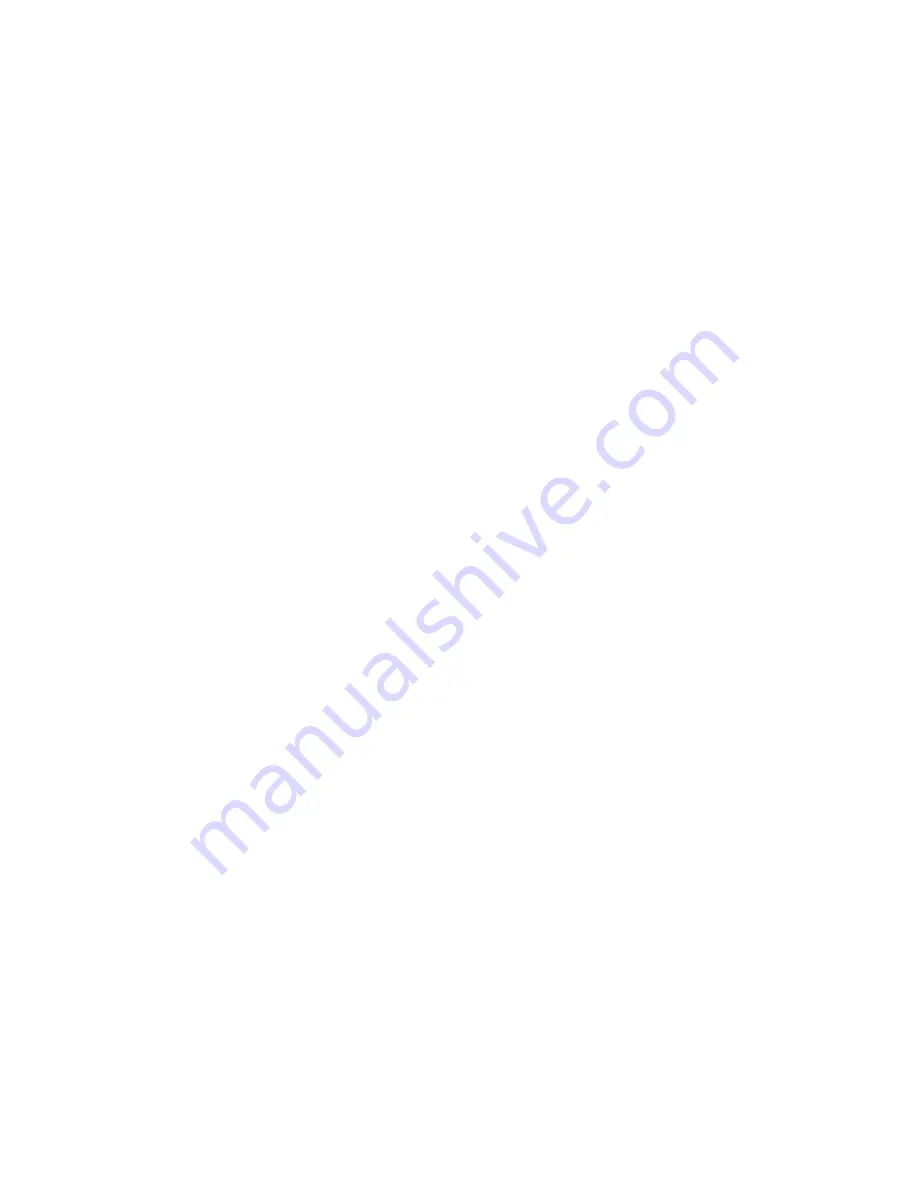
Property of Ultrasonic Power Corporation -
© 2018
Publication #181114
45
10.
Bypass and Purge Valves
– The bypass valve controls the console’s plumbing
settings and is located under the reservoir (weir) tank. Flow may be redirected in the
following configurations:
A. Reservoir (Weir) Tank Filtration- Ideal for the removal of surface
contaminants such as oils and other light particles. Surface contaminants
move from the system tank to the reservoir (weir) tank in order to be
filtered and pumped back into the system tank. When cleaning both large
and small parts, the amount of cleaning fluid transferred from the system
tank to the reservoir (weir) tank will vary. As a result, reservoir (weir) tank
overflow may occur when cleaning larger parts and reservoir (weir) tank
underflow may occur when cleaning smaller parts.
B. System Tank Filtration- Ideal for the removal of bottom dwelling
contaminants in the system tank. The reservoir (weir) tank is bypassed
and cleaning fluid is filtered as it circulates to and from the system tank.
This configuration is ideal for cleaning parts of varying sizes when it is
difficult to predict how much cleaning fluid will be present in the reservoir
(weir) tank. After numerous cleaning cycles, much of the dirt, oil, and other
contaminants are expected to move out of the system tank and into the
reservoir (weir) tank. This prolongs the life of the cleaning fluid by keeping
the system tank cleaner. In this configuration, the contents of the reservoir
(weir) tank may be drained without affecting the system tank by opening
the system drain valve.
C. Reservoir (Weir) Drain- The speed at which the system drains may be
controlled by positioning the bypass valve handle between configurations
B and C. This configuration opens all lines between the two tanks and
may result in reservoir (weir) overflow if the system drain is not open.
Utilize the reservoir (weir) tank’s overflow for additional flexibility.
The purge valv
e enables operators to prime the system’s pump in low feed
conditions. Prolonging the time between maintenance checks and extending the life
of the detergent, the purge and bypass valves respectively decrease the console’s
overall downtime.
11.
Cleaning
- Place materials to be cleaned into the cleaning tank. Be sure that all
parts and components are fully submerged into the cleaning solution. Check to be
sure that no air pockets are present on the item(s) being cleaned, as the cavitation
process will only be e
ffective where water contacts the part’s surface. It may be
necessary to rotate the part while submersed to allow air to escape. Some initial
testing will help determine the proper settings for the optimum time and
temperature.
For
most
applications,
due
to
the
extreme
efficiency
of the unit, only 2 to 3 minutes of immersion time is required to thoroughly clean the
average part. These applications include removing machining oils and small
particles. For application involving baked on carbon or calcium and mineral
deposits, longer times and higher temperatures may be required.
Summary of Contents for UP3218
Page 23: ...Property of Ultrasonic Power Corporation 2018 Publication 181114 23 Figure 3 Plumbing Diagram...
Page 40: ...Property of Ultrasonic Power Corporation 2018 Publication 181114 40 Figure 6 Plumbing Diagram...
Page 58: ...Property of Ultrasonic Power Corporation 2018 Publication 181114 58 Figure 9 Plumbing Diagram...
Page 75: ...Property of Ultrasonic Power Corporation 2018 Publication 181114 75 Figure 12 Plumbing Diagram...
Page 91: ...Property of Ultrasonic Power Corporation 2018 Publication 181114 91 Figure 15 Plumbing Diagram...