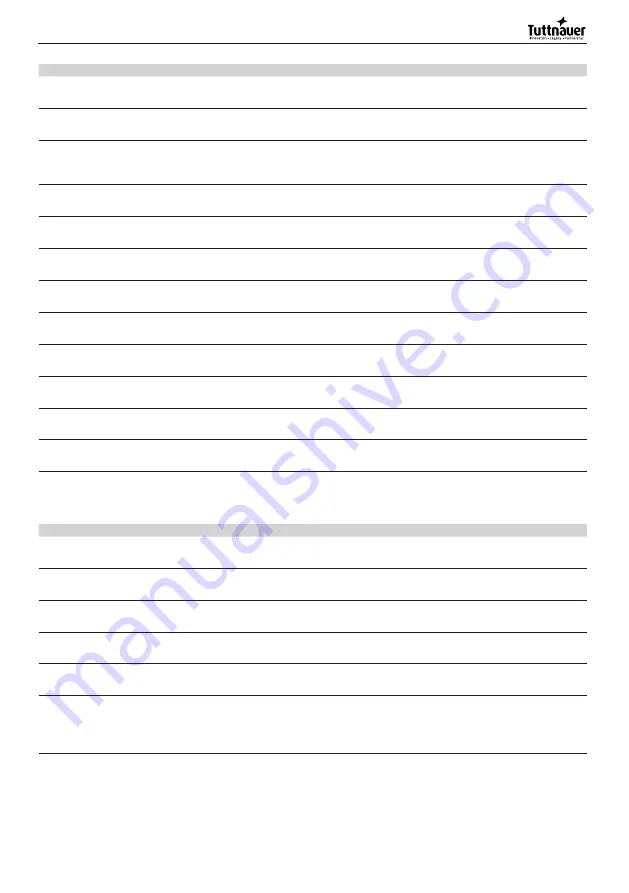
51
English
ALARM
DESCRIPTION
ACTION
E51 PROBE 2 BROKEN
Chamber probe PT1000-2 (control) might be
broken or disconnected.
Press RESET
If it persists, call the technician.
E52 AIR PROBE BROKEN
Air probe PT1000-3 might be broken or
disconnected.
Press RESET
If it persists, call the technician.
E53 CHAMBER T. DIFF
A temperature difference between the
probes in the chamber has been detected
too high.
Press RESET
If it persists, call the technician.
E66 NO HEATING
There is a problem with water heating.
Press RESET
If it persists, call the technician.
E67 CONDENSER LEVEL
The water inside the steam condenser has
reached the maximum level allowed.
Press RESET
If it persists, call the technician.
E70 PUMP PRESSURE
There could be water leaks.
Press RESET
If it persists, call the technician.
E71 HEPA FILTER
The HEPA filter might be dirty or clogged.
Check it.
Press RESET
If it persists, call the technician.
E75 PRODUCT 1 EMPTY
Chemical liquid tank 1 is empty.
Add liquid.
Press RESET
If it persists, call the technician.
E76 PRODUCT 2 EMPTY
Chemical liquid tank 2 is empty.
Add liquid.
Press RESET
If it persists, call the technician.
E77 PRODUCT 3 EMPTY
Chemical liquid tank 3 is empty.
Add liquid.
Press RESET
If it persists, call the technician.
E80 SPRAY ARM LOCKED
The spray arm marked in red on display is
locked. Remove it and clean.
Press RESET
If it persists, call the technician.
E89 NO DISINFECTION
The minimum value of A0 was not reached
and the load is still contaminated.
Press RESET
If it persists, call the technician.
9.10 Warnings table
WARNING TYPE
DESCRIPTION
ACTION
LIQUID RESERVE
PRODUCT 1
Product 1 is in reserve or may be empty.
Add the product 1
LIQUID RESERVE
PRODUCT 2
Product 2 is in reserve or may be empty.
Add the product 2
LIQUID RESERVE
PRODUCT 3
Product 3 is in reserve or may be empty.
Add the product 3
REQUEST
MAINTENANCE
Contact customer service or the dedicated
technical assistance for periodic maintenance.
Press RESET
REQUEST
VALIDATION
Contact customer service or the dedicated
technical assistance for periodic validation.
Press RESET
REFILL
SALT TANK
1- Take out the basket
2- Unscrew the cap of the salt tank
3- Fill the salt tank
4- Screw the cap of the salt tank
Press RESET
For 5 seconds