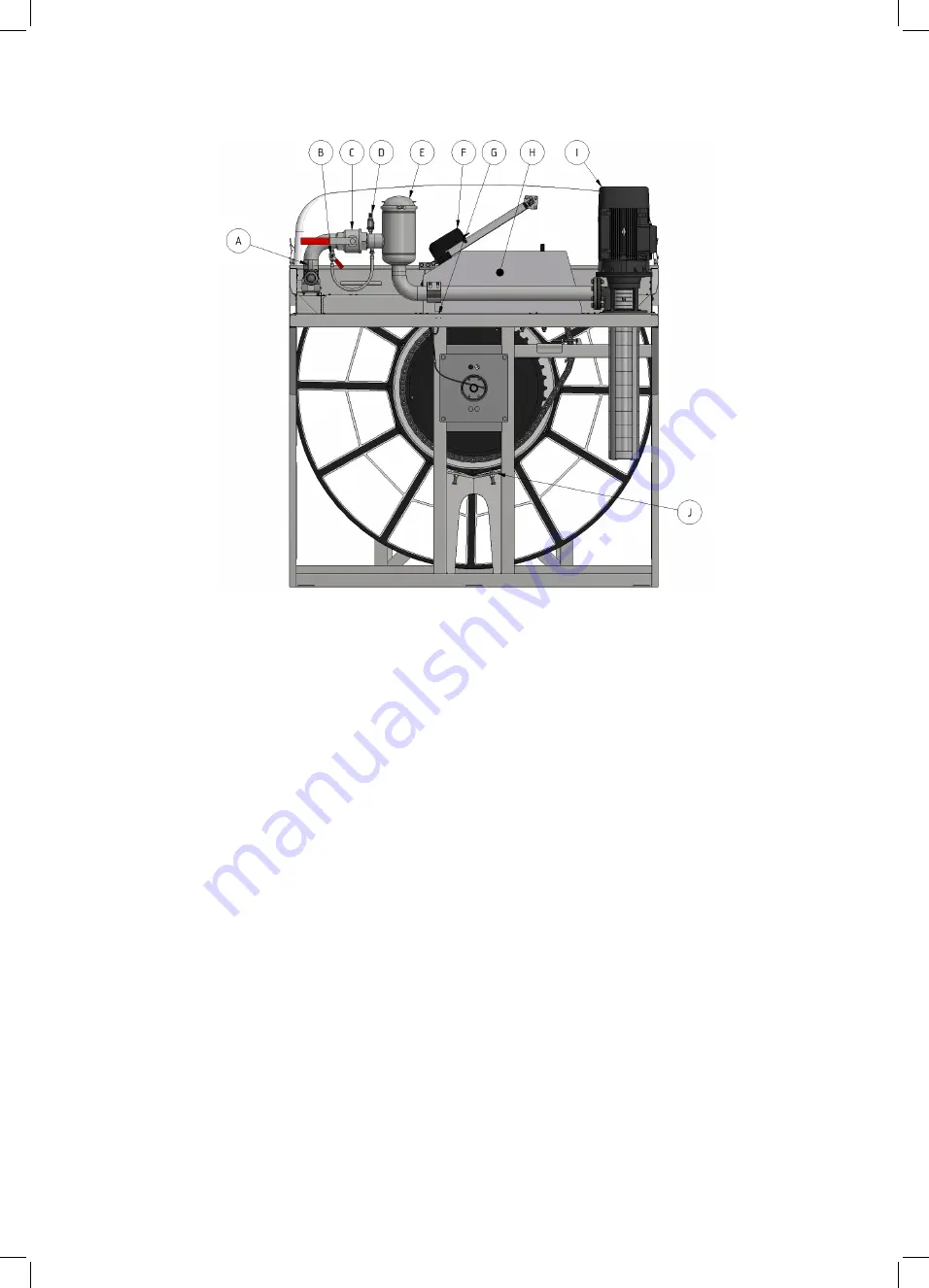
13
Operation and maintenance, Discfilter HPF2200-series PFLC
Figure 3.7 Hydrotech Discfilter in HPF2200 series type 2 (outlet side).
A. Manometer
B. Bypass valve for nozzle check
C. Shut off valve for nozzle check
D. Pressure transmittor - dry running protection for pump
E. Strainer
F. Linear actuator for opening filter cover
G. Lubrication point
H. Drive motor
I. Backwash pump
J. Drum lifter