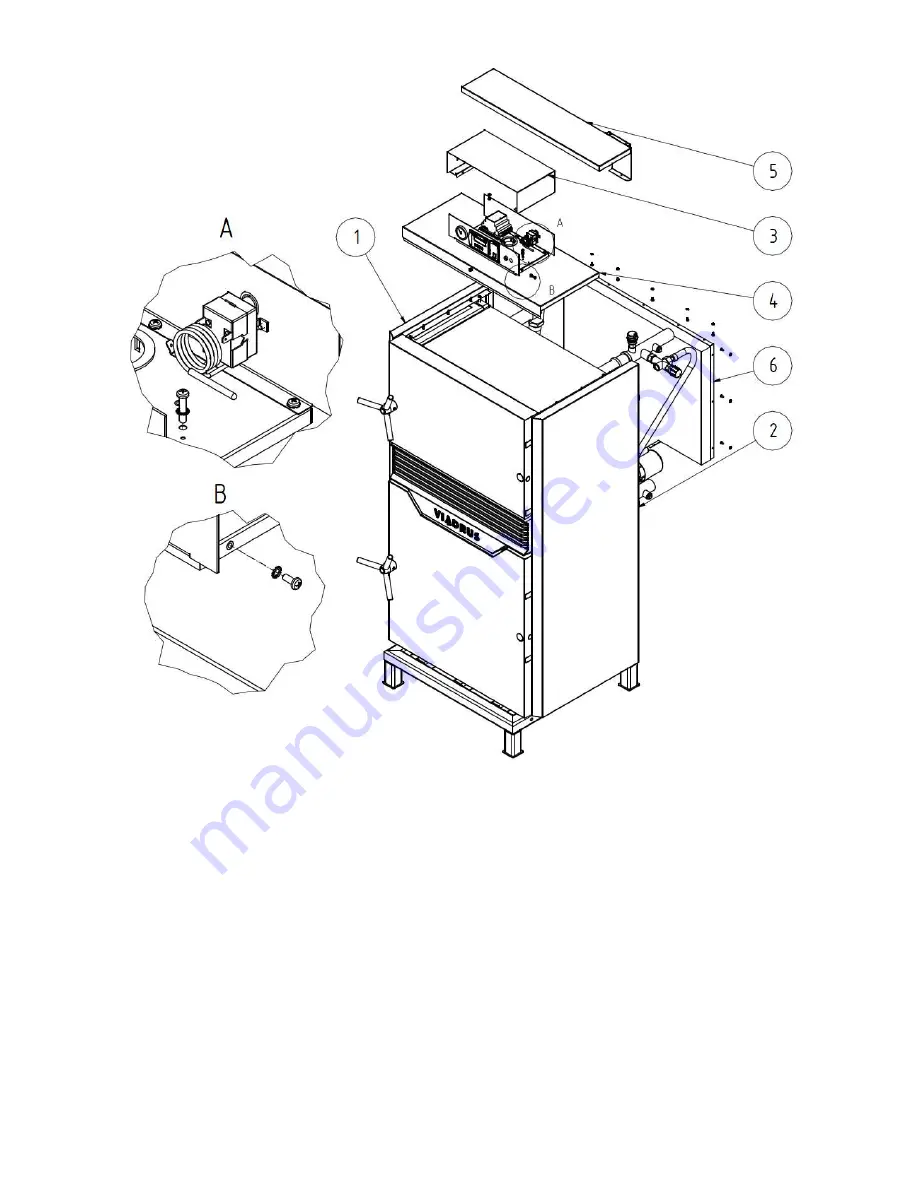
19
1
left side part of shell with
insulation
2
right side part of shell
3
upper part of the control box
4
upper front part of the shell
5
upper part of the shell
6
rear part of the shell
A Mounting the control box to the upper part of the shell
B Mounting the upper part of the control box
Fig. no. 10
Mounting the control box
Summary of Contents for Hercules P 1
Page 1: ...Hercules U26 Návod k obsluze Hefaistos P 1 MANUAL FOR BOILER OPERATION AND INSTALLATION ...
Page 44: ...44 ...
Page 46: ...46 ...
Page 47: ...47 ...
Page 48: ...48 Update Date 42 2012 GB ...