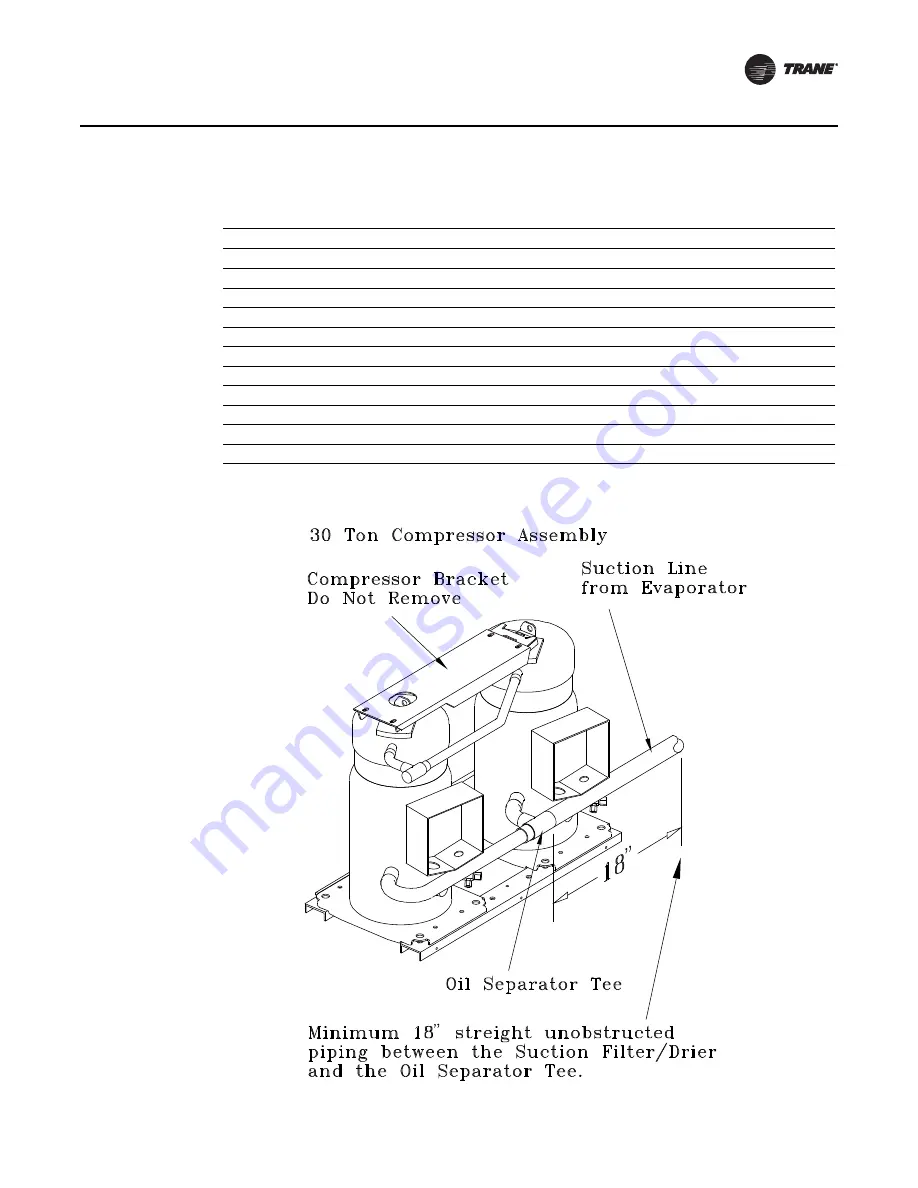
SS-SVX09A-EN
105
Service & Maintenance
Table 19. Compressor Circuit Breaker Data
Voltage
Comp
RLA
LRA
Must
Must
Tons
Hold
Trip
200
9
41.4
269.0
50.4
58.0
230
9
41.4
251.0
50.4
58.0
460
9
18.1
117.0
22.0
25.3
575
9
14.4
94.0
17.5
20.2
380/415
9
17.2
110.0
20.9
24.1
200
14
60.5
404.0
73.7
84.7
230
14
60.5
376.0
73.7
84.7
460
14
26.3
178.0
32.0
36.8
575
14
21.0
143.0
25.6
29.4
380/415
14
26.2
174.0
31.9
36.7
Figure 53. Suction Line Filter/Drier Installation
Summary of Contents for RAUC-C20
Page 10: ...10 SS SVX09A EN Installation Figure 3 RAUC C20 Unit Dimensional Data Recommended Clearances...
Page 11: ...SS SVX09A EN 11 Installation Figure 4 RAUC C25 Unit Dimensional Data Recommended Clearances...
Page 12: ...12 SS SVX09A EN Installation Figure 5 RAUC C30 Unit Dimensional Data Recommended Clearances...
Page 13: ...SS SVX09A EN 13 Installation Figure 6 RAUC C40 Unit Dimensional Data Recommended Clearances...
Page 14: ...14 SS SVX09A EN Installation Figure 7 RAUC C50 Unit Dimensional Data Recommended Clearances...
Page 15: ...SS SVX09A EN 15 Installation Figure 8 RAUC C60 Unit Dimensional Data Recommended Clearances...
Page 55: ...SS SVX09A EN 55 Installation Field Connection Diagram Notes for all System Control Options...
Page 67: ...SS SVX09A EN 67 Installation Figure 33 6RT1 Discharge Air Sensor Assembly...
Page 96: ...96 SS SVX09A EN System Start Up Figure 47 20 Ton Pressure Curve...
Page 97: ...SS SVX09A EN 97 System Start Up Figure 48 25 Ton Pressure Curve...
Page 98: ...98 SS SVX09A EN System Start Up Figure 49 30Ton Pressure Curve...
Page 99: ...SS SVX09A EN 99 System Start Up Figure 50 40 Ton Pressure Curve per Circuit...
Page 100: ...100 SS SVX09A EN System Start Up Figure 51 50 Ton Pressure Curve per Circuit...
Page 101: ...SS SVX09A EN 101 System Start Up Figure 52 60 Ton Pressure Curve per Circuit...