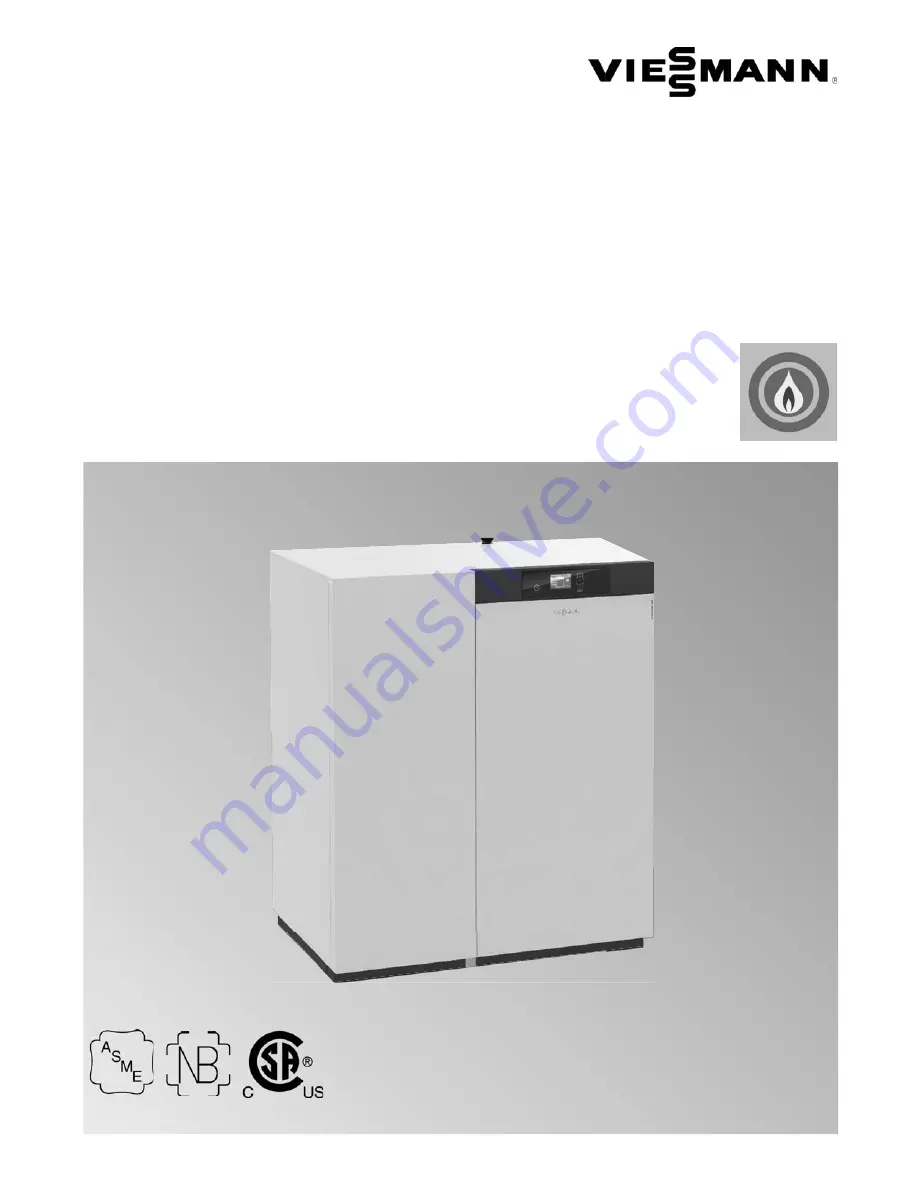
for use by heating contractor
5790 980 - 04 10/2018
Installation and Service
Instructions
VITOLIGNO 300-C
Pellet boiler, with Ecotronic weather-compensated,
digital boiler and heating circuit control unit
Heating input: 44 MBH to 193 MBH
13 kW to 57 kW
Please file in Service Binder
Product may not be exactly as shown
H