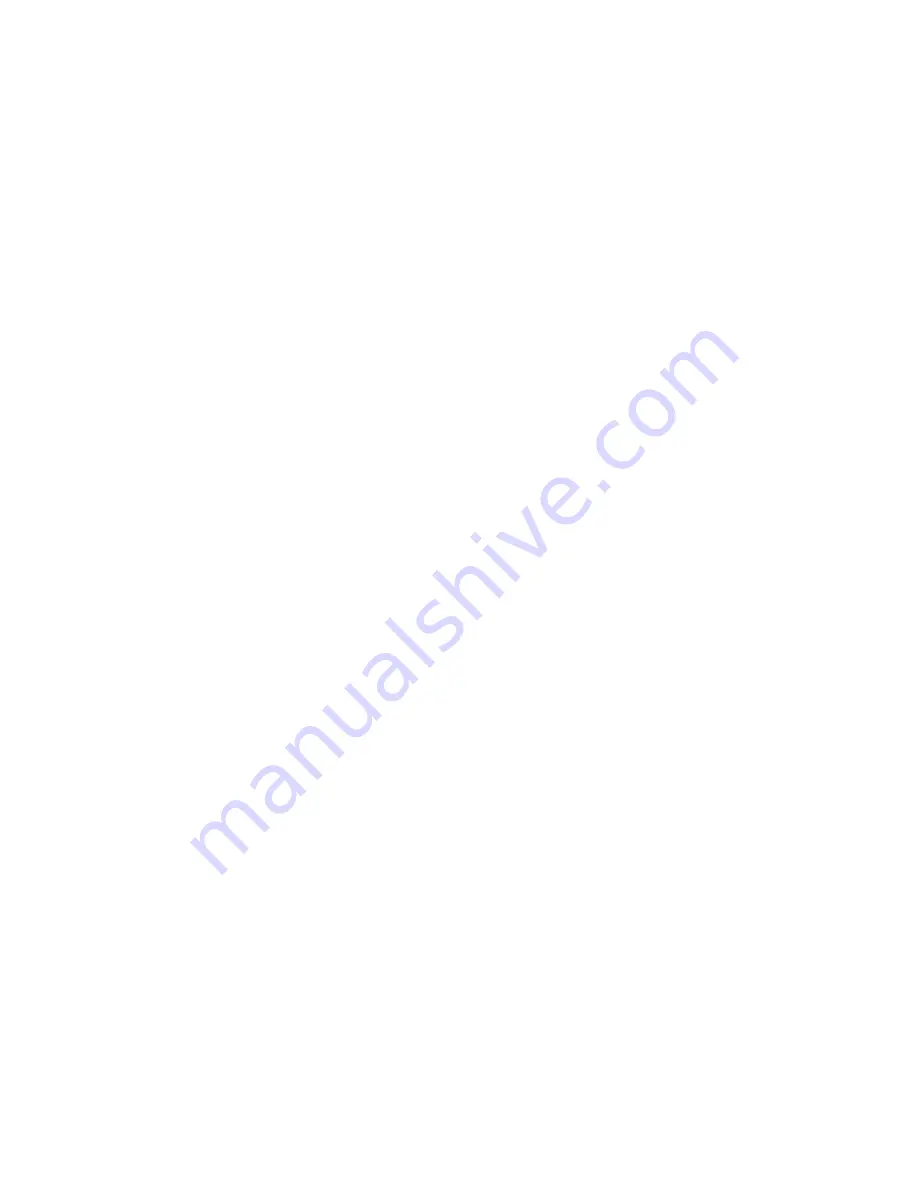
Property of Ultrasonic Power Corporation -
© 2018
Publication #181114
163
4.
Adding Chemicals
– Use the mixture rate recommended by the detergent
manufacturer. After cleaning one or two items, you may choose to increase the
chemical ratio. The amount of chemical will be based on the condition of the water
being used and how much contamination is to be removed. Detergents that are
used in this ultrasonic cleaning system must be compatible with 304 and 316L
stainless steel.
You will void the warranty if chemical attack to the stainless
steel occurs.
5.
Power On
– Turn on the ultrasonic start switch. The ultrasonic generators will start
the ultrasonic action in the tank. All installed generator circuits are controlled by one
switch on the control panel. The power intensity should be set to 80% and adjusted
after testing parts. If UPC performed a cleaning test, consult the test report or
contact your sales representative.
6.
System Degassing
-
If new water and detergent has been added allow the system
to run through one cycle. This allows the water in the cleaning tank to properly
degas (the water comes to oxygen equilibrium). The de-gassing process removes
unwanted air molecules from the cleaning tank, thus maximizing the efficiency of
the cavitation/cleaning process.
7.
Liquid Overtemp Protection
– The liquid overtemp protection’s primary purpose is
to turn off the system when operated above 180˚F. When the system is operated
above 180˚F, liquid overtemp indicator will turn on. Liquid overtemp indicator will
stay on until the system reaches below the pre-set (Pre-
set at 180˚F) temperature.
Contact UPC if system does not turn on when temperature reaches below the pre-
set temperature.
8.
Pump and filter system -
The pump and filter system’s primary purpose is to filter
out contaminants from the liquid in order to extend the life of the detergent and
lower operating costs. As agitation will hinder cavitation, it is recommended that the
operator not use the pump and filter during cleaning. If it is absolutely necessary,
the lowest flow rate permissible is recommended. The system is fitted with a purge
valve that enables operators to prime the system’s pump in low feed conditions.
Some users will operate the system at 100% between cleaning cycles or work
shifts.
9.
Cleaning
- Place materials to be cleaned into the cleaning tank. Be sure that all
parts and components are fully submerged into the cleaning solution. Check to be
sure that no air pockets are present on the item(s) being cleaned, as the cavitation
process will only be effective where water contacts the part’s surface. It may be
necessary to rotate the part while submersed to allow air to escape. Some initial
testing will help determine the proper settings for the optimum time and
temperature.
For
most
applications,
due
to
the
extreme
efficiency
of the unit, only 2 to 3 minutes of immersion time is required to thoroughly clean the
average part. These applications include removing machining oils and small
particles. For application involving baked on carbon or calcium and mineral
deposits, longer times and higher temperatures may be required.
Summary of Contents for UP3218
Page 23: ...Property of Ultrasonic Power Corporation 2018 Publication 181114 23 Figure 3 Plumbing Diagram...
Page 40: ...Property of Ultrasonic Power Corporation 2018 Publication 181114 40 Figure 6 Plumbing Diagram...
Page 58: ...Property of Ultrasonic Power Corporation 2018 Publication 181114 58 Figure 9 Plumbing Diagram...
Page 75: ...Property of Ultrasonic Power Corporation 2018 Publication 181114 75 Figure 12 Plumbing Diagram...
Page 91: ...Property of Ultrasonic Power Corporation 2018 Publication 181114 91 Figure 15 Plumbing Diagram...