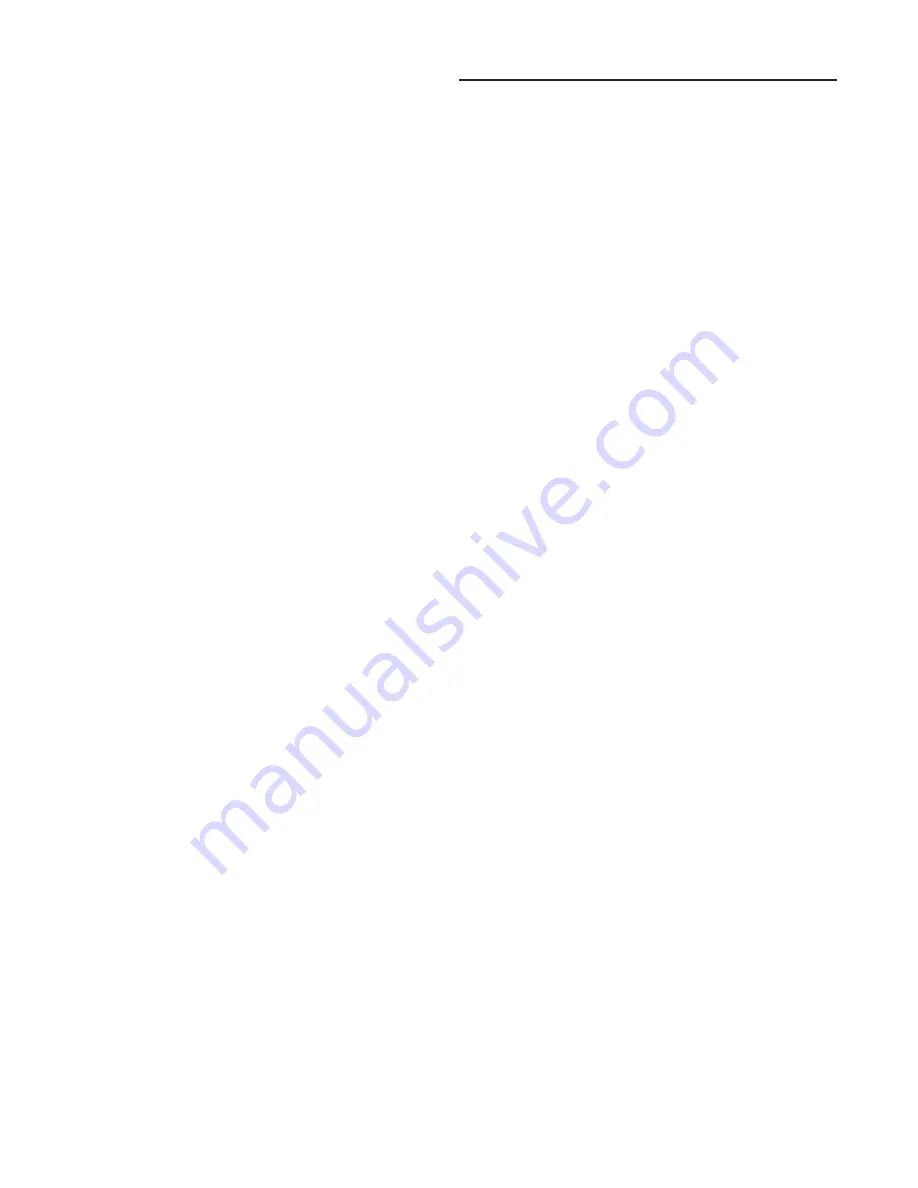
5
General Information
Unit Description
Before shipment, each unit is leak tested, dehydrated,
charged with refrigerant and compressor oil, and run tested
for proper control operation.
Each unit is equipped with manifolded scroll compressors.
Each manifolded set of compressors is piped in parallel and
utilizes a passive oil management system to maintain
proper compressor oil level.
The condenser coils are aluminum fin, mechanically bonded
to copper tubing. Copper-fin coils are optional. Louvered
condenser grilles for coil protection are standard.
Direct-drive, vertical discharge condenser fans are provided
with built-in thermal overload protection.
For “Ship with” items, refer to the Unit Component “Layout”
and “Ship with” Locations illustration.
If low ambient operation is required, low ambient dampers
are available as a field or factory installed option.
The evaporators used in each air-cooled cold generator are
of brazed plate construction. Each evaporator is fully insu-
lated. Entering and leaving temperatures of the chilled solu-
tion are measured by sensors located on the evaporator.
A liquid line solenoid valve, filter drier, sight glass, thermo-
static expansion valve, and service valves (liquid and dis-
charge) are provided on each circuit.
Standard controls for these units is a microelectronics con-
trol system that consists of a network of modules referred to
collectively as Unit Control Modules (UCM). The acronym
UCM is used extensively throughout this document when
referring to the control system network.
These modules, through Proportional/Integral control algo-
rithms, perform specific unit functions that governs unit op-
eration in response to chilled water temperature leaving the
evaporator. The stages of capacity control for these units is
achieved by starting and stopping the compressors.
The modules are mounted in the control panel and are fac-
tory wired to their respective internal components. They re-
ceive and interpret information from other unit modules,
sensors, remote panels, and customer binary contacts to
satisfy the applicable request for cooling. Refer to the fol-
lowing discussion for an explanation of each module func-
tion.
Human Interface Module (HI - Standard)
(1U65 = Local, 6U66 = Remote)
The Human Interface module enables the operator to adjust
the operating parameters for the unit using it’s 16 key key-
pad. The 2 line, 40 character LCD screen provides status
information for the various unit functions as well as menus
for the operator to set or modify the operating parameters.
Cold Generator Module (1U48) (CGM - Standard)
The Cold Generator Module (CGM) responds to cooling re-
quests by energizing the proper unit components based on
information received from other unit modules, sensors, re-
mote panels, and customer supplied binary inputs. It ini-
tiates unit operation based on that information.
Compressor Module (1U44) (MCM)
The Compressor module, upon receiving a request for me-
chanical cooling, energizes the appropriate compressors
and condenser fans. It monitors the compressor operation
through feedback information it receives from various pro-
tection devices. It also provides heat tape output control for
heat exchanger protection.
Interprocessor Communications Board (1U55) (IPCB -
Optional - used with Optional Remote Human Interface)
The Interprocessor Communication Board expands communi-
cations from the unit’s UCM network to a Remote Human Inter-
face Panel. DIP switch settings on the IPCB module for this ap-
plication should be; Switches 1 and 2 “Off”, Switch 3 “On”.
Trane Communications Interface Module (1U54) (TCI -
Optional - used with Trane ICS
TM
Systems)
The Trane Communication Interface module expands
communications from the unit’s UCM network to a Trane Tracer
100™ or a Tracer Summit™ system and allows external setpoint
adjustment and monitoring of status and diagnostics.
DIP Switch settings on the TCI module for these applica-
tions should be: Switches 1, 2, and 3 are “Off”
Generic Building Automation System Module
(1U51 = GBAS 0-5V, 1U98 = GBAS 0-10V)
Optional - used with Non-Trane Building Control System)
The Generic Building Automation System (GBAS) module
allows a non-Trane building control system to communicate
with the unit and accepts external setpoints in form of ana-
log inputs (0 - 5 DCV or 0 - 10 DCV depending on the mod-
ule selected) and a binary Input for demand limit. Five (5)
binary outputs are available on 0 - 5 DCV modules. One (1)
binary output and four (4) analog outputs are available on
the 0 - 10 DCV modules. Refer to the “Field Installed Con-
trol Wiring” section for the control wiring to the GBAS mod-
ule and the various desired setpoints with the correspond-
ing DC voltage inputs.
Lontalk Communication Interface Module (1U54)
(LCI Optional - used on units with Trane ICS
™
or 3rd
party Building Automation Systems)
The LonTalk Communication Interface module expands com-
munications from the unit’s UCM network to a Trane Tracer
Summit
™
or a 3rd party building automation system, that uti-
lizes LonTalk, and allows external setpoint and configuration
adjustment and monitoring of status and diagnostics.
Current Sensing Module (1U90) (CSM - Optional)
Current transformers located around two (2) of the main
power leads for each compressor monitors the running cur-
rent during compressor operation. The information is sent to
the CGM and can be accessed through the “Compressor
Status” submenu displayed at the Human Interface Module.
Superheat & Subcooling Module (1U91) (SSM -
Optional)
Monitors the system operating superheat and subcooling
through the use of pressure transducers, liquid line, and
suction line temperature sensors. The information is sent to
the SSM and can be accessed through the “Compressor
Status” submenu displayed at the Human Interface Module.
Input Devices & System Functions
The descriptions of the following basic Input Devices used
within the UCM network are to acquaint the operator with
their function as they interface with the various modules.
Refer to the unit’s electrical schematic for the specific mod-
ule connections.
Summary of Contents for IntelliPak CG-SVX02B-EN
Page 10: ...10 General Information Module Mounting Locations Screw Hole...
Page 12: ...12 Figure 1 Typical Installation Clearances for Single Multiple or Pit Applications...
Page 13: ...13 Figure 2 C20 Ton Unit Dimensional Data Recommended Clearances...
Page 14: ...14 Figure 2 C25 Ton Unit Dimensional Data Recommended Clearances...
Page 15: ...15 Figure 2 C30 Ton Unit Dimensional Data Recommended Clearances...
Page 16: ...16 Figure 2 C40 Ton Unit Dimensional Data Recommended Clearances...
Page 17: ...17 Figure 2 C50 Ton Unit Dimensional Data Recommended Clearances...
Page 18: ...18 Figure 2 C60 Ton Unit Dimensional Data Recommended Clearances...
Page 35: ...35...
Page 36: ...36 Figure 12B Typical GBAS 0 5 Volt Connections Diagram...
Page 37: ...37...
Page 38: ...38...
Page 63: ...63...
Page 64: ......