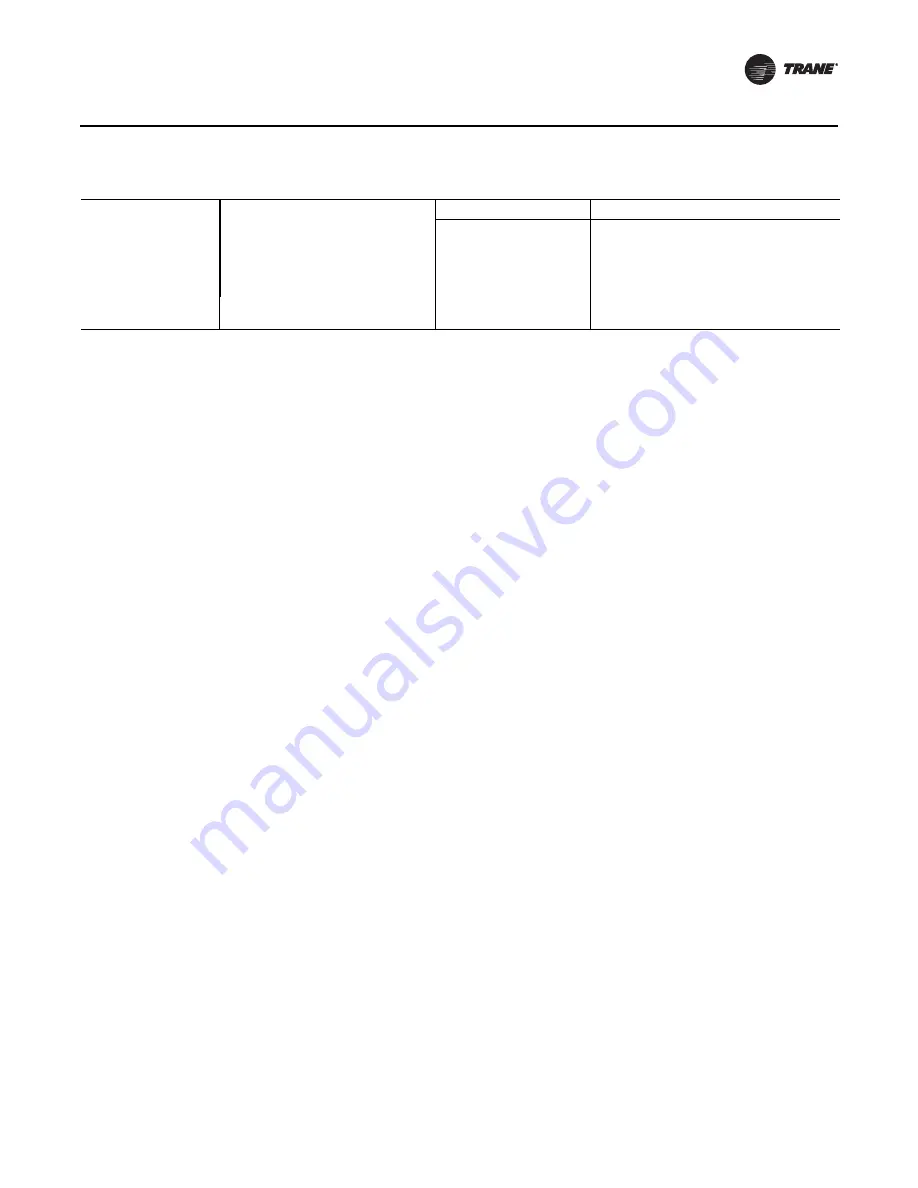
SS-SVX09A-EN
49
Installation
Field Installed Control Wiring
WARNING
Hazardous Voltage!
Disconnect all electric power, including remote disconnects before servicing. Follow proper
lockout/tagout procedures to ensure the power can not be inadvertently energized. Failure to
disconnect power before servicing could result in death or serious injury.
Before installing any connecting wiring, refer to
Figure 3
to
Figure 8
for the electrical access
locations provided on the unit. Install appropriately sized control wiring for the 115 volt electrical
components as required by the application.
Since the unit-mounted 115V control power transformer (1T1) is provided on all units, it is not
necessary to run a separate 115 volt control power source to the unit.
Note:
200/230 Volt units are shipped with transformer 1T1 wired for 200 volt operation. If the unit
is to be operated on a 230 volt power supply, rewire the transformer as shown on the unit
schematic.
Controls Using 115 VAC
WARNING
Hazardous Voltage!
Disconnect all electric power, including remote disconnects before servicing. Follow proper
lockout/tagout procedures to ensure the power can not be inadvertently energized. Failure to
disconnect power before servicing could result in death or serious injury.
Install appropriately sized 115 volt control wiring for the electrical components as required by the
application.
These components may include:
hot gas bypass solenoid wiring;
supply fan interlock and control circuit;
system control switch wiring (“No Control” units);
step controller wiring (“No Control” units);
chilled water pump interlock wiring (EVP units);
chilled water flow switch wiring (EVP units);
outside air thermostat wiring (EVP units):
RAUC-C609
380/415/50/
3XL
342-418/
373-456
122
125
125
0.75 6
1.0
1.7
9.2
4
_
26.2
_
174.0
_
16.4
1.
Electrical data is for each individual motor.
2.
Max Overcurrent Protection device permitted by N.E.C. 440-22 (1993) is 225% of the largest compressor motor RLA plus the remaining motor RLA
and FLA values.
3.
Minimum circuit ampacity is 125% of the largest compressor motor RLA plus the remaining motor RLA and FLA values.
4.
Recommended dual element fuse size is 150% of the largest compressor motor RLA plus the remaining motor RLA and FLA values.
5.
Kw values are taken at conditions of 45ºF saturated suction temperature at the compressor and 95ºF ambient.
6.
Local codes may take precedence.
Table 8.
Electrical Service Sizing Data (continued)
Model
Electrical
Charac.
Unit Characteristics
Condenser Fan Motor
Compressor Motor
Allow-
able
Voltage
Range
Min.
Circuit
Amp
Max.
Over-
current
Protect
-ion
Rec.
Dual
Element
Fuse
Size
No
RLA
(Ea)
10
Ton
RLA
(Ea)
15
Ton
LRA
(Ea)
10
Ton
LRA
(Ea)
15
Ton
Kw
(Ea)
10
Ton
Kw
(Ea)
15
Ton
KW
(Ea) No HP
FLA
(Ea)
LRA
(Ea)
Summary of Contents for RAUC-C20
Page 10: ...10 SS SVX09A EN Installation Figure 3 RAUC C20 Unit Dimensional Data Recommended Clearances...
Page 11: ...SS SVX09A EN 11 Installation Figure 4 RAUC C25 Unit Dimensional Data Recommended Clearances...
Page 12: ...12 SS SVX09A EN Installation Figure 5 RAUC C30 Unit Dimensional Data Recommended Clearances...
Page 13: ...SS SVX09A EN 13 Installation Figure 6 RAUC C40 Unit Dimensional Data Recommended Clearances...
Page 14: ...14 SS SVX09A EN Installation Figure 7 RAUC C50 Unit Dimensional Data Recommended Clearances...
Page 15: ...SS SVX09A EN 15 Installation Figure 8 RAUC C60 Unit Dimensional Data Recommended Clearances...
Page 55: ...SS SVX09A EN 55 Installation Field Connection Diagram Notes for all System Control Options...
Page 67: ...SS SVX09A EN 67 Installation Figure 33 6RT1 Discharge Air Sensor Assembly...
Page 96: ...96 SS SVX09A EN System Start Up Figure 47 20 Ton Pressure Curve...
Page 97: ...SS SVX09A EN 97 System Start Up Figure 48 25 Ton Pressure Curve...
Page 98: ...98 SS SVX09A EN System Start Up Figure 49 30Ton Pressure Curve...
Page 99: ...SS SVX09A EN 99 System Start Up Figure 50 40 Ton Pressure Curve per Circuit...
Page 100: ...100 SS SVX09A EN System Start Up Figure 51 50 Ton Pressure Curve per Circuit...
Page 101: ...SS SVX09A EN 101 System Start Up Figure 52 60 Ton Pressure Curve per Circuit...