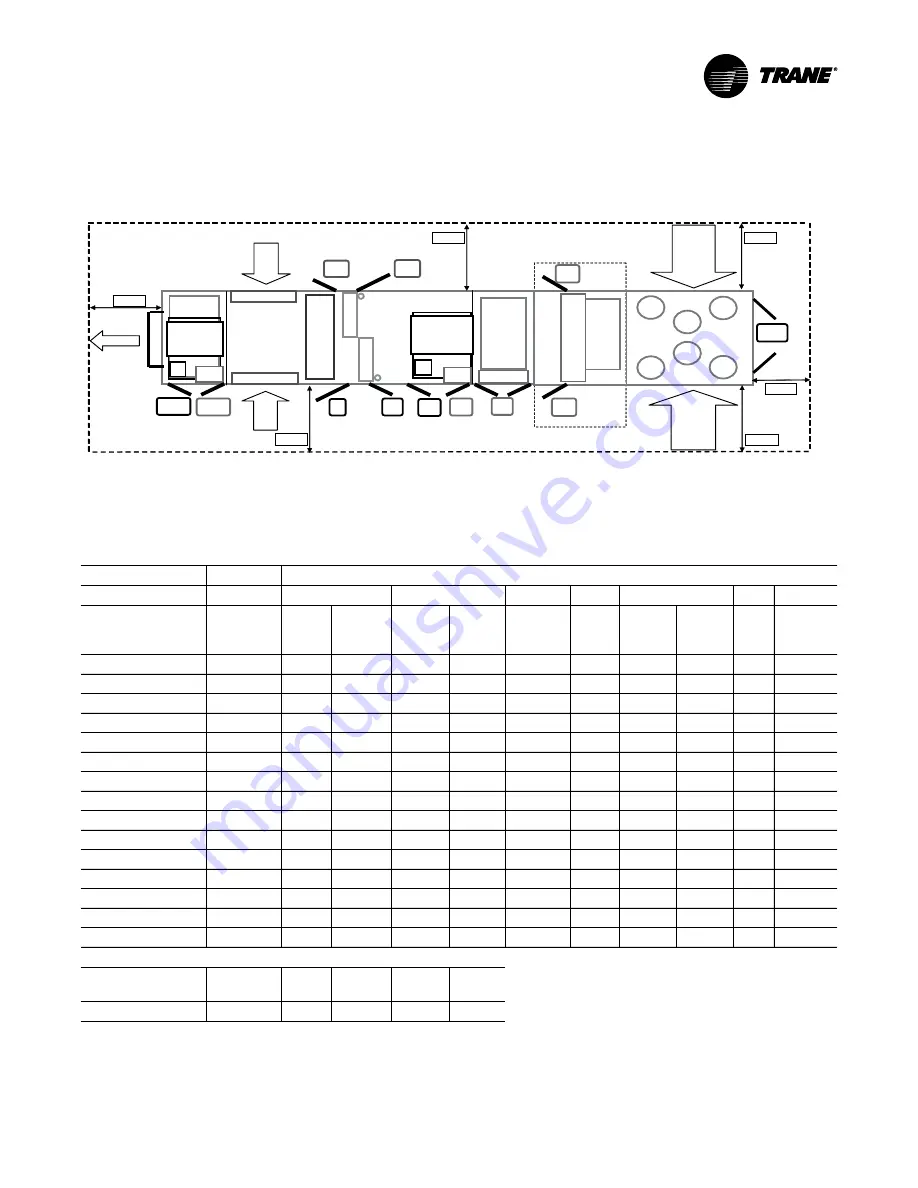
RT-SVX24J-EN
21
Unit Clearances
Figure 10.
Minimum required clearance
(a)
(a) Unit drawing is representative only and may not accurately depict all models.
Filters
VFD
VFD
Heat
Rtn/Exh
Mtr
Rtn/Exh
VFD
Evp
(F)
Fltr
(F)
Sup
Mtr
Sup
VFD
Fltr
(R)
Evp
(R)
Heat
(L&R
Option
Option
As Req.
As Req.
As Req.
Std
Std
Std
Std
Blank Section
Final
Filter
Fnl
Fltr
As Req.
Fnl
Fltr
As Req.
Ctrl Box
(L&R)
Std
Outside
Air
Outside
Air
Exhaust
Condenser
Condenser
Exh
AH R
CBox
AH L
Cond L
Cond R
Left Side
Table 4.
Minimum required clearance
Unit Option Selection (Door Swing
Ft. and In.
)
Standard
VFD
Two-side Access
Door Location
Availability 90-118 120-162
Return/
Exhaust Supply
Heat
Reheat 90-118 120-162
Final
Filter
Energy
Recovery
Exhaust/Ret Motor
Std
2' 2"
2' 2"
*
*
*
*
*
*
*
Exhaust/Ret VFD
As Req.
*
*
2' 2"
*
*
*
*
*
*
ERW Fltr
(a)
(L & R) (F)
Option
*
*
*
*
*
*
*
*
*
2' 2"
ERW Fltr
(a)
(L & R) (R)
Option
*
*
*
*
*
*
*
*
*
2' 2"
Filter (Front)
Std
2' 8"
2' 8"
*
*
*
*
*
*
*
Filter (Rear)
Option
*
*
*
*
*
*
2' 2"
2' 8"
*
Evap (Front)
Std
2' 2"
2' 2"
*
*
*
*
*
*
*
Evap (Rear)
Std
2' 8"
*
*
*
*
*
*
*
*
or Evap (Rear)
Option
*
*
*
*
*
2' 2
*
2' 2"
*
Supply Motor
Std
2' 8"
2' 8"
*
*
*
*
*
*
*
Supply VFD
As Req.
*
*
*
2' 2"
*
*
*
*
*
Heat (Left & Right)
As Req.
*
*
*
*
2' 2"
*
*
*
*
Final Filter (Front)
As Req.
*
*
*
*
*
*
*
*
2' 2"
Final Filter (Rear)
As Req.
*
*
*
*
*
*
*
*
2' 2"
Control Box (L & R)
Std
3' 2"
3' 2"
*
*
*
*
*
*
*
Minimum Required Clearance (Ft.)
AH_L
AH_R
Exh
Cond_L Cond_R
Control
Box
8'
8'
8'
8'
8'
6'
(a) See Unit Dimensions for Energy Recovery Wheel location.