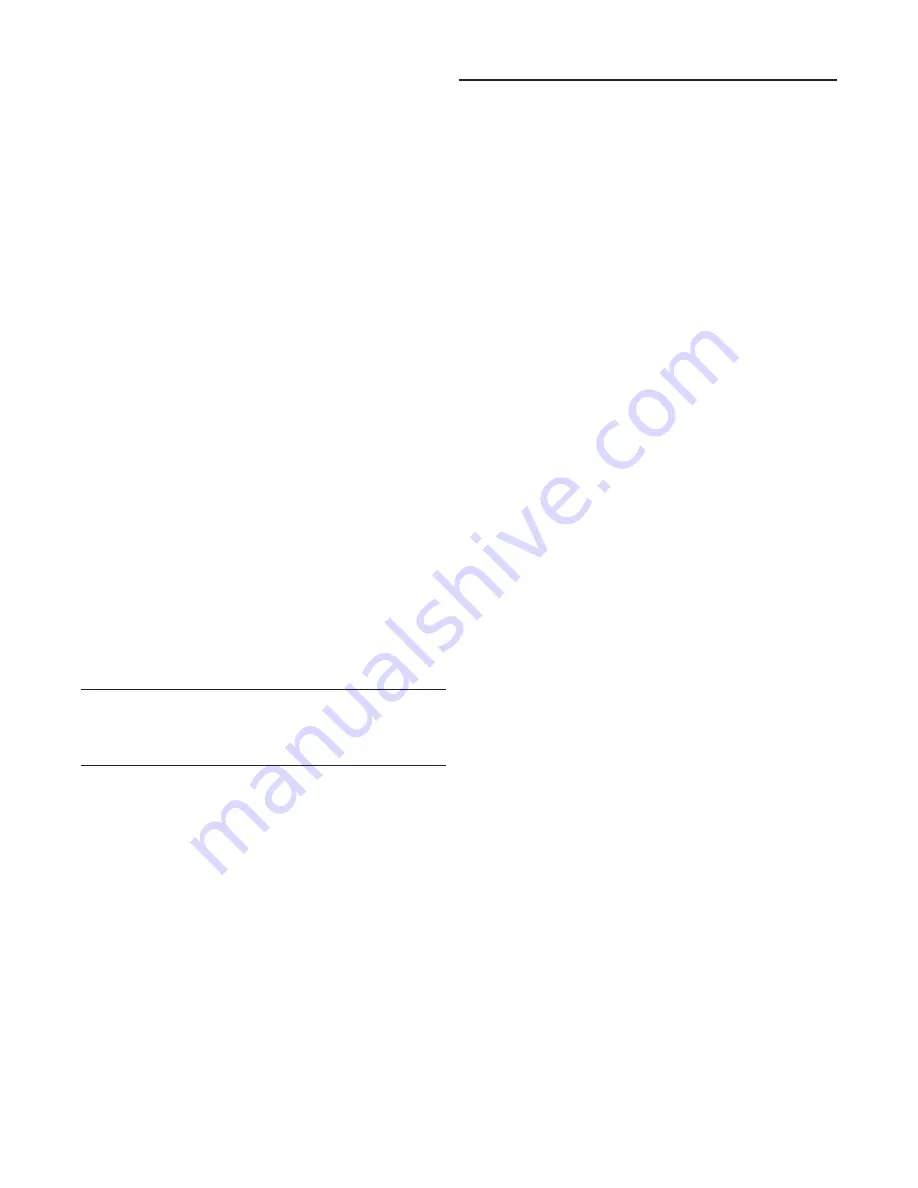
24
Installation
General Unit Requirements
The checklist listed below is a summary of the steps re-
quired to successfully install a commercial air cooled unit.
This checklist is intended to acquaint the installing person-
nel with what is required in the installation process. It does
not replace the detailed instruction called out in the appli-
cable sections of this manual.
[ ] Verify that the power supply complies with the unit name-
plate specifications.
[ ] Check the unit for shipping damage and material short-
age; file a freight claim and notify Trane office.
[ ] Verify that the installation location of the unit will provide
the required clearance for proper operation.
[ ] Install appropriate isolators, if required.
Chilled Water Piping Requirements
[ ] Install properly sized chilled water pipe between the
chiller and the supporting equipment. Refer to the
“Chilled Water Piping” section for recommended system
components and guidelines. Ensure that all necessary
components have been installed:
Recommended:
Water pressure gauges (with isolation valves)
Thermometers
Chiller isolation (shutoff) valves in the solution inlet and
outlet piping
Pressure taps on the inlet and outlet at the chiller barrel
Chiller drain plug, or drain piping with a shutoff valve
Balancing valve
Required:
Strainer in the solution inlet piping
Flow switch in the solution outlet piping
[ ] Flushing the chilled solution piping system, if applicable.
Note: If using an acidic, commercial flushing
solution, to prevent damage to the internal
evaporator components, flush all chilled solution
piping before making the final connection to the
chiller.
[ ] Connecting the chilled solution piping to the chiller barrel.
[ ] Install heat tape and insulation, if necessary, to protect
any exposed solution piping from external freezing condi-
tions.
Main Electrical Power Requirements
[ ] Verify the power supply meets the required power re-
quirements of the system.
WARNING
Hazardous Voltage!
Disconnect all electric power, including remote discon-
nects before servicing. Follow proper lockout/tagout
procedures to ensure the power can not be inadvert-
ently energized. Failure to disconnect power before ser-
vicing could result in death or serious injury.
[ ] Install power wiring in accordance with all applicable
codes.
[ ] Install and connect properly sized power supply wiring,
with over current protection, to the main power terminal
block (1TB1) or to an optional factory mounted nonfused
disconnect switch (1S1) in the control panel.
[ ] Install and connect properly sized power supply wiring,
with over current protection, to the proper termination
point in the air handling unit (If applicable).
[ ] Install and connect properly sized power supply wiring,
with over current protection, to the proper termination
point for the chilled solution pump (chiller units only).
[ ] Install proper grounding wires to an earth ground.
Field Installed Control Wiring Requirements
115 Volt Control Wiring
[ ] Install the interlock circuitry wiring for the chilled water
pump auxiliary contacts to the UCM to permit compres-
sor operation after the chilled water pump has started.
(i.e., proof of flow device, pump starter station, pump
starter auxiliary contacts, etc). Refer to the Field Connec-
tion Diagram that shipped with the unit for interlocking in-
formation.
Low Voltage Wiring (AC & DC)
[ ] Verify that the proper connections have been made at
the UCM for the remote running/alarm indication con-
tacts (if applicable).
[ ] Verify that the proper connections have been made for
external auto/stop (if applicable).
[ ] Verify that the proper connections have been made for
the optional chilled water flow switch (if applicable).
[ ] Verify that the proper connections have been made at
the UCM for the optional compressor inhibit/KW limit
function (if applicable).
[ ] Verify that the proper connections have been made at
the UCM for the optional external Auto/Stop (if used).
[ ] Verify that the proper connections have been made for
the zone sensor(s) at the UCM for chilled solution set-
point reset based on zone temperature.
[ ] If the unit is a component of an ice storage system,
verify that the remote contact connections have been
made at the UCM for ice machine control.
[ ] Verify that the proper connections have been made be-
tween the UCM and the bidirectional communication link
device (Tracer
TM
or other remote device, if applicable).
[ ] Verify that the shielded twisted-pair communication wire
between the UCM and the remote display panel has
been connected (if applicable).
Chilled Water Piping
Evaporator water inlet and outlet types, sizes and locations
are shown in Figure 2. Refer to the operating GPM param-
eters listed in Table 9 when determining flow and piping re-
quirements. Figure 8 illustrates the typical water piping
components for chiller applications. Refer to this illustration
while following the discussion on the various piping compo-
nents.
Summary of Contents for IntelliPak CG-SVX02B-EN
Page 10: ...10 General Information Module Mounting Locations Screw Hole...
Page 12: ...12 Figure 1 Typical Installation Clearances for Single Multiple or Pit Applications...
Page 13: ...13 Figure 2 C20 Ton Unit Dimensional Data Recommended Clearances...
Page 14: ...14 Figure 2 C25 Ton Unit Dimensional Data Recommended Clearances...
Page 15: ...15 Figure 2 C30 Ton Unit Dimensional Data Recommended Clearances...
Page 16: ...16 Figure 2 C40 Ton Unit Dimensional Data Recommended Clearances...
Page 17: ...17 Figure 2 C50 Ton Unit Dimensional Data Recommended Clearances...
Page 18: ...18 Figure 2 C60 Ton Unit Dimensional Data Recommended Clearances...
Page 35: ...35...
Page 36: ...36 Figure 12B Typical GBAS 0 5 Volt Connections Diagram...
Page 37: ...37...
Page 38: ...38...
Page 63: ...63...
Page 64: ......