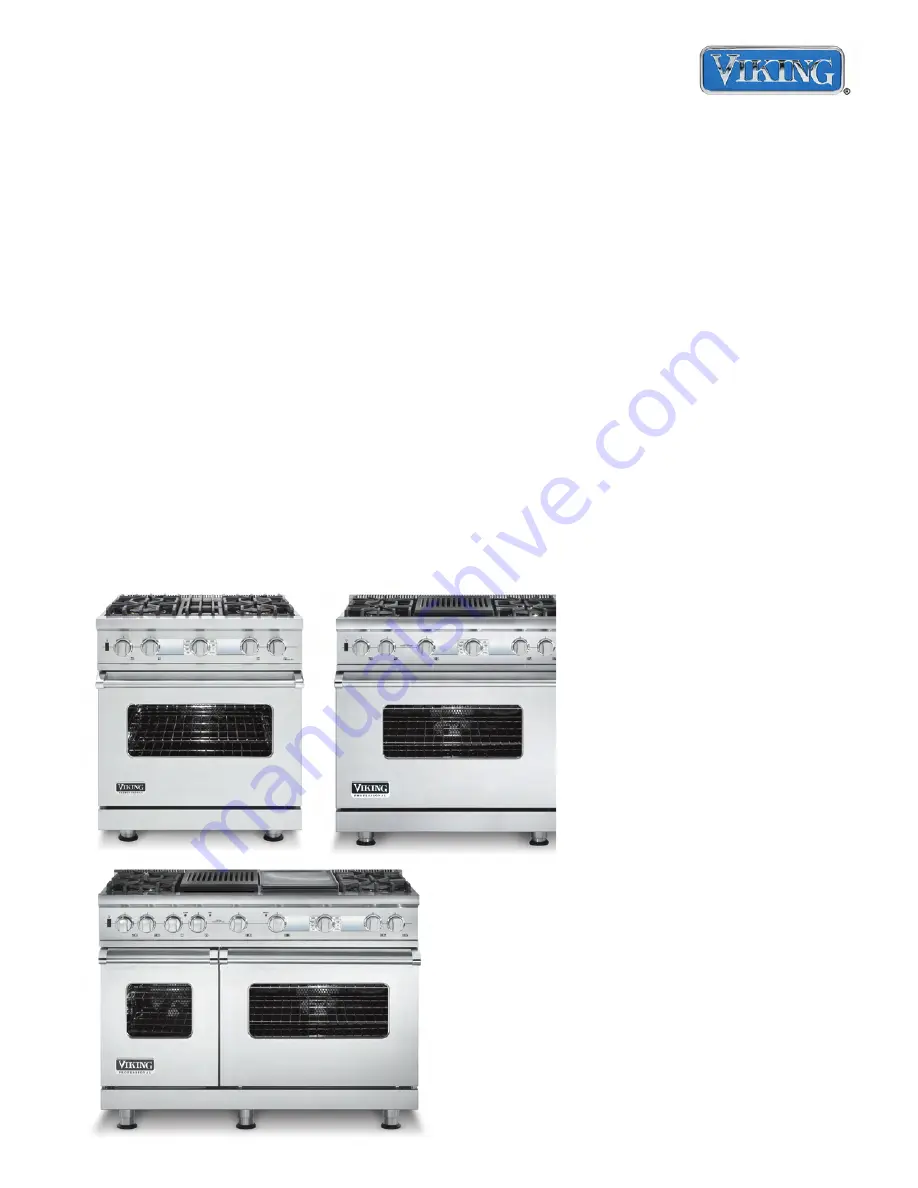
Preferred Service
SMC-0012A
June, 2011
This manual is to be used by qualified appliance technicians only.
Viking does not assume any responsibility for property damage
or personal injury for improper service procedures done by an
unqualified person.
Service
Manual
This Base Manual covers general and
specific information including, but not
limited to the following models:
VDSC530T–4B
VDSC536T–6B
VDSC536T–4G
VDSC536T–4Q
VDSC548T–6G
VDSC548T–6Q
VDSC548T–4GQ
Electronic
Control Dual
Fuel Range
Summary of Contents for VDSC530 Series
Page 124: ...Wiring and Schematics Wiring Schematic VDSC530T 4B 124 2010 Viking Preferred Service ...
Page 125: ... 2010 Viking Preferred Service 125 Wiring and Schematics Wiring Schematic VDSC536T 4G ...
Page 126: ... 2010 Viking Preferred Service 126 Wiring and Schematics Wiring Schematic VDSC536T 4Q ...
Page 127: ... 2010 Viking Preferred Service 127 Wiring and Schematics Wiring Schematic VDSC536T 6B ...