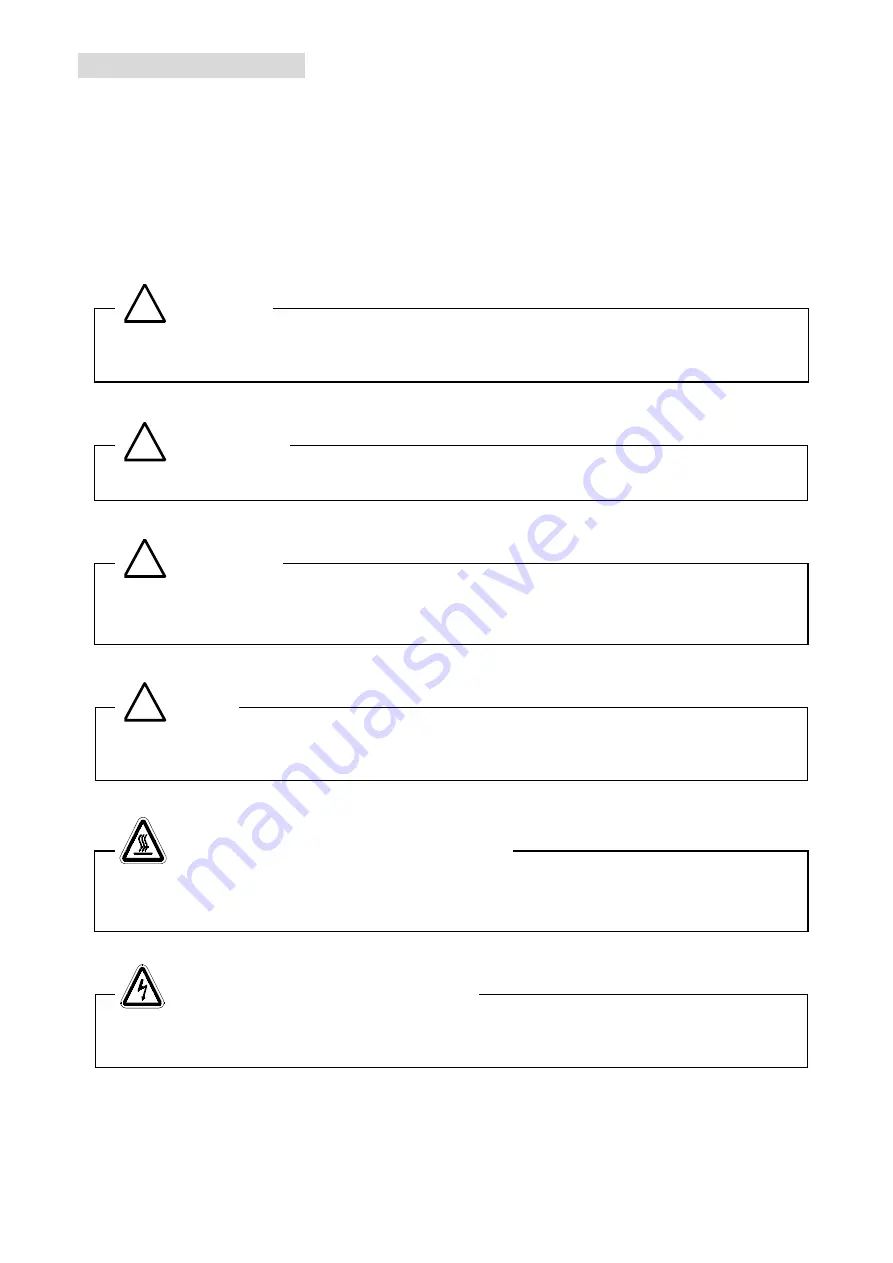
03
Using the Pump Safely
To ensure that the pump is handled correctly, read this section thoroughly before use.
This manual and the warning labels on the pump include safety icons as an aid to understanding
safety requirements.
These safety icons warn the operator and others of possible dangers and damage and should
always be followed.
・
Safety icons
The meanings of the safety icons are as follows.
Incorrect handling of the equipment is very likely to result in death or serious injury to the
operator.
Incorrect handling of the equipment may result in death or serious injury to the operator.
Incorrect handling of the equipment may result in light or medium injuries to the operator or
damage to the equipment.
Incorrect handling of the equipment may result in damage to the equipment and hinder its
correct operation.
Some parts of the pump may reach temperatures of 60°C or more during operation.
Touching such components may result in burns.
Always switch off the main power supply before installing electrical wiring or performing
any electrical work on the pump. Failure to do so may result in electric shock.
!
Danger
!
Warning
!
Caution
!
Note
Electric Shock Caution
High temperature Caution