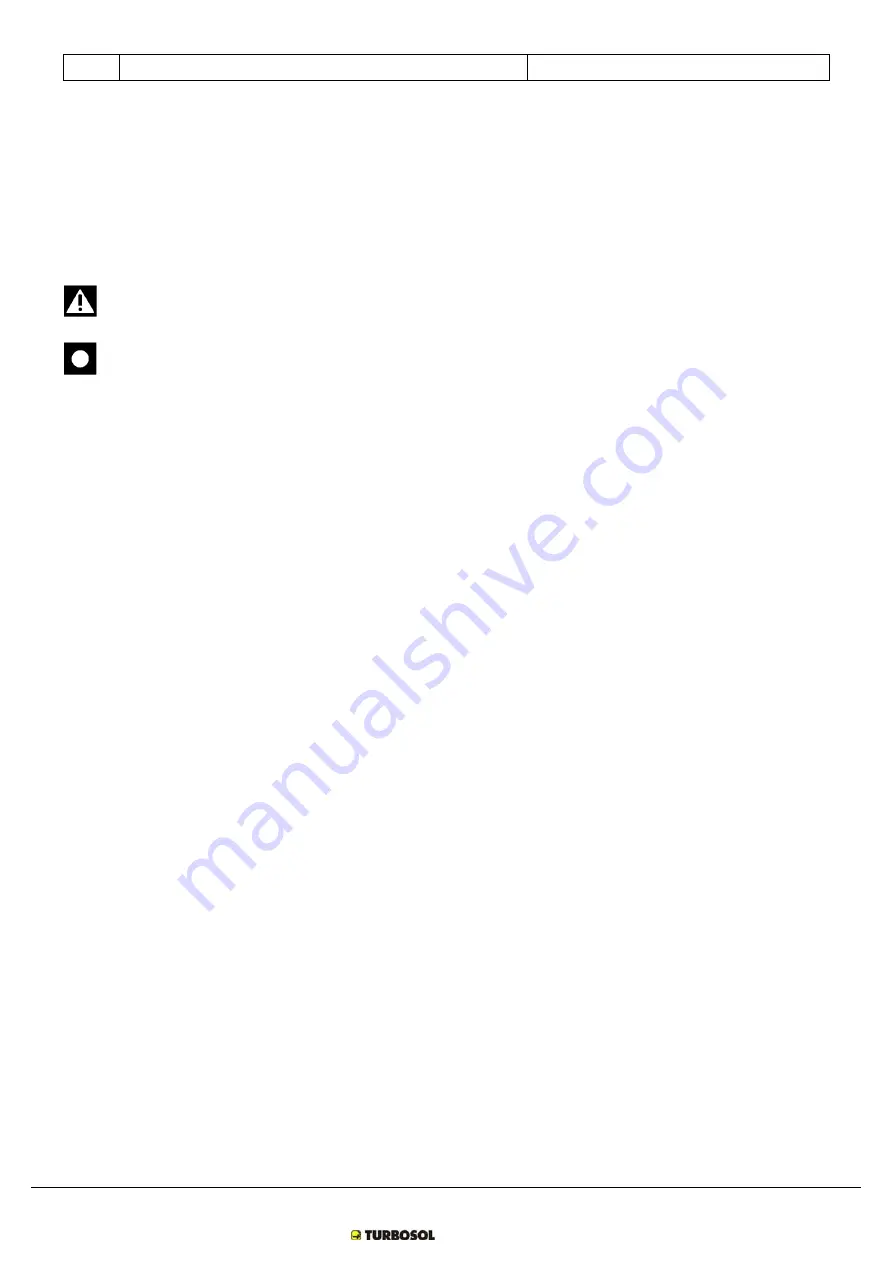
EN
BM 30
IS13/02 - 561291
7 - USE AND OPERATION
Cap. 7 -
Pag. 7/13
THIS MANUAL IS PROPERTY OF
-
ANY TOTAL OR PARTIAL REPRODUCTION IS STRICTLY FORBIDDEN
The pre-heat phase starts automatically once the password is entered. The LED on the console indicating spark plugs pre-
heating switches on. Wait for this LED to switch off. Exit this phase and go back using the ON/OFF start key. This phase is set
to last 11 seconds, regardless of the external environmental conditions. Start the engine once pre-heat is completed.
The flow rate ratio (corresponding to number of pumps per minute) is shown on the display's top-right part, when pumping is
activated. This is important in the event of malfunctionings.
The partial operation time of the started work session is shown bottom-left.
- Pour the grout in the hopper.
- Activate the mix using the ON/OFF key. The mixer's rotation direction can be reversed. Press the ON key with the relative
ON/OFF key engaged; go back to normal rotation direction by releasing it.
Ensure material outflow does not create dangers in the unload area before starting pumping.
During warm-up period do not use the machine at maximun output. Let the machine work approx. 10 min.
(depending on ambient temperature) in order to warm the hydraulic oil.
- Using the manual acceleratore, accelerate the engine slightly up to bottom ramp and activate pumping by pressing the
ON/OFF key; act on the accelerator lever again, if required.
Press the pumping reverse key to suck the mix: the mix is sucked by piping and re-introduced in the hopper. (this is useful to
depressurise the piping line, e.g. when clogged). Press the pumping reverse key again to go back to pumping.
- Rotate the hydraulic pump's adjustment handwheel to obtain a value of about 6 - 10 pumps per minute (always displayed top-
right of control board's display).
- If the STOP "grid safety intervention" indicators switch-on, it means the hopper's safety grid is open and the grid's safety
device has intervened: hydraulic supply is interrupted and the controls are disabled. Close the grid and re-start pumping by
pressing the ON/OFF button, to restore operation.
The operator must check the pumping circuit manometer during the first few pumping cycles, for best perception of relation
between the effective work pressure and the maximum pressure.
The effective work pressure (on hydraulic circuit oil) varies based on used mix and layout of the piping line. The manometer
indicates the hydraulic cylinders' working pressure during pumping. The manometer indicates the hydraulic jacks' (controlling
the S valve) working pressure during S valve exchange; the manometer indicates peak pressure for a brief moment, when
jacks reach end run.
When the pumping barrels' inlets and/or wear plate surface from the hopper full of grout, pour the concrete and start pumping
at low flow rate.
- Activate the grid's electric vibrator using the ON/OFF key. The electric vibrator is working when the indicator is on.
Flow rate can be increased to wanted value using the flow rate regulator, when the first concrete reaches the piping line's
outfeed.
The auxiliary circuit manometer indicates the services' work pressure (mixer, optional high pressure water jet machine), that
must be below 180 bar. Should the mix be operating and manometer show 180bar pressure, check there is nothing in the
hopper preventing mixer rotation.
Remote controls
Insert the plut into the connector's socket located on the machine's bodywork (see par. 5.4.1), if using the remote control via
cable.
If machine is provided with radio control, connect it to the connector's socket (see par. 5.4.2).
The LOCAL/REMOTE button allows selecting the pumping controls from the control board (local) or from a remote device
[remote control (standard) or radio control (optional)].
7.6
Additive pump parameters settings
For proper automati dosage of additive is necessary to set:
- kilos of cement per cubic metre of concrete (refer to the cement manufacturer),
- density of the additive (indicated by the manufacturer, generally on the package itself or on the relative safety data sheet).
Follow the procedure below: