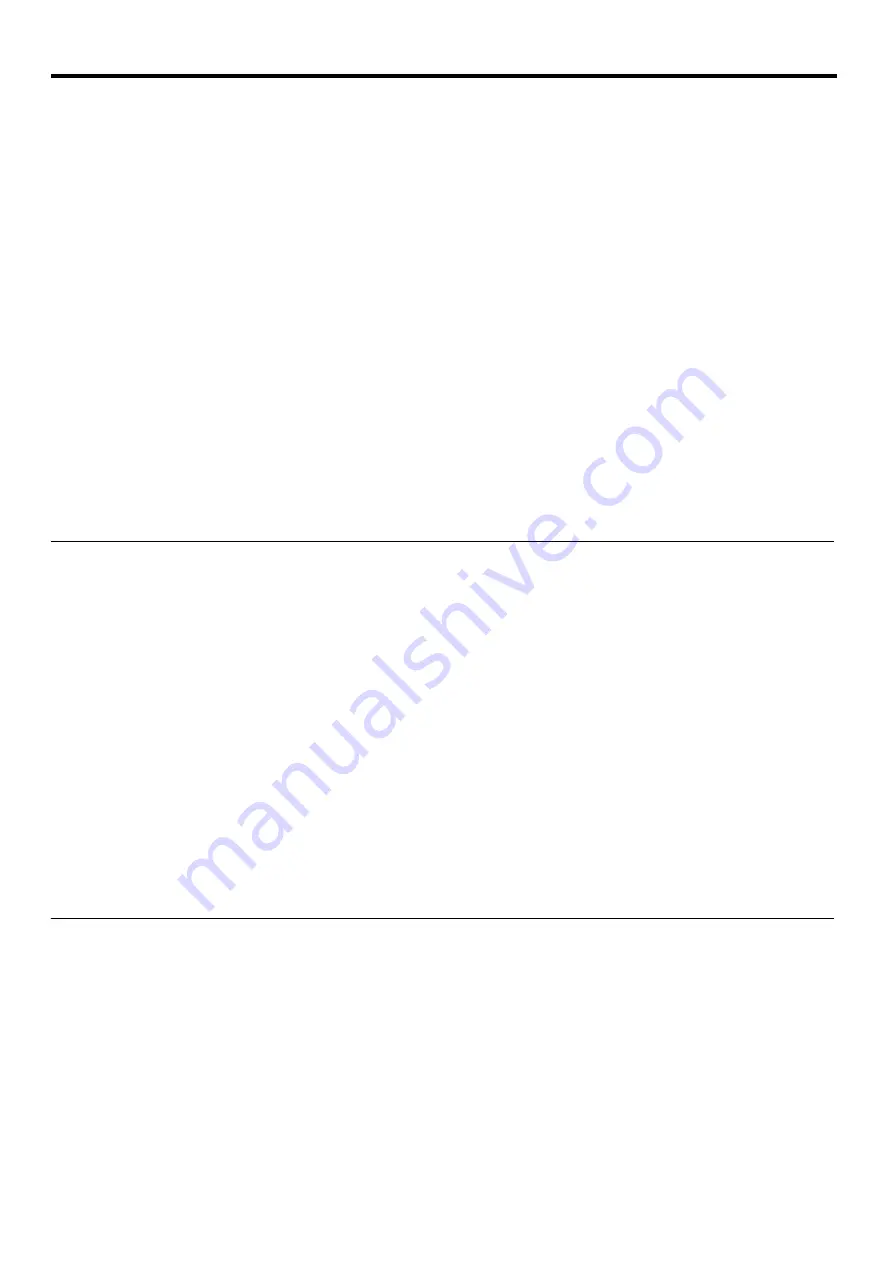
PART II: INSTALLATION
18
4.0 OIL TRAIN CONNECTIONS
The pump provided with the burner must be installed according to the hydraulic diagram.
Kral KF-10 pumps
Capacity: 500 l/h
Power consumption: 0.37 kW
Speed: 1500 rpm
Max outlet pressure: 10bar
Max inlet pressure: 2bar
NPSH: 2 mWC
For further details see the manifacturer documentation.
Cucchi pumps FMG25
Capacity: 1500 l/h
Power consumption: 0.75 kW
Speed: 1400 rpm
Max outlet pressure: 10bar
Max inlet pressure: 2bar
For further details see the manifacturer documentation.
4.1 About the use of fuel pumps
z
Do not use fuel with additives to avoid the possible formation over time of compounds which may deposit between the gear teeth,
thus obstructing them.
z
After filling the tank, wait before starting the burner. This will give any suspended impurities time to deposit on the bottom of the
tank, thus avoiding the possibility that they might be sucked into the pump.
z
On initial commissioning a "dry" operation is foreseen for a considerable length of time (for example, when there is a long suction
line to bleed). To avoid damages inject some lubrication oil into the vacuum inlet.
z
Care must be taken when installing the pump not to force the pump shaft along its axis or laterally to avoid excessive wear on the
joint, noise and overloading the gears.
z
Pipes should not contain air pockets. Rapid attachment joint should therefore be avoided and threaded or mechanical seal jun-
ctions preferred. Junction threads, elbow joints and couplings should be sealed with removable sg component. The number of jun-
ctions should be kept to a minimum as they are a possible source of leakage.
z
Do not use PTFE tape on the suction and return line pipes to avoid the possibility that particles enter circulation. These could depo-
sit on the pump filter or the nozzle, reducing efficiency. Always use O-Rings or mechanical seal (copper or aluminium gaskets) jun-
ctions if possible.
z
An external filter should always be installed in the suction line upstream the fuel unit.
4.2 Connecting the oil flexible hoses to the pump
To connect the flexible oil hoses to the pump, proceed as follows, according to the pump provided:
1
remove the closing nuts
A
(on the pump inlet) and
B
(from pump to the burner);
1
screw the rotating nut of the two flexible hoses on the pump
being careful to avoid exchanging the lines
: see the arrows marked
on the pump.
For further information, refer to the technical documentation of the pump.
Summary of Contents for KPBY70
Page 33: ...PART III OPERATION 33 FLUIDICS 12AG 90Kg h...
Page 53: ......
Page 54: ......
Page 55: ......
Page 57: ...Service manual AZL2x LMV2x 3x Burner Management System M12916CD Rev 3 4 03 2023...
Page 64: ...8 Parameters level heating engineer...
Page 106: ...50 ERROR CODE TABLE...
Page 107: ...51...
Page 108: ...52...
Page 109: ...53...
Page 110: ...54...
Page 111: ...55...
Page 112: ...56...
Page 113: ...57...
Page 114: ...58...
Page 115: ...59...
Page 116: ...60...
Page 117: ...61...
Page 118: ...62...
Page 119: ...63...
Page 120: ...64...
Page 125: ......
Page 126: ......
Page 127: ......
Page 142: ......
Page 151: ......
Page 152: ......
Page 153: ...RWF50 2x RWF50 3x User manual M12922CB Rel 1 0 07 2012...
Page 168: ...16 Note Specifications and data subject to change Errors and omissions excepted...
Page 169: ...KM3 Modulator USER MANUAL M12927CA Rel 1 0 10 2020...
Page 170: ...M12927CA MOUNTING 2...