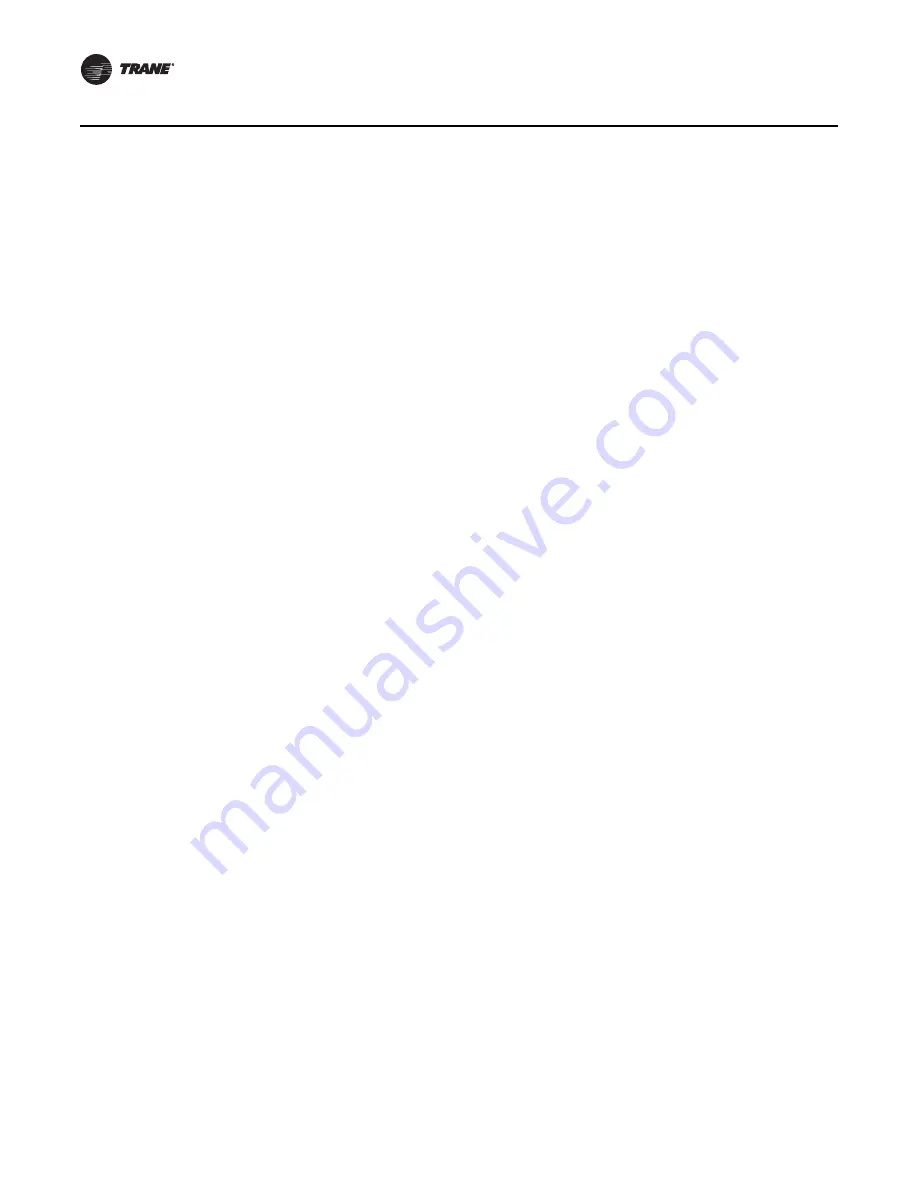
56
SS-SVX09A-EN
Installation
Variable Air Volume Control (Honeywell W7100A)
In a variable air volume system, the desired space temperature is maintained by varying the
amount of conditioned air being delivered to the space. As the cooling requirements of the space
decreases, less air is delivered to the zone; conversely, as the cooling requirements of the space
increases, a greater volume of air is delivered to the zone.
The descriptions of the following basic input devices used with the Honeywell W7100A discharge
air controller are to acquaint the operator with their function as they interface with the controller.
Refer to the field connection diagram in
Figure 27
for the specific component connections at the
unit control panel.
For discussion of evaporator fan interlock, hot gas bypass, and economizer connections, refer to
the “Controls Using 115 VAC” section. Refer to
Figure 26
for the specific component connections.
Discharge Air Sensor (Honeywell 6RT3)
Each unit ordered with variable air volume controls (digit 9 in the model number) is shipped with
a Honeywell 6RT3 discharge air sensor.
WARNING
Hazardous Voltage!
Disconnect all electric power, including remote disconnects before servicing. Follow proper
lockout/tagout procedures to ensure the power can not be inadvertently energized. Failure to
disconnect power before servicing could result in death or serious injury.
The sensor should be installed in a turbulent free area of the discharge air duct at a location that
will provide accurate supply air sensing. Refer to the illustration in
Figure 26
for installation and
sensor dimensional information.
The sensor serves two functions;
1.
It sends the supply air temperature data to the Discharge Air Controller, in the form of an analog
input, to control the economizer (if applicable) and the cycling of the compressors.
2. It serves as a low limit sensor for the system when the supply air temperature reaches too high
a delta tee between the actual supply air temperature and the supply air temperature setpoint.
Before installing any connecting wiring, refer to
Figure 3
to
Figure 8
for the electrical access
locations provided on the unit. Wire the sensor in accordance with the field connection diagram
in
Figure 27
. Shielded cable (Belden 8760 or equivalent) must be used when wiring the sensor to
the terminal board inside the unit’s control panel.
Connect the shielded cable to the appropriate terminals on the terminal board (7TB7), in the unit’s
control panel.
WARNING
Ground Wire!
All field-installed wiring must be completed by qualified personnel. All field-installed wiring
must comply with NEC and applicable local codes. Failure to follow this instruction could result
in death or serious injuries.
WARNING
Grounding Required!
Follow proper local and state electrical code on requirements for grounding. Failure to follow
code could result in death or serious injury.
Ground the shield (at the unit only) using the ground screw in the “customer 24 volt connection
area as shown in the field connection diagram.
Summary of Contents for RAUC-C20
Page 10: ...10 SS SVX09A EN Installation Figure 3 RAUC C20 Unit Dimensional Data Recommended Clearances...
Page 11: ...SS SVX09A EN 11 Installation Figure 4 RAUC C25 Unit Dimensional Data Recommended Clearances...
Page 12: ...12 SS SVX09A EN Installation Figure 5 RAUC C30 Unit Dimensional Data Recommended Clearances...
Page 13: ...SS SVX09A EN 13 Installation Figure 6 RAUC C40 Unit Dimensional Data Recommended Clearances...
Page 14: ...14 SS SVX09A EN Installation Figure 7 RAUC C50 Unit Dimensional Data Recommended Clearances...
Page 15: ...SS SVX09A EN 15 Installation Figure 8 RAUC C60 Unit Dimensional Data Recommended Clearances...
Page 55: ...SS SVX09A EN 55 Installation Field Connection Diagram Notes for all System Control Options...
Page 67: ...SS SVX09A EN 67 Installation Figure 33 6RT1 Discharge Air Sensor Assembly...
Page 96: ...96 SS SVX09A EN System Start Up Figure 47 20 Ton Pressure Curve...
Page 97: ...SS SVX09A EN 97 System Start Up Figure 48 25 Ton Pressure Curve...
Page 98: ...98 SS SVX09A EN System Start Up Figure 49 30Ton Pressure Curve...
Page 99: ...SS SVX09A EN 99 System Start Up Figure 50 40 Ton Pressure Curve per Circuit...
Page 100: ...100 SS SVX09A EN System Start Up Figure 51 50 Ton Pressure Curve per Circuit...
Page 101: ...SS SVX09A EN 101 System Start Up Figure 52 60 Ton Pressure Curve per Circuit...