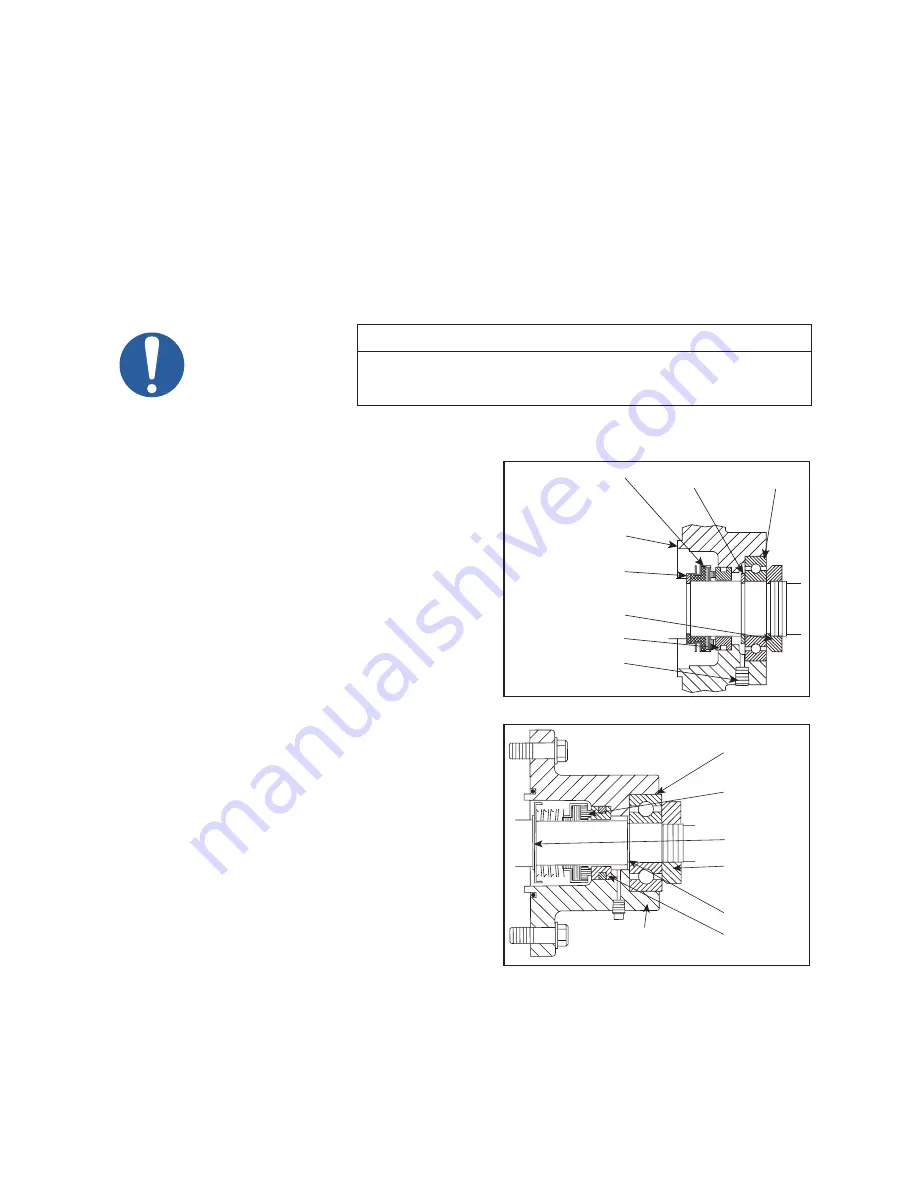
23
To inspect the discharge valves, proceed as follows:
1. Drain oil from the pump and remove the separator housing cover.
2. Unscrew the air/oil separator from the top of the valve deck cover.
3. Remove the capscrews from the valve deck cover and remove the cover.
4. The valve chamber will contain a quantity of oil. Drain the chamber by removing the pipe plug on the
closed head end of the cylinder. As an alternative, scoop the oil out of the valve cavity with a small
container. Remove cap screws in valve hold down plates and lift out valve plates with valves.
5. Inspect the valves by snapping the valve disk or lower valve spring away from the valve seat to check
for spring tension and mechanical defects. Inspect the sealing surfaces for dirt or other foreign material.
Check that the disk or lower valve spring has not warped (dish shape) as they must be flat for full
contact. If a more careful inspection is required, remove the cap screw(s) holding the valve together.
When reassembling the valve, replace valve components in exactly the same position as before.
6. Reinstall the valves in the pump.
NOTE
Caution must be used to insure no screws or objects enter the piston
chamber. It is recommended to replace the locking screws with new lock
screws when re-installing the valves and plates.
8.2 SHAFT SEAL ASSEMBLY
Under normal conditions, the shaft seal (See Figures 8
and 9) has a long trouble-free life. It may become worn
or scratched on the sealing face by dirty sealing oil which
also lubricates the shaft seal, or it may be damaged by
excessive heat due to poor lubrication.
If oil drips from the shaft seal and bearing housing, it is
an indication that the shaft seal should be inspected, and
replaced as necessary. The drain plug of the shaft seal
and bearing housing should be removed as long as oil is
leaking past the shaft seal. If oil which has leaked from
the shaft seal is allowed to drain through the bearing it
will wash the grease from the bearing and cause it to fail.
To inspect the seal:
1. Remove the belt guard and belts.
2. Remove the pump pulley and drive key from the
shaft.
3. Remove the shaft bearing and housing:
(a) Remove the outboard bearing retainer nut from
the shaft.
(b) Remove the capscrews holding the bearing
housing and remove it.
4. Inspect the face of the running surface for dirt,
scratches, or grooves, which might cause leaks into
the pump. A smooth shining carbon face indicates a
good seal. A crease across the sealing ring, a dent,
or scratch in the running face makes a direct leak
through the seal. Cracks or hardening of the rubber
parts indicate that they were exposed to excessive
operating temperatures and need replacement.
Figure 8 - KT-150 Shaft Seal & Bearing Housing
SHAFT SEAL AND
BEARING HOUSING
MECHANICAL
SHAFT SEAL
BEARING
BACK-UP RING
BALL
BEARING
SEAL
BACK-UP RING
MATING RING
LOCKNUT
DRAIN PLUG
Figure 9 - KT-300, KT-500, KT-850 Shaft Seal
& Bearing Housing
BALL BEARING
MATING RING
LOCKNUT
BEARING
BACK-UP RING
SHAFT SEAL
BEARING HOUSING
MECHANICAL
SHAFT SEAL
SHAFT SEAL
BACK-UP RING
Summary of Contents for KINNEY 850D
Page 29: ...29 NOTES ...
Page 35: ...35 NOTES ...