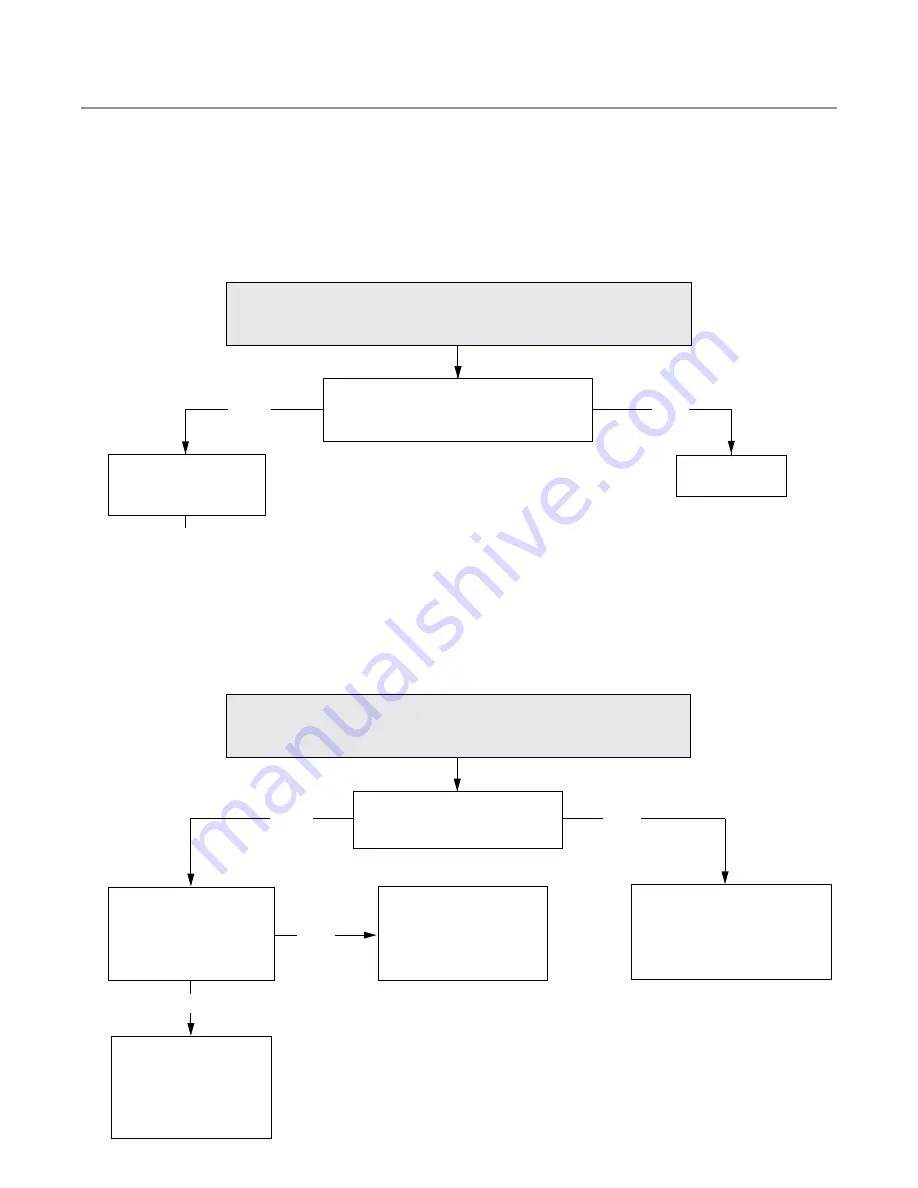
32
DIAGNOSING AN ISSUE
Troubleshooting:
No Keypad Input
YES
NO
Replace the keypad.
(page 38)
Is the keypad cable properly connected
to the control board?
Correct wiring.
Troubleshooting:
“Cook Door Open” Message when Door is Closed
YES
NO
Is the door aligned properly?
Align the door by following
the steps for removing and
reinstalling it (page 45).
YES
Adjust the door switch
(page 45) or replace it.
Non-Fault Code Troubleshooting
This section provides troubleshooting tips for issues that may occur independent of an oven fault.
Correct wiring.
If wiring is damaged,
replace the door
switch (page 46).
Is wiring from the door
switch to the control
board OK?
NO
Summary of Contents for HIGH H BATCH 2
Page 2: ......
Page 3: ...For further information call Customer Service at 800 90turbo Sales Marketing at 866 90turbo TM...
Page 11: ...Specifications and Installation...
Page 12: ......
Page 21: ...Oven Maintenance...
Page 22: ......
Page 26: ...12 OVEN MAINTENANCE This page intentionally left blank...
Page 27: ...Operating the Oven...
Page 28: ......
Page 38: ...22 operating the oven This page intentionally left blank...
Page 39: ...Diagnosing an Issue...
Page 40: ......
Page 54: ...36 diagnosing an issue This page intentionally left blank...
Page 55: ...The Control System...
Page 56: ......
Page 61: ...The Convection System...
Page 62: ......
Page 67: ...The Oven Door...
Page 68: ......
Page 71: ...The Filtering System and Miscellaneous Components...
Page 72: ......
Page 75: ...Schematics...
Page 76: ......
Page 78: ...50 SCHEMATICS This page intentionally left blank...
Page 81: ......