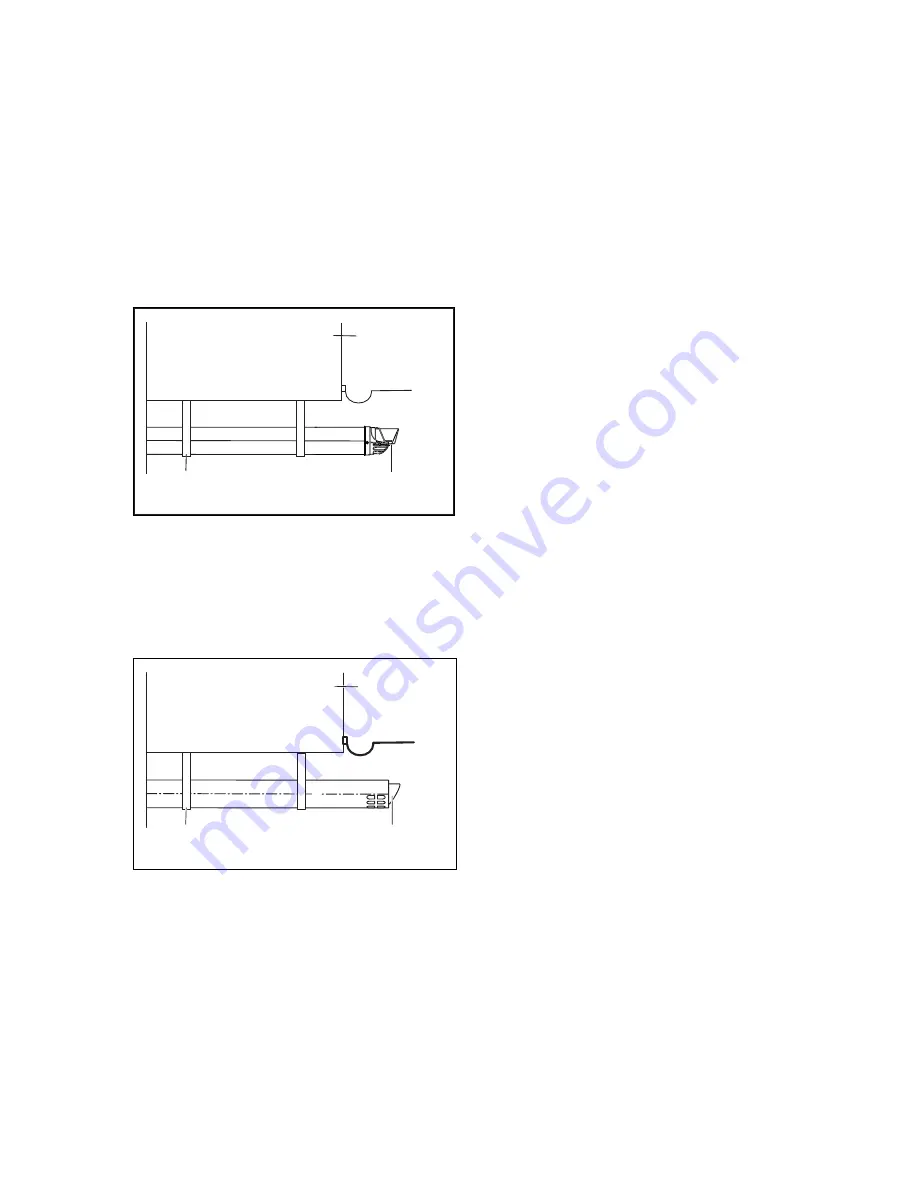
Appendix
46
Installation
and
maintenance
instructions
ecoTEC
pro
0020244995_02
I
Horizontal terminal positioning
BS 5440-1 recommends that fanned flue chimney terminals should be positioned as follows:
a) at least 2 m from an opening in the building directly opposite, and
b) so that the products of combustion are not directed to discharge directly across a boundary if the products are likely to
cause a nuisance to a neighbour or discharge over a walkway or patio.
For IE see current issue of IS 813.
For boilers covered within this manual.
1) Dimensions D, E, F and G:
These clearances may be reduced to 25 mm without affecting the performance of the boiler. In order to ensure that the con-
densate plume does not affect adjacent surfaces the terminal should be extended as shown below.
Balcony/eaves
Gutter
Adequately secured
air/flue gas pipe
The flue pipe must
protrude beyond any overhang
2) Dimension H:
This clearance may be reduced to 25 mm without affecting the performance of the boiler. However, in order to ensure that
the condensate plume does not affect adjacent surfaces a clearance of 300 mm is preferred.
For 1 and 2 above you can use a flue gas management kit to enable the termination point to be positioned and directed away
from the building fabric.
J
Opening of the flue pipe below eaves and balconies
Balcony/eaves
Gutter
Adequately secured
air/flue gas pipe
The flue pipe must
protrude beyond any overhang