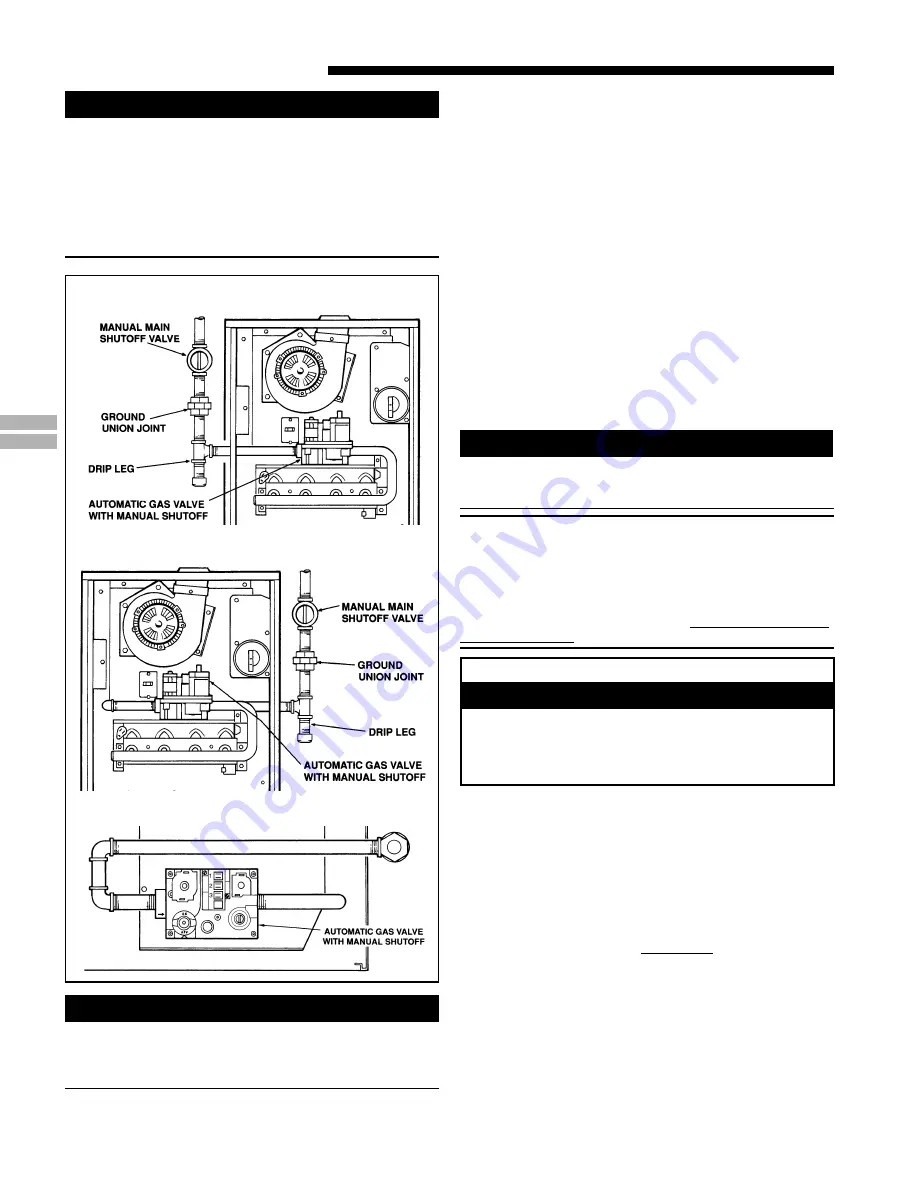
18
18-CD20D1-18
Installer’s Guide
LEFT SIDE PIPING (STANDARD)
TOP VIEW OF RIGHT SIDE PIPING
RIGHT SIDE PIPING (OPTIONAL)
j
▲
WARNING
!
FIRE OR EXPLOSION HAZARD
Failure to follow the safety warnings exactly could result in
serious injury, death or property damage.
Never test for gas leaks with an open flame. Use a com-
mercially available soap solution made specifically for the
detection of leaks to check all connections. A fire or
explosion may result causing property damage, personal
injury, or loss of life.
GAS PIPING
This unit is shipped standard for left side installation of gas
piping. A piping knockout is also provided in the right side
for an alternate piping arrangement. The installation of
piping shall be in accordance with piping codes and the
regulations of the local gas company. Pipe joint compound
must be resistant to the chemical reaction with liquefied
petroleum gases.
Refer to piping Table 8 for delivery sizes. Connect gas supply
to the unit, using a ground joint union and a manual shut-off
valve as shown in Figure 27. National codes require a
condensation drip leg to be installed ahead of the controls as
shown in Figure 27.
The furnace and its individual shut-off valve must be discon-
nected from the gas supply piping system during any pres-
sure testing of that system at test pressures in excess of
1/2 psig.
The furnace must be isolated from the gas supply piping by
closing its individual manual shut-off valve during any
pressure testing of the gas supply piping system at test
pressures equal to or less than 1/2 psig.
▲
CAUTION
!
Use a backup wrench on the gas valve when installing gas
piping to prevent damage to the gas valve and manifold
assembly.
NOTE:
Maximum pressure to the gas valve for natural gas is
13.8" W.C. Minimum pressure is 5.0" W.C. Maximum
pressure to the gas valve for propane is 13.8" W.C.
Minimum pressure is 11.0" W.C.
All gas fittings must be checked for leaks using a soapy
solution before lighting the furnace. DO NOT CHECK WITH
AN OPEN FLAME!
The following warning complies with State of California law, Proposition 65.
Hazardous Gases!
Exposure to fuel substances or by-products of incomplete
fuel combustion is believed by the state of California to
cause cancer, birth defects, or other reproductive harm.
▲
WARNING
!
COMBUSTION AND INPUT CHECK
1. Make sure all gas appliances are off except the furnace.
2. Clock the gas meter with the furnace operating (deter-
mine the dial rating of the meter) for one revolution.
3. Match the “Sec” column in the gas flow (in cfh) Table 13
with the time clocked.
4. Read the “Flow” column opposite the number of seconds
clocked.
5. Use the following factors if necessary:
For 1 Cu. Ft. Dial Gas Flow CFH =
Chart Flow Reading ÷ 2
For 1/2 Cu Ft. Dial Gas Flow CFH =
Chart Flow Reading ÷ 4
For 5 Cu. Ft. Dial Gas Flow CFH =
10X Chart Flow Reading ÷ 4
6. Multiply the final figure by the heating value of the gas
obtained from the utility company and compare to the
nameplate rating. This must not exceed the nameplate
rating.
▲
WARNING
!
TO PREVENT AN EXPLOSION OR POSSIBLE INJURY,
DEATH AND EQUIPMENT DAMAGE, DO NOT STORE
COMBUSTIBLE MATERIALS, GASOLINE OR OTHER
FLAMMABLE VAPORS OR LIQUIDS NEAR THE UNIT.