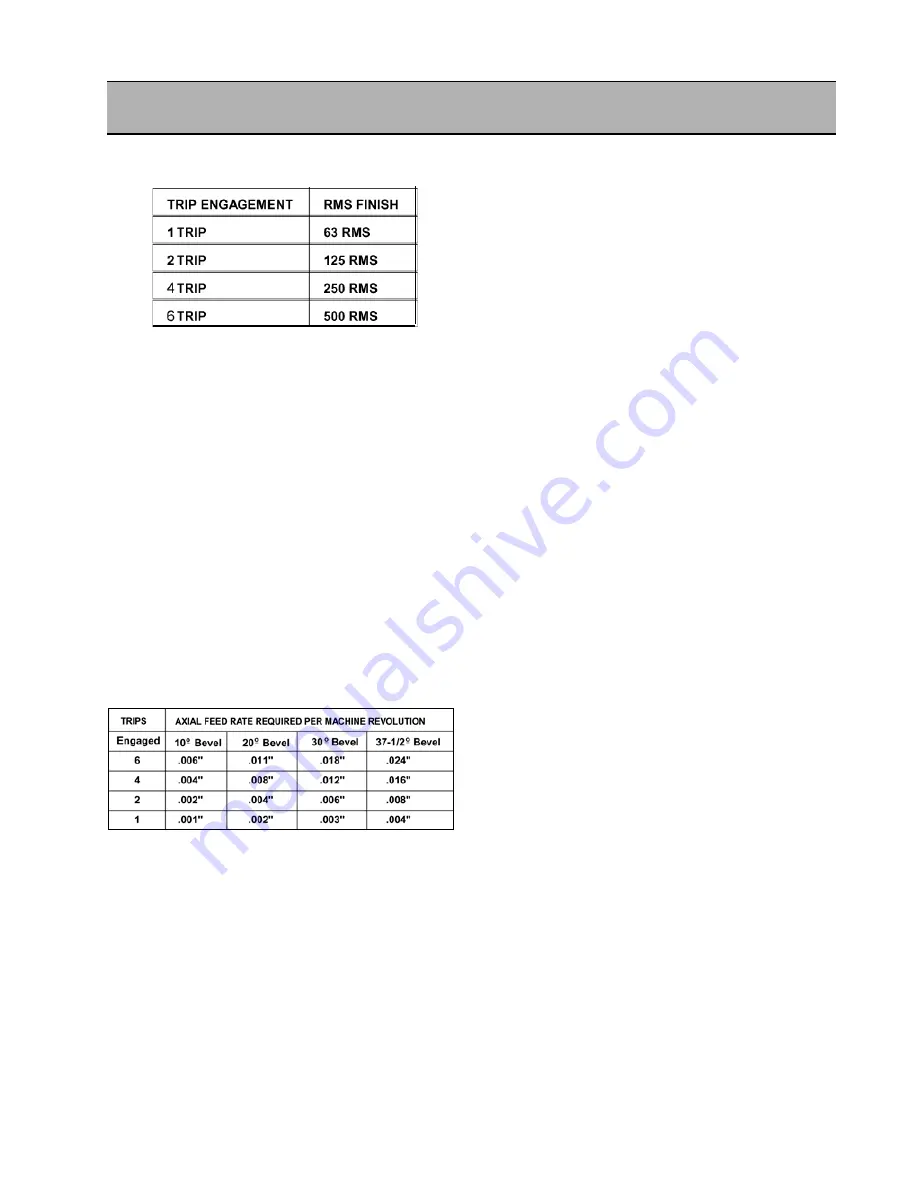
SDB 412/2 SMALL DIAMETER BEVELER
B. MANUAL BEVEL GENERATION USING
SINGLE POINT MODULE:
A bevel can be generated by feeding the cutting
tool into the work radially and axially simultaneously.
As the radial feed advances the tool automatically,
the operator must withdraw the tool by rotating the
axial feed handle counter-clockwise. The correct
amount of axial feed per machine revolution is given
in the following chart.
For example, to generate a 30 degree bevel with 6
trips engaged (the fastest tool feed setting), the
operator must withdraw the cutting tool .018” each
time the cutting tool completes a revolution. This
distance is represented by .018 (18 thousandths)
increments on the calibrated feed dial located on the
feed handle assembly.
MANUAL BEVEL GENERATION CHART
A.
FLANGE SURFACE TRIP CHART
C. TIPS FOR A GOOD FINISH:
SINGLE POINT FLANGE FACING
BEVELING MODULE
1.
Always place mandrel as close to pipe end as
possible.
2.
Use the cutting coolant generously. This will
also increase cutter life.
3.
The feed rate for each trip is .005 per revolution.
4. CHATTER: Tool chatter occurs when the tool
begins to vibrate during a cut. Excessive tool
chatter can cause poor quality surface finishes.
Chatter can be caused by any one of a number
of variables inherent in a portable machine of this
type. Check tooling: To high of an operating
speed or to great of a radial feed rate for the
material being machined.
5. INTERMITTENT CUTS: When working on a rough
cut end of a piece of pipe or a warped flange, the
need to do an intermittend cut does exist. In order
to prolong tool life and reduce shock loads on the
machine and inserts, intermittent cuts should be
done at a slower speed and feed rate. Once a full
cut is achieved, operating speeds can be increased
to normal machining procedures.
6. As you finish a pass, note your location on the
indiced axial feed guage. Then, to take your next
pass, rotate the feed handle backwards 1 full turn
to your noted location and retract your tool slide.
Once retracted, rotate the feed handle in the amount
you wish for the cut depth of your next pass. This
will allow you to retract the slide without damaging
the tooling, remove all backlash in the feed handle,
and give you an exact depth of cut on your next
pass.
7. To produce a 500 RMS or record groove finish, the
best results are achieved with a finish cut depth of
.007” to .008”.
16
Summary of Contents for FF 424
Page 2: ......
Page 6: ...SDB 412 and FF 424 4 Part No 66 MAN 01 Rev A E H Wachs...
Page 12: ...SDB 412 and FF 424 10 Part No 66 MAN 01 Rev A E H Wachs...
Page 24: ...22...
Page 40: ...SDB 412 and FF 424 38 Part No 66 MAN 01 Rev A E H Wachs SDB 412 Air Drive 66 000 01 NOTE...
Page 48: ...SDB 412 and FF 424 46 Part No 66 MAN 01 Rev A E H Wachs...
Page 66: ...SDB 412 and FF 424 66 Part No 66 MAN 01 Rev A E H Wachs...
Page 69: ......
Page 70: ...600 Knightsbridge Parkway Lincolnshire IL 60069 847 537 8800 www ehwachs com...