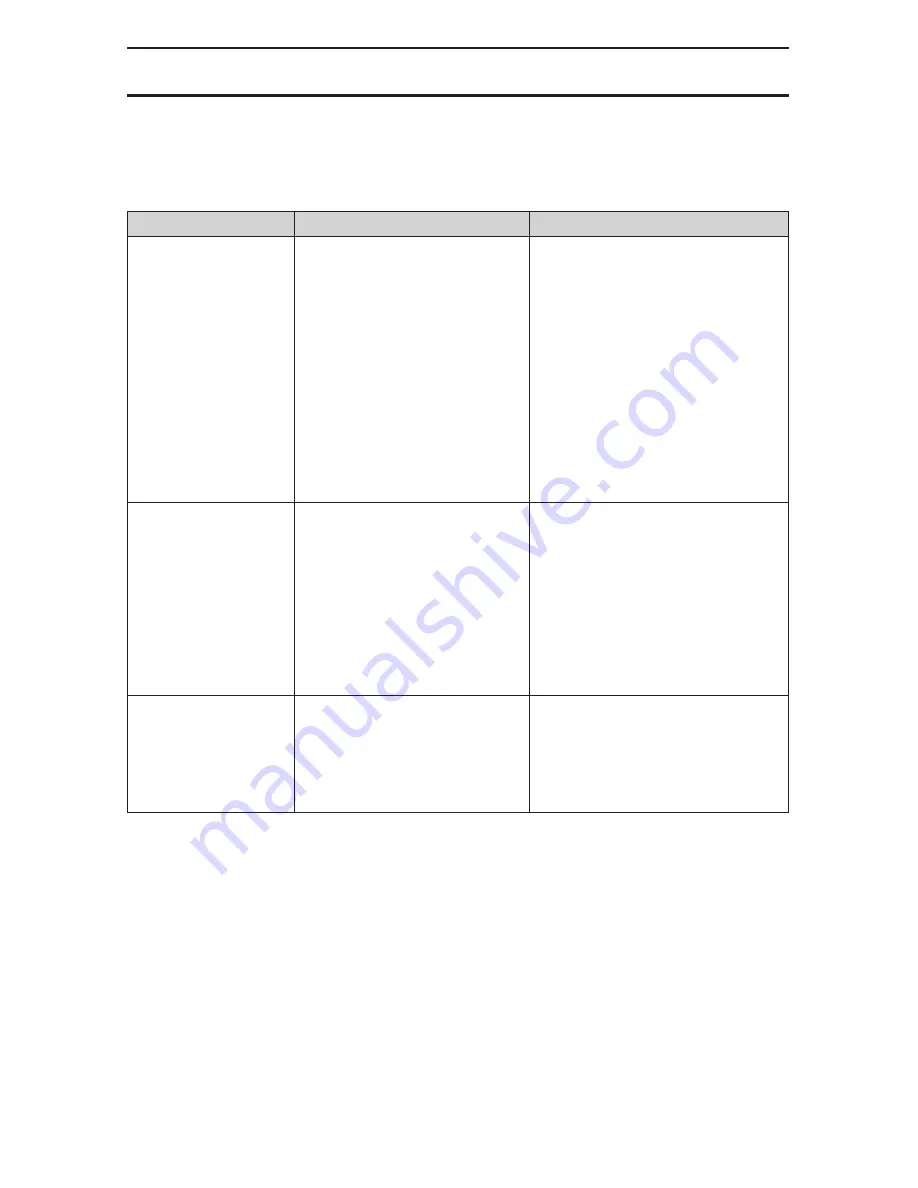
20
SAFETY AND OPERATING INSTRUCTIONS
89200009
SECTION 8: MAINTENANCE AND TROUBLESHOOTING
Contact tips and nozzles should be cleaned frequently. Spatter buildup may cause bridging between nozzle and
tip. This could cause electrical shorting between the nozzle and work piece as well as poor or improper gas flow.
Regularly inspect the conductor tube, handle, cable, and other parts of the MIG Gun for abrasion, cuts, or undue
wear. Replace or repair any parts found deficient.
Problem
Possible Cause
Corrective Action
Wire feed inconsistent or not
smooth
1. Loose contact tip or diffuser.
1. Tighten contact tip and diffuser plier
tight.
2. Excessively worn contact tip.
2. Replace contact tip.
3. Spatter buildup on end of contact
tip.
3. Clean or replace contact tip.
4. Sharp bends or kinks in conduit.
4. Straighten or replace conduit.
5. Dirty or plugged conduit.
5. Replace conduit.
6. Conduit pulled back from diffuser.
6. Reposition conduit and tighten front set
screw.
7. Machine improperly adjusted.
7. Reset machine per machine and wire
manufacturers’ recommendations.
MIG Gun is running hot
1. Loose contact tip or diffuser.
1. Tighten contact tip and diffuser plier
tight.
2. Loose power connections.
2. Inspect complete gun for loose
connections and repair.
3. Loose or undersize ground cable or
ground clamp.
3. Tighten or replace as required.
4. Operating gun above recommended
amperage rating.
4. Readjust machine to correct setting for
size of gun being used.
Porous weld
1. Poor or improper gas flow.
1. Check gas flow out of gun nozzle. Check
for leaks or restrictions in gas hoses and
connections.
2. Dirty or contaminated wire.
2. Change wire.
3. Base metal contaminated.
3. Replace base metal.
Summary of Contents for Spray Master Series
Page 6: ...iv This page intentionally blank...
Page 29: ...SAFETY AND OPERATING INSTRUCTIONS 23 89200009 This page intentionally blank...
Page 34: ...28 SAFETY AND OPERATING INSTRUCTIONS 89200009 This page intentionally blank...
Page 35: ...SAFETY AND OPERATING INSTRUCTIONS 29 89200009 This page intentionally blank...