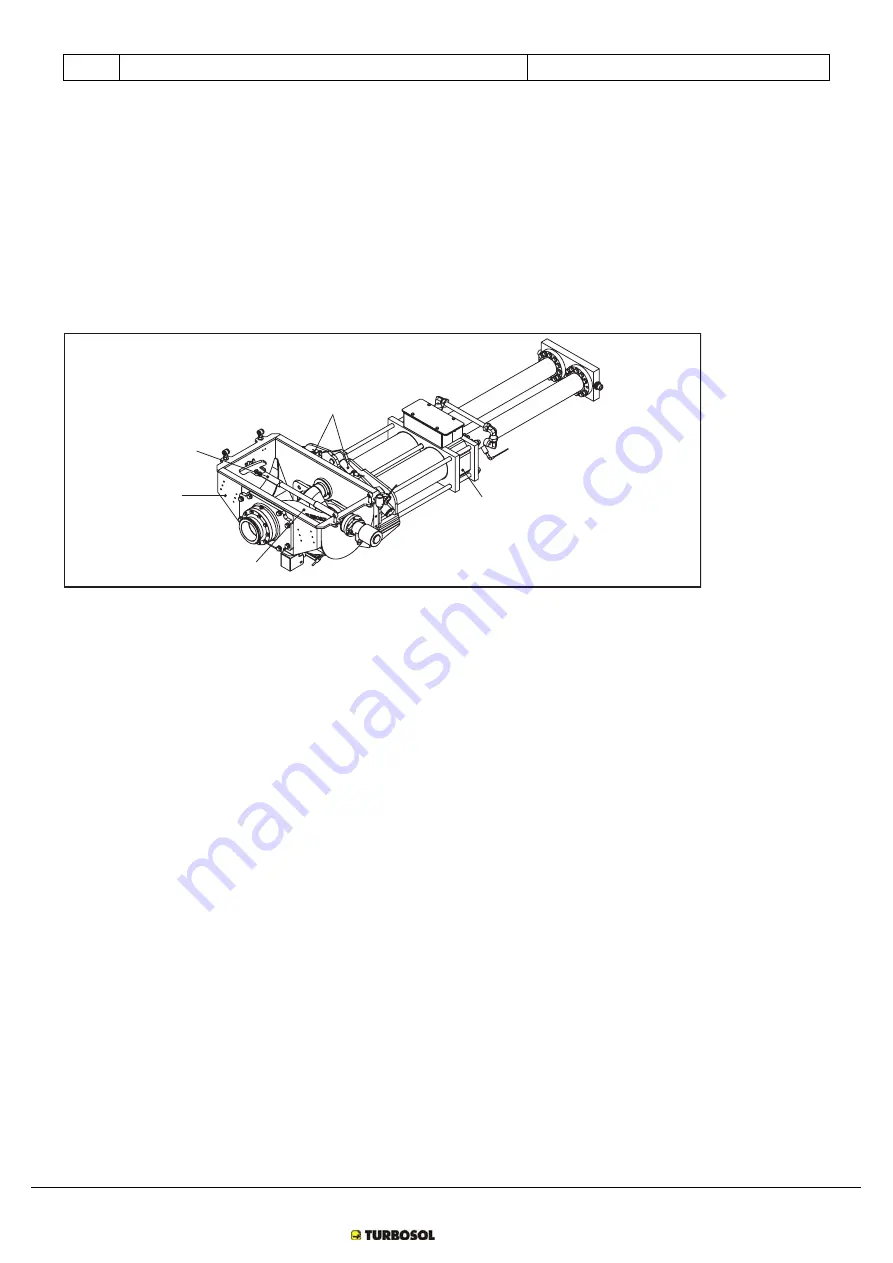
EN
BM 30
IS13/02 - 561291
7 - USE AND OPERATION
Cap. 7 -
Pag. 1/13
THIS MANUAL IS PROPERTY OF
-
ANY TOTAL OR PARTIAL REPRODUCTION IS STRICTLY FORBIDDEN
7.1 OPERATION
PRINCIPLE
The machine's main unit is the pumping unit. It consists of a lower hopper (FIG.21-REF.1) housing the S valve (FIG.21-REF.2)
and the mixer (FIG.21-REF.3). Two hydraulic jacks (FIG.21-REF.4) are found behind the hopper, that move the S valve; two
cylinders accept the concrete sucked by the hopper. A rubber piston that sucks/pumps the concrete is present in each cylinder;
the pistons are moved by hydraulic cylinders. A bowl (FIG.21-REF.8) containing water to cool and lubricate the pistons during
their run, is found between the concrete cylinders and the hydraulic cylinders.
Fresh concrete is poured inside the hopper; the internal grid preventing oversized aggregate from entering, is fitted with a
vibrator to facilitate unload. The concrete is firstly sucked inside the cylinders and then pumped towards the piping. The
alternating of sucking/pumping is produced by the S valve alternating communication between the cylinders and the piping.
The pumping system is hydraulically activated, with hydraulic pump at variable flow rate and valves unit distributing the oil. The
exchange sequence of the pumping unit is controlled by means of four sensors on the machine's board.
The control board manages the main machine functions. Pumping start, stop and reversal can be directly controlled by the
operator by means of remote control via cable (standard) or radio control (optional).
3
2
1
4
8
FIG.21
7.2 PUMPABLE
MATERIALS
The machine works with different types of material:
- Concrete in general, normal or controlled shrinkage grout, mortar for micropiles, common mortar, sludge and bentonite.
- Grout spraying (spritzbeton/shotcrete) for tunnels, slopes, embankments, swimming pools, channels consolidation and
coverings.
All pumpable concrete can be strengthened with flexible or stiff fibres and sprayed with setting accelerator.
The composition of concrete and spritzbeton (shotcrete) to be pumped come from supply agreements not machine dependant.
To avoid problems during pumping:
- the inert's maximum diamter must be between 1/3 and 1/4 of the pipe's diameter,
- the grading envelope of the mix must be suitable for pumping,
- the sand's fineness modulus must be between 2.4 and 3,
- a high slump value must be chosen to facilitate pumping, if the mix cannot be segregated.