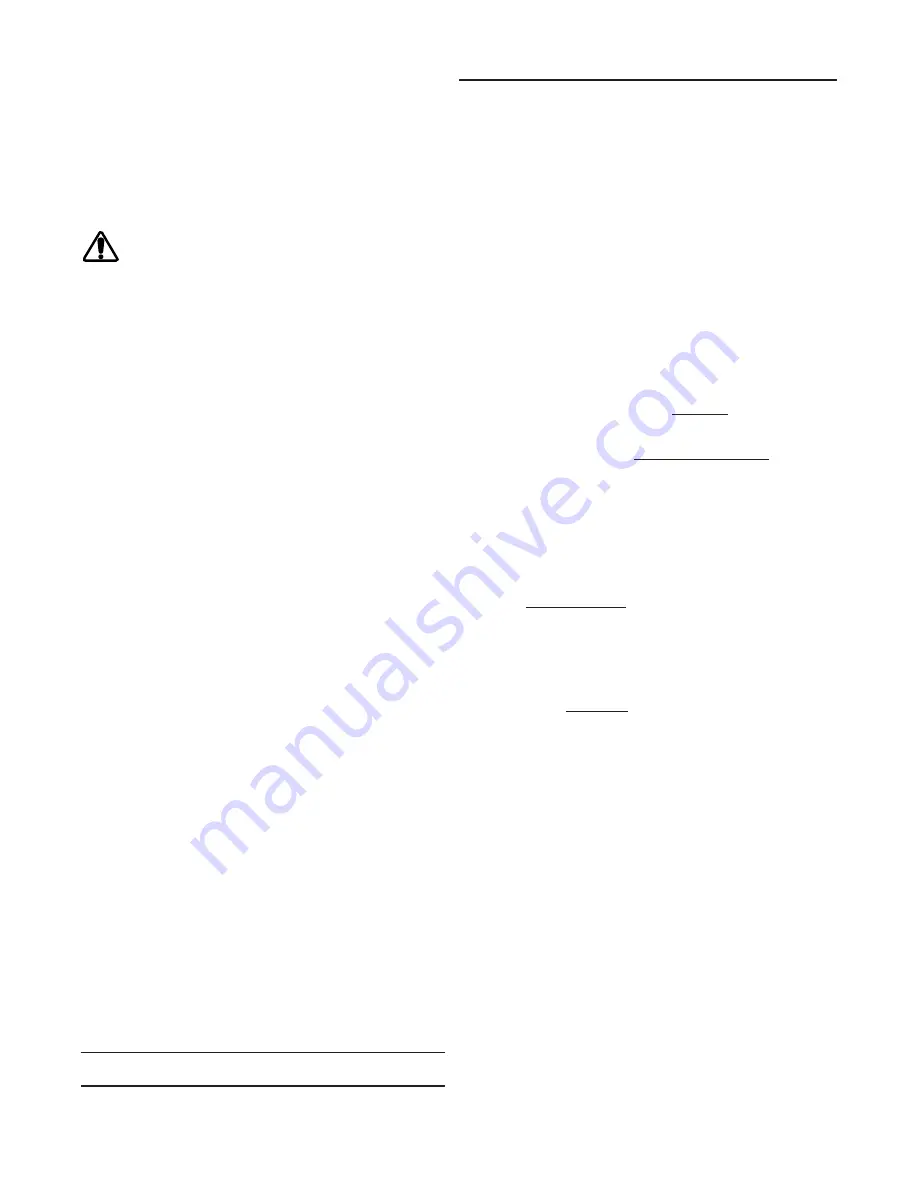
39
System Pre-Start Procedures
Use the checklist provided below in conjunction with the
“General Unit Requirement” checklist” to ensure that the
unit is properly installed and ready for operation. Be sure to
complete all of the procedures described in this section be-
fore starting the unit for the first time.
[ ] Turn the field supplied disconnect switch, located up-
stream of the unit, to the “Off” position.
WARNING
Hazardous Voltage!
Disconnect all electric power, including remote discon-
nects before servicing. Follow proper lockout/tagout
procedures to ensure the power can not be inadvert-
ently energized. Failure to disconnect power before ser-
vicing could result in death or serious injury.
[ ] Turn the “System” selection switch (at the Remote Panel)
to the “Off” position and the “Fan” selection switch (if ap-
plicable) to the “Auto” or “Off” position.
[ ] Check all electrical connections for tightness and “point
of termination” accuracy.
[ ] Verify that the condenser airflow will be unobstructed.
[ ] Check the condenser fan blades. Ensure they rotate
freely within the fan orifices and are securely fastened to
the fan motor shaft.
[ ] Verify that all compressor service valves, discharge ser-
vice valves, and liquid line service valves are back
seated on each circuit.
CAUTION
Compressor Damage!
Do not allow liquid refrigerant to enter the suction line.
Excessive liquid accumulation in the liquid lines may
result in compressor damage.
Compressor service valves must be fully opened before
start-up (suction, discharge, liquid line, and oil line).
Failure to fully open valves prior to start-up may cause
compressor failure due to lack of refrigerant and/or oil
flow.
[ ] Inspect the interior of the unit for tools and debris.
[ ] Fill the chilled water system.
[ ] Vent the chilled water system at the highest points in the
system. Vent the air out of the chiller barrel by opening
the vent, located on the top of the chiller barrel. Close
the vent when the chiller barrel is full of water.
[ ] Once the system has been filled, inspect the entire
chilled water piping system for leaks. Make any neces-
sary repairs before proceeding.
Note: To avoid possible equipment damage, do not
use untreated or improperly treated system water.
WARNING
Live Electrical Components!
During installation, testing, servicing and troubleshoot-
ing of this product, it may be necessary to work with
live electrical components. Have a qualified licensed
electrician or other individual who has been properly
trained in handling live electrical components perform
these tasks. Failure to follow all electrical safety pre-
cautions when exposed to live electrical components
could result in death or serious injury.
Voltage Imbalance
Excessive three phase voltage imbalance between phases
will cause motors to overheat and eventually fail. The maxi-
mum allowable voltage imbalance is 2%. Measure and
record the voltage between phases 1, 2, and 3 and calcu-
late the amount of imbalance as follows:
% Voltage Imbalance =
100 X
AV - VD
where;
AV
AV (Average Voltage) =
Volt 1 + Volt 2 + Volt 3
3
V1, V2, V3 = Line Voltage Readings
VD = Line Voltage reading that deviates the farthest from
the average voltage.
Example:
If the voltage readings of the supply power
measured 221, 230, and 227, the average volts would
be:
221 + 230 + 227 = 226 Avg.
3
VD (reading farthest from average) = 221
The percentage of Imbalance equals:
100 X 226 - 221 = 2.2%
226
The 2.2% imbalance in this example exceeds the maximum
allowable imbalance of 2.0%. This much imbalance be-
tween phases can equal as much as a 20% current imbal-
ance with a resulting increase in motor winding tempera-
tures that will decrease motor life. If the voltage imbalance
is over 2%, notify the proper agencies to correct the voltage
problem before operating this equipment.
Scroll Compressor Current Imbalance
Typically, current imbalance is associated with loss in motor
efficiency, higher operating motor temperature, loss of per-
formance and reliability.
With the designs of specialized motors such as those used
in the Trane scroll compressor, operating temperature, effi-
ciency, performance, and reliability has been taken into ac-
count in the total performance of the compressor.
Current imbalance in a scroll compressor can typically vary
from 4 to 15 percent with balanced line voltage. This imbal-
ance occurs because not all of the winding turns see the
same amount of stator iron. The variance of iron within the
motor is to accommodate design requirements for motor
cooling and oil return.
Summary of Contents for IntelliPak CG-SVX02B-EN
Page 10: ...10 General Information Module Mounting Locations Screw Hole...
Page 12: ...12 Figure 1 Typical Installation Clearances for Single Multiple or Pit Applications...
Page 13: ...13 Figure 2 C20 Ton Unit Dimensional Data Recommended Clearances...
Page 14: ...14 Figure 2 C25 Ton Unit Dimensional Data Recommended Clearances...
Page 15: ...15 Figure 2 C30 Ton Unit Dimensional Data Recommended Clearances...
Page 16: ...16 Figure 2 C40 Ton Unit Dimensional Data Recommended Clearances...
Page 17: ...17 Figure 2 C50 Ton Unit Dimensional Data Recommended Clearances...
Page 18: ...18 Figure 2 C60 Ton Unit Dimensional Data Recommended Clearances...
Page 35: ...35...
Page 36: ...36 Figure 12B Typical GBAS 0 5 Volt Connections Diagram...
Page 37: ...37...
Page 38: ...38...
Page 63: ...63...
Page 64: ......