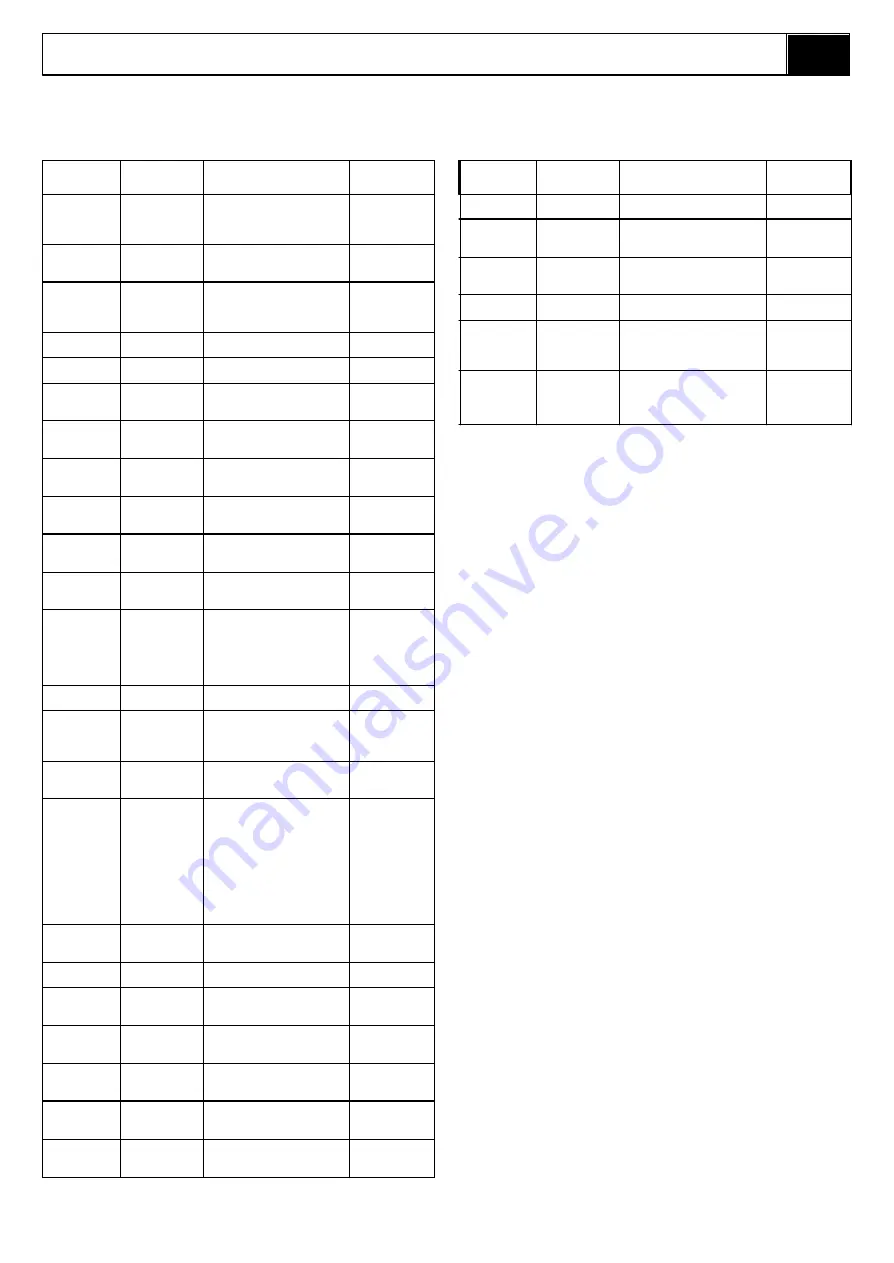
Schematics
Section
6-9
AB38 Work Platform
REFERENCE
NAME
FUNCTION
LOCATION
V10 (RV)
Main relief
Sets max system pressure to On main
valve.
145 Bar
manifold block.
V11
Single
Prevents back flow and
On base of
Overcentre
provides a hydraulic lock on
upper, lower &
valve.
the cylinder.
tele cylinders.
V12
Emergency
Allows upper and lower boom
On base of
lowering valve.
to be manually lowered.
upper and lower
cylinders.
V13
Pilot operated
Holds tele cylinder in position
On base of
check valve.
after controls are released
tele cylinder.
V14
Dual
Holds pressure in
On base of
Overcentre
master/slave closed circuit
master cylinder.
valve.
and provides host burst
protection. (Set 160 Bar).
V15
Dual
Holds pressure in slave
On base of
Overcentre
cylinder and provides host
slave cylinder.
valve.
burst protection.
(Set 120 Bar).
6.2
6.2. Hydraulic Schematics
Table 6-2: Hydraulic Schematic Legend
REFERENCE
NAME
FUNCTION
LOCATION
BRK
Brake.
Spring applied - hydraulically
On front end of
released brakes to stop
wheel drive
rotation of drive wheels.
motors on
(Set at 100 Bar).
chassis.
CLRV
Cross-line
To limit the max. operating
On main
relief valve.
pressure of the slew motor.
manifold block.
(Set at 50 Bar).
CV
Check Valve.
To prevent oil pressure in the
On main
brake line from being lost
manifold block.
through the main pressure
line.
CYL1
Lower boom lift Provides the force to lift the
Foward of first
cylinder.
lower boom - Boom1.
post
CYL2
Upper boom lift Provide the force to lift the
Behind second
cylinder.
upper boom - Boom2.
post
CYL3
Tlelscopic
Provides the force to
Inside Boom2
cylinder.
push/pull the tele-boom
& Tele boom.
- Boom3.
CYL4
Steering
Provides the force to
Inside front of
cylinder.
push/pull the steering torque
chassis.
arms.
CYL5
Master levelling Provides the pressure to the
Behind the
cylinder.
slave cylinder for cage
second post
levelling.
CYL6
Slave levelling
Provides the force to level
Close to cage
cylinder.
the cage up/down.
pivot at inner
Tele boom.
FL1
Return line
Continuously filters hydraulic
On top of the
filter.
return oil.
hydraulic
(10 Micron)
reservoir.
HP
Handpump.
Used for retraction of tele
On side of
boom in the case of power
manifold block.
failure. Delivers 15cc/stroke.
MMB
Main manifold
Contains the directional
On hydraulic
block.
control valves and relief
reservoir in
valves that distribute oil to
chassis.
the various functions and
control the operating
pressures.
MOT1
Slew Motor.
Drives slew bearings drive
Connected to
pinion.
drive pinion.
MP
Motor/Pump
Gear pump close coupled to
On chassis.
set.
D.C electric motor. Provides
pressurised oil flow for all
hydraulic functions.
V1
Brake oil
This valve is energised to
On main
supply valve.
allow oil into the brake
manifold block
release chamber.
V2
Brake valve.
When energised this valve
On main
prevents the pressurised
manifold block.
brake oil from venting back
to tank. When the machine is
stationary this valve
de-energises and the brake
oil vents to tank and the
brake springs apply
themselves and keep the
machine stationary.
V3
Pressure
Prevents pressures in
On main
reduction valve. excess of 100 Bar entering
manifold block.
the brake chambers.
V4
Slew Directional Send oil to the left or right
On main
Control Valve.
side of the slew motor.
manifold block.
V5
Steer
Send oil to the annular or full-
On main
Directional
bore side of the steering
manifold block.
Control Valve.
cylinder.
V6
Tele
Send oil to the annular or full-
On main
Directional
bore side of the telescopic
manifold block.
Control Valve.
cylinder.
V7
Boom2
Send oil to the annular or full-
On main
Directional
bore side of the Boom2
manifold block.
Control Valve.
cylinder.
V8
Boom1
Send oil to the annular or full-
On main
Directional
bore side of the Boom1
manifold block.
Control Valve.
cylinder.
V9
Levelling
Send oil to the annular or full-
On main
Directional
bore side of the levelling
manifold block.
Control Valve.
cylinders.
Notes:
1.
All of the Overcentre Valves represented within
this schematic have a 5:1 Pilot Ratio.
2.
The P/O Check Valve represented has a 3:1
Pilot Ratio.
3.
The maximum flow rate of the Pump/Motor Unit
is limited to 15 L/min @ 100% speed. Although
it should be noted that the actual flow rate will
depend on the applied load and the D.C. Motor
speed.
4.
The maximum ‘Return’ flow rates for each of
the functions are restricted to the following
values;
l
Slew...
4 L/min
l
Boom1...
8 L/min
l
Boom2...
5 L/min
l
Tele...
5 L/min
l
Steering...
6 L/min.
Summary of Contents for AB38
Page 2: ...ii AB38 Work Platform NOTES...
Page 4: ...ii AB38 Work Platform NOTES...
Page 6: ...iv AB38 Work Platform NOTES Foreword...
Page 10: ...Contents Section IV AB38 Work Platform i NOTES...
Page 14: ...Introduction Specifications Section 1 4 AB38 Work Platform NOTES 1 3...
Page 17: ...Machine Preparation Section 2 3 AB38 Work Platform NOTES 2 7...
Page 18: ...Machine Preparation Section 2 4 AB38 Work Platform 2 7 NOTES...
Page 29: ...Operation Section 3 11 AB38 Work Platform NOTES 3 5...
Page 30: ...Operation Section 3 12 AB38 Work Platform NOTES 3 5...
Page 59: ...Maintenance Section 4 29 AB38 Work Platform NOTES 4 21...
Page 60: ...Maintenance Section 4 30 AB38 Work Platform NOTES 4 21...
Page 66: ...Troubleshooting Section 5 6 AB38 Work Platform 5 7 NOTES...
Page 68: ...Schematics Section 6 2 AB38 Work Platform NOTES 6 0...
Page 72: ...Schematics Section 6 6 AB38 Work Platform 6 1 NOTES...
Page 73: ...Electrical Schematic Schematics 6 7 AB38 Work Platform Section 6 1...
Page 74: ...Electrical Schematic Schematics 6 8 AB38 Work Platform Section 6 1 TOP VIEW...
Page 76: ...Schematics Section 6 10 AB38 Work Platform NOTES 6 2...
Page 78: ...Section 6 2 6 12 AB38 Work Platform Schematics NOTES...
Page 81: ...Illustrated Parts Breakdown Section 7 3 AB38 Work Platform 7 2...
Page 83: ...Illustrated Parts Breakdown Section 7 5 AB38 Work Platform 7 2...
Page 85: ...Illustrated Parts Breakdown Section 7 7 AB38 Work Platform 7 2...
Page 87: ...Illustrated Parts Breakdown Section 7 9 AB38 Work Platform 7 2...
Page 89: ...Illustrated Parts Breakdown Section 7 11 AB38 Work Platform 7 2 22...
Page 91: ...Illustrated Parts Breakdown Section 7 13 AB38 Work Platform 7 2...
Page 93: ...Illustrated Parts Breakdown Section 7 15 AB38 Work Platform 7 2...
Page 95: ...Illustrated Parts Breakdown Section 7 17 AB38 Work Platform 7 2...
Page 97: ...Illustrated Parts Breakdown Section 7 19 AB38 Work Platform 7 2...
Page 99: ...Illustrated Parts Breakdown Section 7 21 AB38 Work Platform 7 2...
Page 101: ...Illustrated Parts Breakdown Section 7 23 AB38 Work Platform 7 2...
Page 103: ...Illustrated Parts Breakdown Section 7 25 AB38 Work Platform 7 2...
Page 105: ...Illustrated Parts Breakdown Section 7 27 AB38 Work Platform 7 2...
Page 107: ...Illustrated Parts Breakdown Section 7 29 AB38 Work Platform 7 2...
Page 109: ...Illustrated Parts Breakdown Section 7 31 AB38 Work Platform 7 2...
Page 111: ...Illustrated Parts Breakdown Section 7 33 AB38 Work Platform 7 2...
Page 113: ...Illustrated Parts Breakdown Section 7 35 AB38 Work Platform 7 2...
Page 115: ...Illustrated Parts Breakdown Section 7 37 AB38 Work Platform 7 2...
Page 117: ...Illustrated Parts Breakdown Section 7 39 AB38 Work Platform 7 2...
Page 119: ...Illustrated Parts Breakdown Section 7 41 AB38 Work Platform 7 2 8 9...
Page 121: ...Illustrated Parts Breakdown Section 7 43 AB38 Work Platform 7 2...
Page 123: ...Illustrated Parts Breakdown Section 7 45 AB38 Work Platform 7 2...
Page 125: ...Illustrated Parts Breakdown Section 7 47 AB38 Work Platform 7 2...
Page 127: ...Illustrated Parts Breakdown Section 7 49 AB38 Work Platform 7 2...
Page 131: ...Illustrated Parts Breakdown Section 7 53 AB38 Work Platform 7 2 NOTES...
Page 133: ...Technician s Print AB38 Work Platform Electrical Schematic...