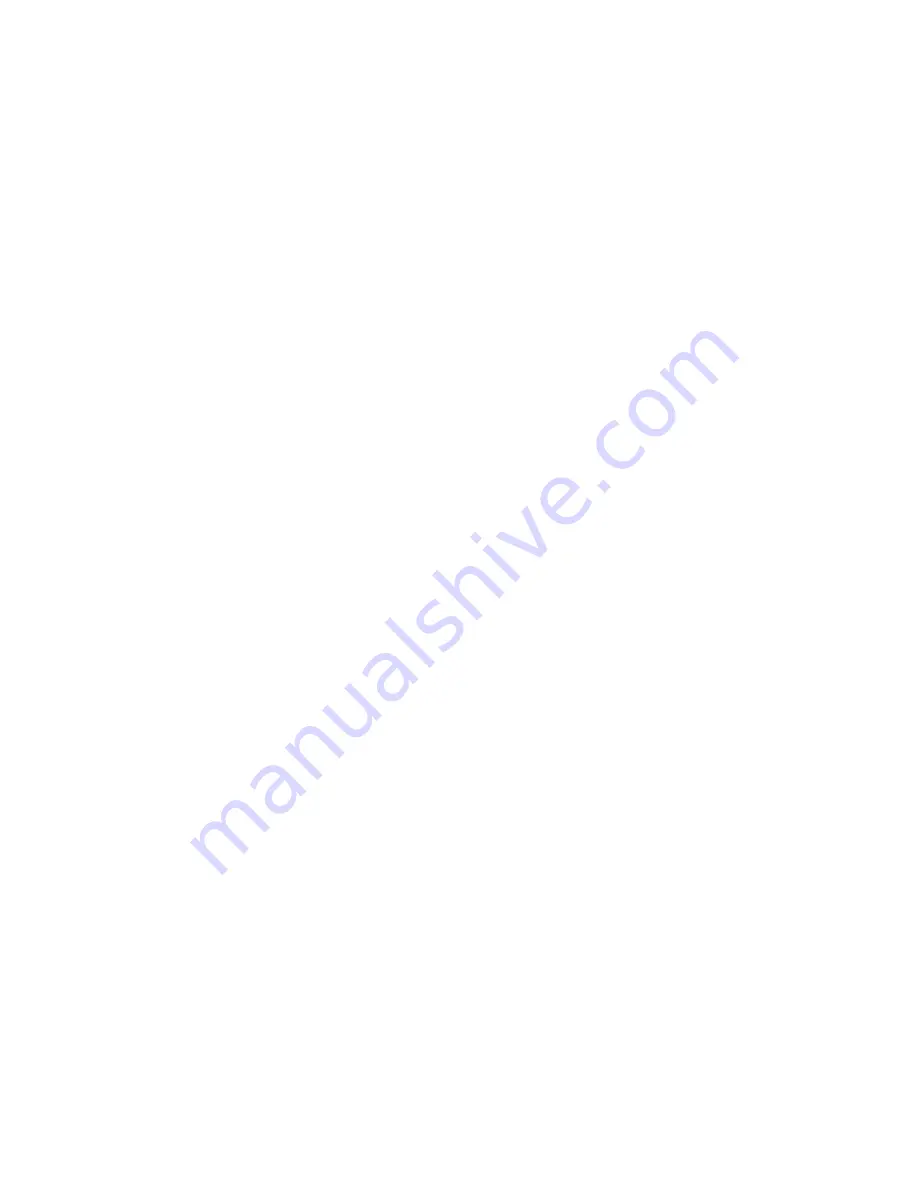
17
KT-Series pumps can accumulate .75 - 2.5 gallons (2.8 - 9.5 Liters) of water (depending on the model) in
the reservoir before the water level reaches the oil line pickup where it could circulate through the pump. If
water or other condensate collects in the oil reservoir, the water should be drained before the level reaches
the oil line pickup. To drain water from the pump, crack the oil drain valve and leave it open until any free
water accumulation has drained out. Drain the water as often as necessary. Never shutdown the KT pump
if oil is wet with water since it can separate out and cause damage on startup. Always clean up the oil first
using gas ballast to remove water vapor before shutting down.
6.6 GAS BALLAST
The gas ballast valve is shown in Figure 1 of this manual. Gas ballast is used while the pump is running,
to prevent internal condensation of oil insoluble vapors such as water, alcohol or acetone and to quiet the
hydraulic noise when running the pump at blank-off conditions.
When gas ballast is used, the ultimate pump pressure increases, more oil mist is created in the pump
discharge, and power consumption increases slightly (within the standard motor rating). Pump noise can be
generally eliminated by using a small flow of gas ballast with only slight increase in ultimate pump pressure.
Continuous use of gas ballast is recommended where the process pressure requirements can be met with
the gas ballast valve open; otherwise, intermittent use of gas ballast between process cycles is suggested.
If use of gas ballast at neither of these times is tolerable; it is advisable to run the pump using full gas
ballast, when process work is not being done such as overnight.
Use the gas ballast valve as follows:
1.
CONTINUOUS GAS BALLAST —
With the pump operating, open the gas ballast valve until the ultimate
pressure is slightly below that needed for the process. Operate the pump in this manner continuously to
aid in preventing oil contamination.
2.
INTERMITTENT GAS BALLAST DURING PROCESSING —
With the pump operating, fully open the
gas ballast valve during periods when this will not affect the process (work preparation, recycling, etc.).
This will aid in cleaning the oil.
3.
CONTINUOUS GAS BALLAST WHEN NOT PROCESSING —
With the pump operating, but isolated
from the process, fully open the gas ballast valve. If convenient, operate the pump overnight in this
manner to clean badly contaminated oil. Gas ballast will remove vapor contamination but will not
remove solids such as varnish. If it is necessary to clean the oil using gas ballast in the short period, the
time needed can be estimated as follows: Open the gas ballast valve fully and operate the pump for a
short period (15 to 20 minutes). Close the gas ballast valve for 1 to 2 minutes and observe the pressure
change. Use the “pressure change versus time” as a rough guide to estimate the total time required to
obtain the desired blank-off pressure.
6.7 STALLING
If the pump stalls at any time, it may be due to loose belts, lack of lubrication caused by failure of the oil
circulating pump, badly contaminated oil, coating build up or foreign matter in the pump or oil line strainer
(KT-500 and KT-850). If the pump cannot be turned over freely by hand after cooling, there is foreign matter
in the pump and the inside of the pump must be cleaned.
Sometimes a process related coating build up can be removed by soaking the pump with the proper solvent
(Turning by hand) – check with Tuthill Vacuum & Blower Systems. Inspecting the inside of the pump is
covered under the
Disassembly
section.
6.8 PUMP LEAKS
If the pump is suspected of having an air leak, after eliminating oil contamination as the causes of poor
performance, use a plastic sealing compound to seal over suspected areas, such as joints, connections
Summary of Contents for KINNEY 850D
Page 29: ...29 NOTES ...
Page 35: ...35 NOTES ...