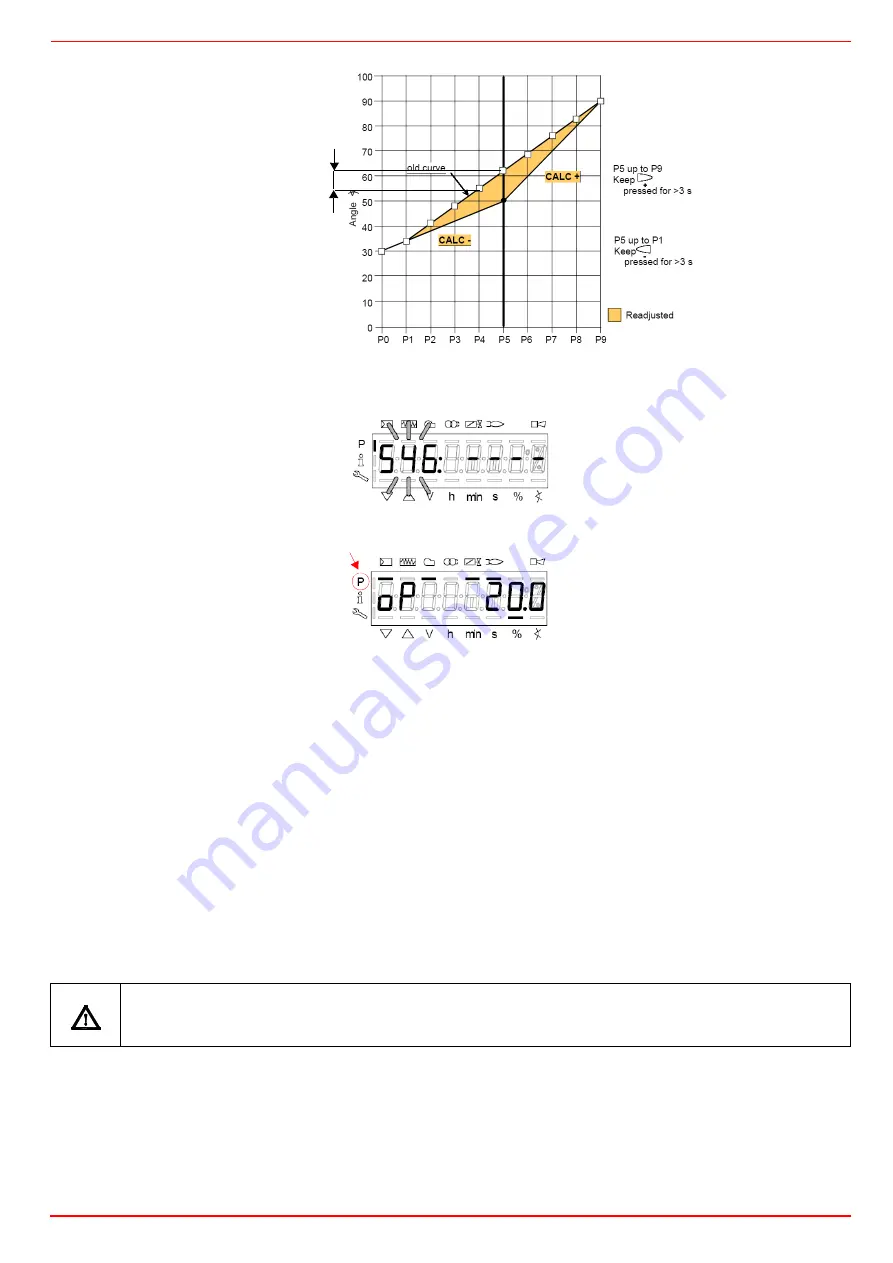
39
P5, keep pressing “-” unitl “Calc” is displayed. The curve will be processed again downwards point P1.
12 press “-” to go through the lower points and check the combustion values, if necessary change the points as described above.
13 By pressing ESC, at the end of the points adjusments, the parameter “
546”
(setting the maximum load) will be displayed; press
ENTER (InFo), then “+” until 100%, then press ENTER (InFo) again, ESC and then “+”.
14 The parameter “
545”
(setting the minimum load) is displayed: press ENTER (InFo), then “+” until 20%. Press ENTER, then press
ESC for three times. The message “oP” will be displayed as well as the load percentage at the burner is working on.
he hyphen related to the symbol “P” (highlited in the picture) will be off to show that the unit exited the programmig mode. The burner
will then work automatically, following the curve set.
.
Note1:
if the curvepoints settings is quit before end (by pressing ESC or for a faulty shutdown), the message “OFF UPr” (Start preven-
tion) will be diplayed until all the curvepoints will be set.
Note2:
if the gas flow rate at high flame point (maximum load) is changed by means of the pressure stabiliser, all the curvepoints must
be checked by going through the curve downwards and resetting them if necessary.
Note3:
if the point does not flash, it means thet the actuators have not reached the set position yet.
Note4:
if an error occurs causing a safety shutdwon during the processing of the curve, the processing itself will be interrupted.
Cold setting
The ”cold setting“ (without flame) can be performed only when all the curve points values are known (for instance, in case of replace-
ment).
When the burner is off, if you modify one curve set point, when the burner restarts the AZL2x shows OFF UPr
(OFF UPr0 or OFF UPr1 for LMV26). The LMV.. then, requires a new "warm" startup (see procedure paragraph
"Warm Setting”) by checking again all points of curve from P0 to P9.
deviation between two
following points: 25°max.
Fuel
An
golo
Summary of Contents for KPBY70
Page 33: ...PART III OPERATION 33 FLUIDICS 12AG 90Kg h...
Page 53: ......
Page 54: ......
Page 55: ......
Page 57: ...Service manual AZL2x LMV2x 3x Burner Management System M12916CD Rev 3 4 03 2023...
Page 64: ...8 Parameters level heating engineer...
Page 106: ...50 ERROR CODE TABLE...
Page 107: ...51...
Page 108: ...52...
Page 109: ...53...
Page 110: ...54...
Page 111: ...55...
Page 112: ...56...
Page 113: ...57...
Page 114: ...58...
Page 115: ...59...
Page 116: ...60...
Page 117: ...61...
Page 118: ...62...
Page 119: ...63...
Page 120: ...64...
Page 125: ......
Page 126: ......
Page 127: ......
Page 142: ......
Page 151: ......
Page 152: ......
Page 153: ...RWF50 2x RWF50 3x User manual M12922CB Rel 1 0 07 2012...
Page 168: ...16 Note Specifications and data subject to change Errors and omissions excepted...
Page 169: ...KM3 Modulator USER MANUAL M12927CA Rel 1 0 10 2020...
Page 170: ...M12927CA MOUNTING 2...