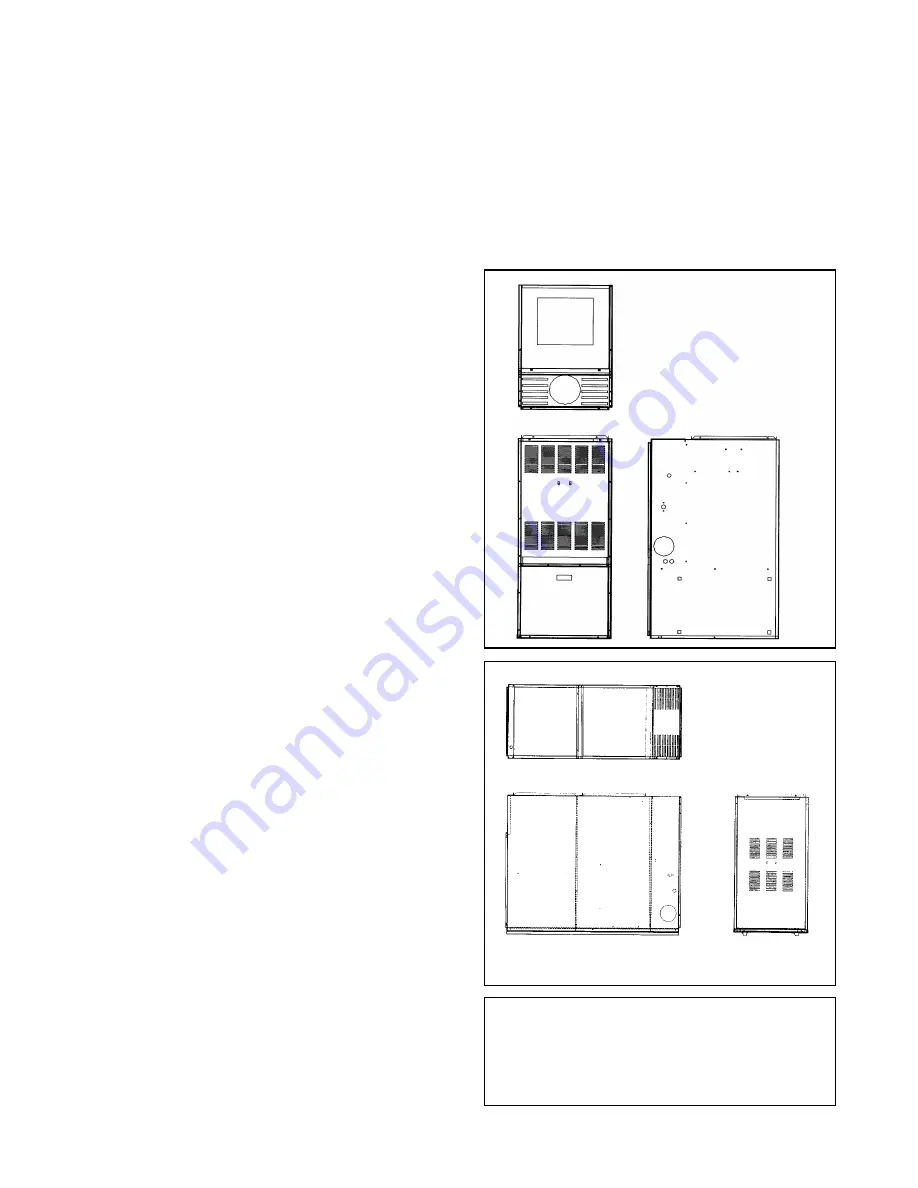
1
OIL-FIRED WARM AIR
FURNACE
P2HMX12F08001 P3HMX14F10001
P3HMX20F12001
(Upflow or Horizontal Models)
P3LBX12F08001 P3LBX14F12001
(Lowboy Models)
INTRODUCTION ...............................................................2
HEAT LOSS ......................................................................2
LOCATION OF UNIT ........................................................2
AIR CONDITIONING .........................................................4
COMBUSTION AIR ...........................................................4
CHIMNEY VENTING .........................................................4
OIL TANK..........................................................................6
PIPING INSTALLATION ...................................................6
ELECTRICAL CONNECTIONS ........................................6
CIRCULATING AIR BLOWER..........................................7
OIL BURNER ....................................................................8
FURNACE INSTALLATION SET-UP................................9
MAINTENANCE AND SERVICE.....................................10
OPERATING INSTRUCTIONS .......................................10
TABLE A-1: BECKETT OIL BURNER SET-UP .............11
TABLE A-2: DIRECT DRIVE BLOWER SET-UP ...........11
TABLE A-3: DIRECT DRIVE BLOWER
CHARACTERISTICS ......................................................12
GENERAL DIMENSIONS – P*HMX MODELS ...............14
GENERAL DIMENSIONS – P3LBX MODELS................15
APPENDIX B: WIRING DIAGRAM .................................16
WIRING NOTES..............................................................17
R7184 DETAILED SEQUENCE OF OPERATION..........18
TABLE C-1: ST9103 DETAILED SEQUENCE OF
OPERATION ...................................................................20
TABLE C-2: CAD CELL RESISTANCE ........................21
TABLE C-3: R7184 TROUBLESHOOTING...................21
TABLE C-4: SYSTEM AND GENERAL
TROUBLESHOOTING ....................................................24
AIR FILTER LOCATIONS...............................................27
REPAIR PART LIST – P3HMX14F10001 &
P3HMX20F12001 ............................................................28
REPAIR PART LIST – P3LBX12F08001A &
P3LBX14F12001A ..........................................................29
REPAIR PART LIST – P2HMX12F08001 .......................30
REPLACEMENT PART CONTACT INFORMATION ......31
INSTALLATION
MANUAL
CONTENTS
Read this manual completely before beginning
installation.
Important: These instructions must be kept with
the furnace for future reference.
Summary of Contents for P2HMX12F08001
Page 16: ...16 APPENDIX B WIRING DIAGRAM ...