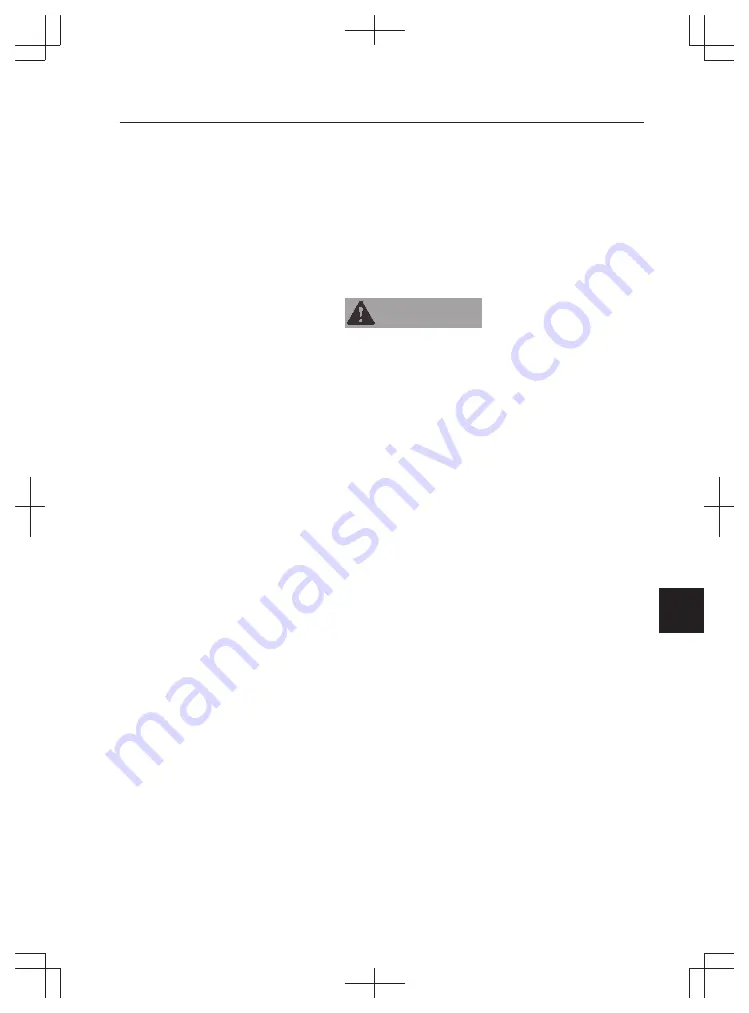
Safety when servicing
This section deals with the safety rules which
should be followed when checking and servicing the
machine. It also describes the risks when working
with unhealthy material and ways to avoid personal
injuries.
Further safety rules and warnings texts are given
within the respective sections.
WARNING
Risk of burns!
Hot machine parts could cause burns.
Allow hot machine parts to cool before performing
adjustments or service. Wear personal protective
equipment.
Safety when servicing
131