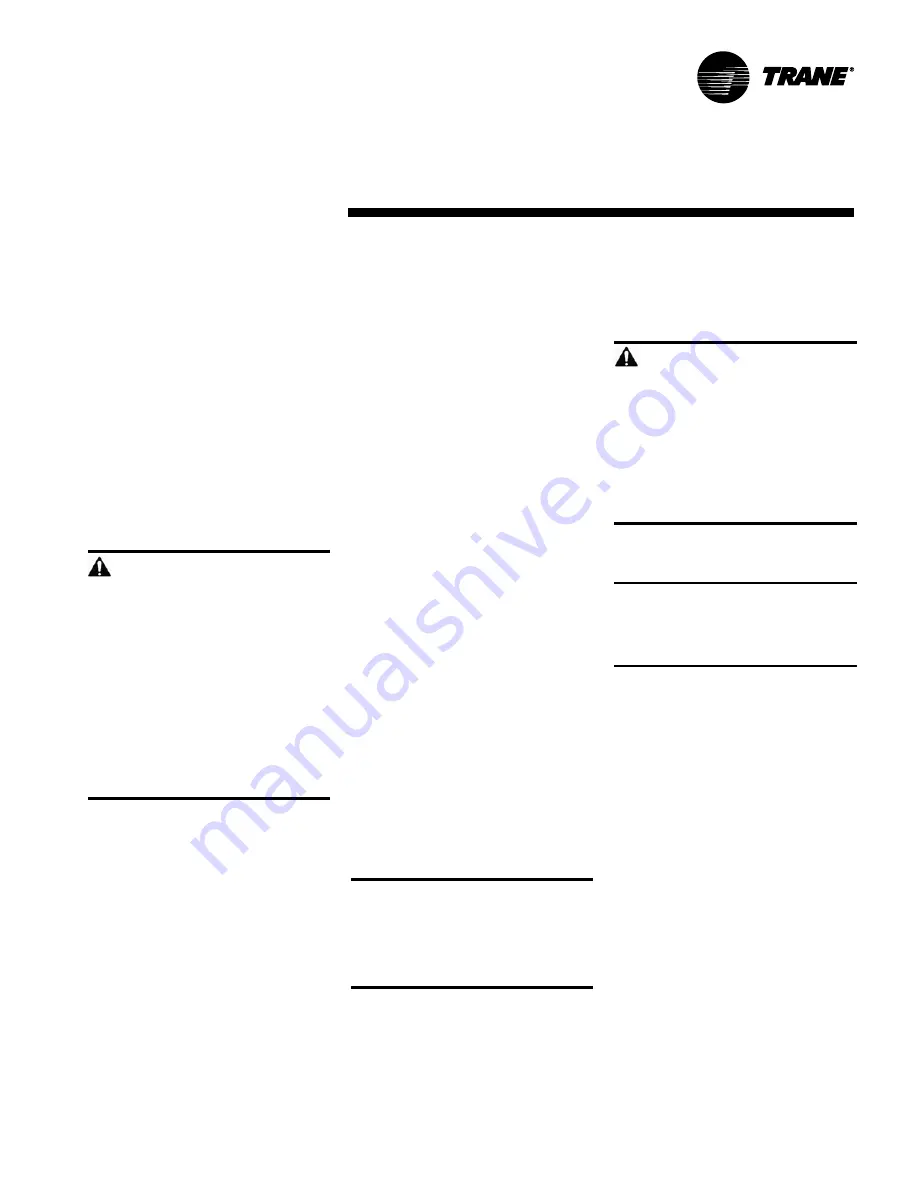
LPC-SVX01C-EN
101
Maintenance
maintenance
procedures
Steam and Hydronic Coil Cleaning
Procedure
1. Disconnect all electrical power to the
unit.
2. Don the appropriate personal
protective equipment (PPE).
3. Gain access to both sides of the coil.
4. Use a soft brush to remove loose
debris from both sides of the coil.
5. Use a steam cleaning machine, starting
from the top of the coil and working
downward. Clean the leaving air side of
the coil first, then the entering air side.
Use a block-off to prevent steam from
blowing through the coil and into a dry
section of the unit.
6. Repeat step 5 as necessary. Confirm
that the drain line is open following
completion of the cleaning process.
7. Allow the unit to dry thoroughly before
putting the system back into service.
8. Straighten any coil fins that may be
damaged with a fin rake.
9. Replace all panels and parts and
restore electrical power to the unit.
10. Ensure that contaminated material
does not contact other areas of the unit
or building. Properly dispose of all
contaminated materials and cleaning
solutions.
Winterizing the Coil
Make provisions to drain coils that are not
in use, especially when subjected to
freezing temperatures.
To drain the coil, first blow out the coil
with compressed air. Next, fill and drain
the tubes with full-strength ethylene
glycol several times. Then drain the coil as
completely as possible.
CAUTION
Coil Freeze-up Damage!
Failure to properly drain and vent
coils when not in use during freezing
temperatures may result in coil
freeze-up damage.
Coil Maintenance
Keep coils clean to maintain maximum
performance. For operation at its highest
efficiency, clean the coil often during
periods of high demand or when dirty
conditions prevail. Clean the coil a
minimum of once a year to prevent dirt
buildup in the coil fins, where it may not
be visible.
Remove large debris from the coils and
straighten fins before cleaning. Remove
filters before cleaning.
Clean the coil fins using steam with
detergent, hot water spray and deter-
gent, or a commercially available
chemical coil cleaner. Be sure to rinse
coils thoroughly after cleaning.
WARNING
Hazardous Chemicals!
Coil cleaning agents can be either
acidic or highly alkaline. Handle
chemical carefully. Proper handling
should include goggles or face shield,
chemical resistant gloves, boots,
apron or suit as required. For personal
safety refer to the cleaning agent
manufacturer’s Materials Safety Data
Sheet and follow all recommended
safe handling practices. Failure to
follow all safety instructions could
result in death or serious injury.
Inspecting and Cleaning Coils
Coils become externally fouled as a result
of normal operation. Dirt on the coil
surface reduces it’s ability to transfer heat
that can result in comfort problems,
increased airflow resistance and thus
increased operating energy costs. If the
coil surface dirt becomes wet, which
commonly occurs with cooling coils,
microbial growth (mold) may result,
causing unpleasant odors and serious
health-related indoor air quality
problems.
Inspect coils at least every six months or
more frequently as dictated by operating
experience. Cleaning frequently is
dependent upon system operating hours,
filter maintenance, and efficiency and dirt
load. Follow the suggested methods in
the following paragraphs.
Refrigerant Coil Cleaning Procedure
1. Disconnect all electrical power to the
unit.
2. Wearing the appropriate personal
protective equipment, use a soft brush
to remove loose debris from both sides
of the coil.
3. Install a block-off to prevent spray from
going through the coil and into a dry
section of the unit and/or system
ductwork.
WARNING
Hazardous Pressures!
Coils contain refrigerant under
pressure. When cleaning coils,
maintain coil cleaning solution
temperature under 150°F to avoid
excessive pressure in the coil. Failure
to follow these safety precautions
could result in coil bursting, which
could result in death or serious injury.
4. Mix a high-quality coil cleaning
detergent with water according to the
manufacturer’s instructions.
Note: If the detergent is strongly alkaline
after mixing (pH of 8.5 or higher), it must
contain an inhibitor. Follow the cleaning
solution manufactuer’s instructions
regarding the use of the product.
5. Place the mixed solution in a garden
pump-up sprayer or high-pressure
sprayer. If using a high-pressure
sprayer, follow these guidelines:
• maintain minimum nozzle spray angle of
15 degrees
• spray perpendicular to the coil face
• keep the nozzle at least six inches from
the coil
• do not exceed 600 psi
6. Spray the leaving air side of the coil
first, then the entering air side.
7. Thoroughly rinse both sides of the coil
and drain pan with cool, clean water.
8. Repeat steps 6 and 7 as necessary.
9. Straighten any coil fins damaged
during the cleaning process.
10. Confirm the drain line is open
following the cleaning process.
11. Allow the unit to dry thoroughly before
putting it back into service.
12. Replace al panels and parts and
restore electrical power to the unit.
13. Do not allow contaminated material
to contact other areas of the unit or
building. Properly dispose of all
contaminated materials and cleaning
solution.
Summary of Contents for LPC
Page 50: ...50 LPC SVX01C EN Operation general information Figure O GI 9 Tracer AH540 termination board ...
Page 91: ...LPC SVX01C EN 91 Maintenance diagnostics Table M D 2 Tracer AH540 541 diagnostics ...
Page 92: ...92 LPC SVX01C EN Maintenance diagnostics Table M D 2 continued Tracer AH540 541 diagnostics ...
Page 94: ...94 LPC SVX01C EN Maintenance troubleshooting Table M T 2 Valves stay open ...
Page 95: ...LPC SVX01C EN 95 Maintenance troubleshooting Table M T 3 Valves stay closed ...
Page 96: ...96 LPC SVX01C EN Maintenance troubleshooting Table M T 4 Outdoor air damper stays open ...
Page 97: ...LPC SVX01C EN 97 Maintenance troubleshooting Table M T 5 Outdoor air damper stays closed ...
Page 107: ...LPC SVX01C EN 107 Maintenance appendix Table M A 6 Hard wired CO2 sensor values ...
Page 109: ......