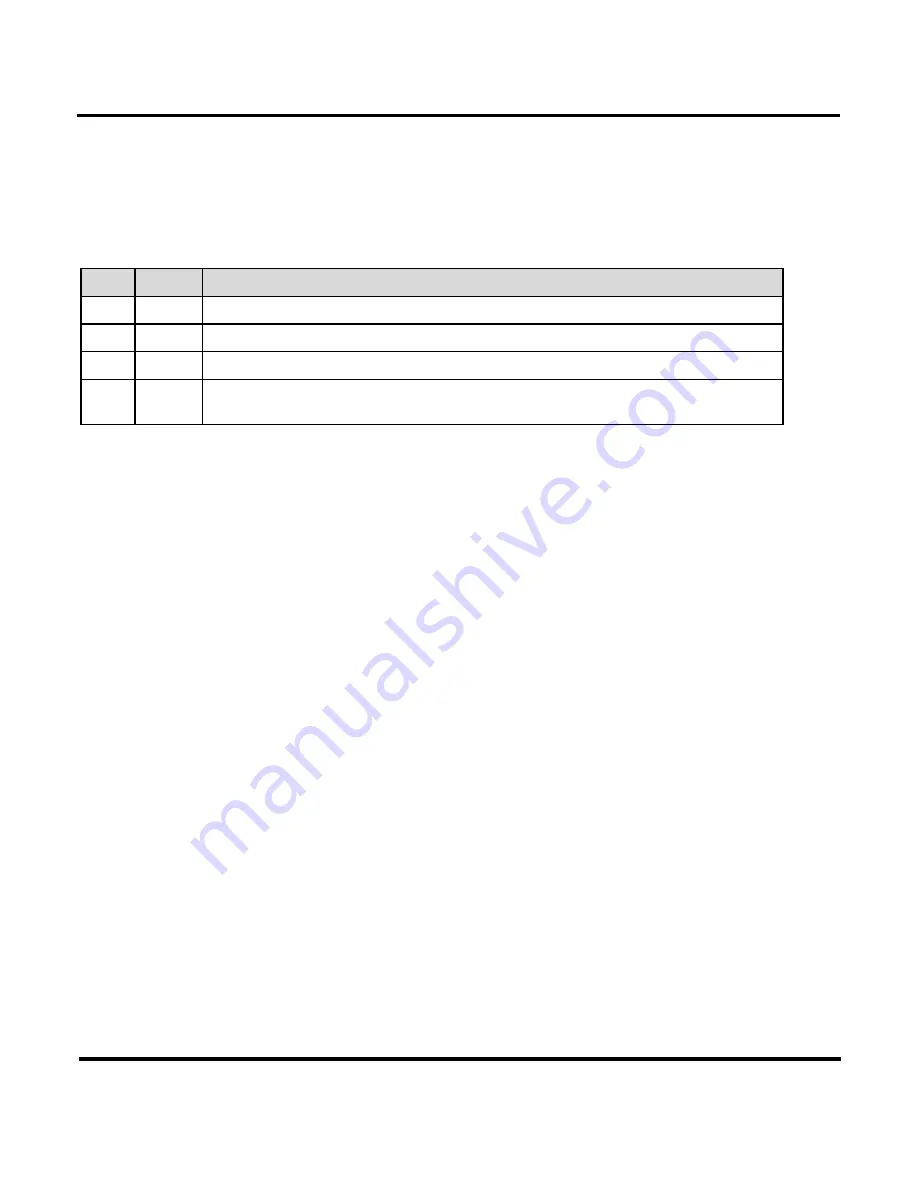
ADDENDUM 995-605, REV B
LW250 OMS MANUAL
Unitek Miyachi Lasers
Q
P. O. Box 5033
Q
Monrovia
Q
CA 91017-7133
Q
(626) 303-5676
Page 2of 4
Page 3-5, the following additional information should be inserted immediately prior to
the Warning in “Pin No. 34, Laser start:”
Duration of the laser output is dependent on the settings of REP (Pulse Repetition Rate) and SHOT
(Actual Shot Repetitions) as shown below (### represent numbers other than zero):
REP SHOT
Laser Output Duration
00
000
Single shot at each start signal input
00
###
Single shot at each start signal input
##
000
Laser beam repeatedly fires until laser stop signal is entered
##
###
Laser beam repeatedly fires until laser stop signal is entered or shot count
expires, whichever occurs first
Page 3-8, paragraph titled, Output Signal Specifications, EXT I/O (1) Connector -
Following Pin No. 11 - 12, Monitor trouble: add the following, and delete the existing Pin
No. 13 - 14.
Pin No. 13 -- 14, Monitor no light:
This signal is output for 50 msec when the NO-LIGHT
signal is indicated.
Pin No. 18 -- 19, External Input enable:
When this circuit is closed, the laser can receive
external signals.
Page 6-2, paragraph titled, Deionize - Change the existing READY and NOT READY
conditions to read as follows:
READY:
Above 3.00 megohms per cm
NOT READY:
Equal to or below 3.00 megohms per cm