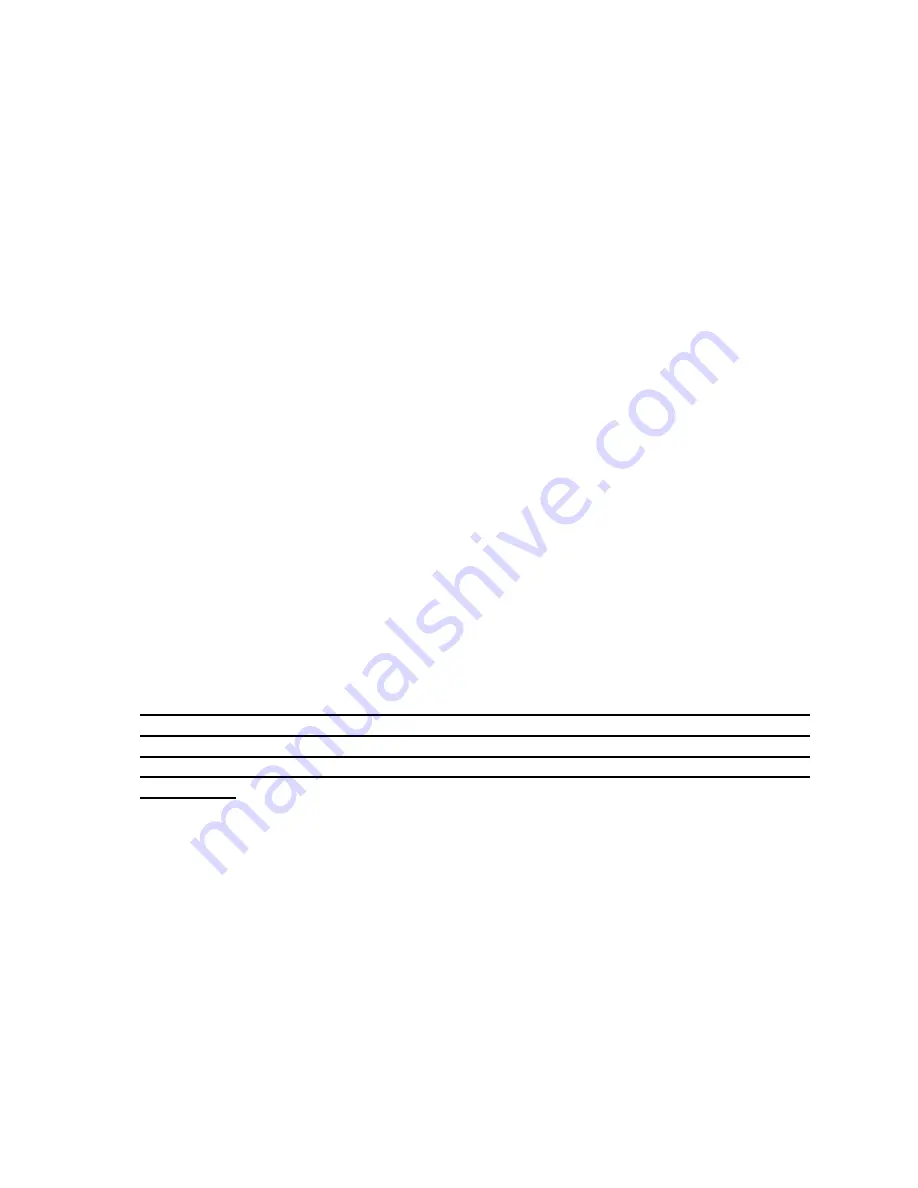
Property of Ultrasonic Power Corporation -
© 2018
Publication #181114
147
5.
Power On
– Turn on the ultrasonic start switch. The ultrasonic generators will start
the ultrasonic action in the tank. All installed generator circuits are controlled by one
switch on the control panel. The power intensity should be set to 80% and adjusted
after testing parts. If UPC performed a cleaning test, consult the test report or
contact your sales representative.
6.
System Degassing
-
If new water and detergent has been added allow the system
to run through one cycle. This allows the water in the cleaning tank to properly
degas (the water comes to oxygen equilibrium). The de-gassing process removes
unwanted air molecules from the cleaning tank, thus maximizing the efficiency of
the cavitation/cleaning process.
7.
Liquid Overtemp Protection
– The liquid overtemp protection’s primary purpose is
to turn off the system when operated above 180˚F. When the system is operated
above 180˚F, liquid overtemp indicator will turn on. Liquid overtemp indicator will
stay on until the system reaches below the pre-set (Pre-
set at 180˚F) temperature.
Contact UPC if system does not turn on when temperature reaches below the pre-
set temperature.
8.
Cleaning
- Place materials to be cleaned into the cleaning tank. Be sure that all
parts and components are fully submerged into the cleaning solution. Check to be
sure that no air pockets are present on the item(s) being cleaned, as the cavitation
process will only be effective where water contacts the part’s surface. It may be
necessary to rotate the part while submersed to allow air to escape. Some initial
testing will help determine the proper settings for the optimum time and
temperature.
For
most
applications,
due
to
the
extreme
efficiency
of the unit, only 2 to 3 minutes of immersion time is required to thoroughly clean the
average part. These applications include removing machining oils and small
particles. For application involving baked on carbon or calcium and mineral
deposits, longer times and higher temperatures may be required.
When first learning the capabilities of this system, do no leave
items
unattended in the wash tank for long periods. The system may damage
surfaces if allowed to remain in the ultrasonic bath for extended periods of
time. Longer cleaning times can be used after thorough testing has been
completed.
Do not place items to be cleaned directly on the tank bottom. The bottom is
essentially a high frequency speaker so contact may hinder the acoustic
propagation. Use UPC approved baskets or fixtures that are designed to minimize
acoustical losses and or damage to the tank bottom and the transducers. Heavy
items should always be suspended or placed on a work rest. In cases when a work
rest is required, consult UPC regarding a proper design for your application.
Summary of Contents for UP3218
Page 23: ...Property of Ultrasonic Power Corporation 2018 Publication 181114 23 Figure 3 Plumbing Diagram...
Page 40: ...Property of Ultrasonic Power Corporation 2018 Publication 181114 40 Figure 6 Plumbing Diagram...
Page 58: ...Property of Ultrasonic Power Corporation 2018 Publication 181114 58 Figure 9 Plumbing Diagram...
Page 75: ...Property of Ultrasonic Power Corporation 2018 Publication 181114 75 Figure 12 Plumbing Diagram...
Page 91: ...Property of Ultrasonic Power Corporation 2018 Publication 181114 91 Figure 15 Plumbing Diagram...