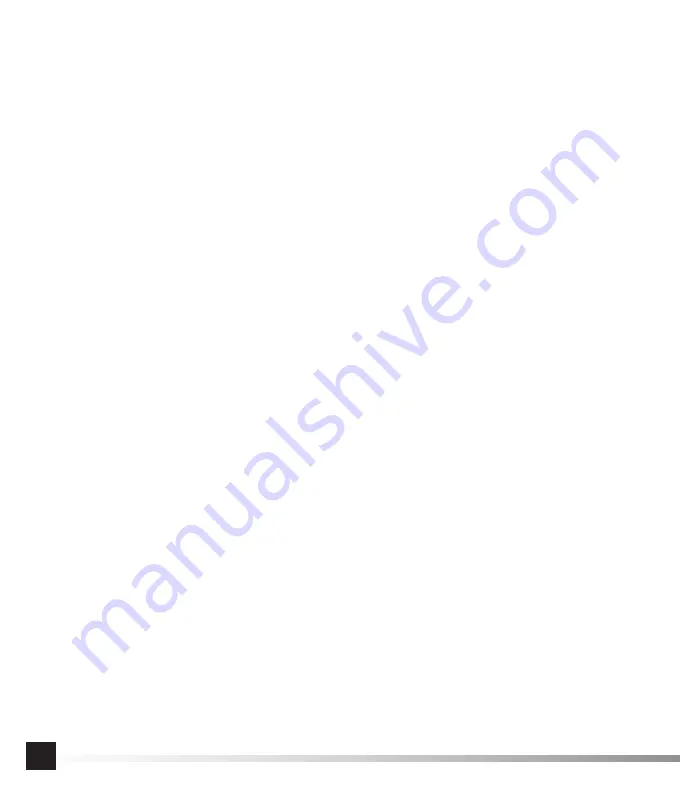
10
GB
O R I G I N A L I N S T R U C T I O N S
assembly power tool for threaded fasteners is operating. Select, maintain
and replace the consumable/inserted tool as recommended in the instruc-
tion handbook, to prevent an unnecessary increase in noise.
Vibration hazards
Exposure to vibration can cause disabling damage to the nerves and blood
supply of the hands and arms. Keep the hands away from the nutrunner
sockets. Wear warm clothing when working in cold conditions and keep your
hands warm and dry. If you experience numbness, tingling, pain or whitening
of the skin in your
fi
ngers or hands, stop using the assembly power tool for
threaded fasteners, tell your employer and consult a physician. Operate and
maintain the assembly power tool for threaded fasteners as recommended
in the instruction handbook, to prevent an unnecessary increase in vibration
levels. Do not use worn or ill-
fi
tting sockets or extensions, as this is likely to
cause a substantial increase in vibration. Select, maintain and replace the
consumable/inserted tool as recommended in the instruction handbook, to
prevent an unnecessary increase in vibration levels. Sleeve
fi
ttings should
be used where practicable. Support the weight of the tool in a stand, ten-
sioner or balancer, if possible. Hold the tool with a light but safe grip, taking
account of the required hand reaction forces, because the risk from vibration
is generally greater when the grip force is higher.
Additional safety instructions for pneumatic power tools
The following additional warnings (or equivalent) shall be given with all
pneumatic assembly power tools for threaded fasteners. Air under pres-
sure can cause severe injury:
- always shut o
ff
air supply, drain hose of air pressure and disconnect tool
from air supply when not in
use, before changing accessories or when making repairs;
- never direct air at yourself or anyone else.
Whipping hoses can cause severe injury. Always check for damaged or
loose hoses and
fi
ttings. Cold air shall be directed away from the hands.
Do not use quick-disconnect couplings at tool inlet for impact and air-hy-
draulic impulse wrenches. Use hardened steel (or material with compa-
rable shock resistance) threaded hose
fi
ttings. Whenever universal twist
couplings (claw couplings) are used, lock pins shall be installed and whip-
check safety cables shall be used to safeguard against possible hose-to-
tool and hose-and-hose connection failure. Do not exceed the maximum
air pressure stated on the tool. For torque-control and continuous-rotation
tools, the air pressure has a safety critical e
ff
ect on performance. There-
fore, requirements for length and diameter of the hose shall be speci
fi
ed.
Never carry an air tool by the hose.
CONDITIONS OF OPERATION
Make sure the source of compressed air may create appropriate working
pressure and guarantee the required
fl
ow of the air. If the pressure of the
air is too high, use a reduced with a safety valve. The pneumatic tool must
be powered through a
fi
lter and a greaser. It will guarantee simultaneously
cleanliness and lubrication of the air with oil. The state of the
fi
lter and
the greaser must be checked before each use and, if necessary, the
fi
lter
must be cleaned or the oil supplied in the greaser. It will guarantee proper
operation of the tool and will prolong its durability.
It is necessary to correctly adapt the reaction stick to a given task.
In the case additional holders or supporting stands are used; make sure
the tool has been correctly
fi
xed.
Adopt a correct position that will allow you to react to normal or unexpected
movements of the tool that may be caused by the turning moment.
Wrenches and other inserted tools must be adapted to work with pneu-
matic tools. The inserted tools must be in good working order and must be
cleaned and not damaged. Their size must
fi
t the dimensions of the collec-
tor. It is prohibited to modify the sockets of the wrenches or the collector.
OPERATION OF THE TOOL
Before each use of the tool, make sure that no element of the pneumatic
system is damaged. If there are any damaged elements, they should be
immediately replaced with new, faultless elements of the system.
Before each use of the pneumatic system, dry the humidity that conden-
sates inside the tool, the compressor and the dusts.
Connection of the tool to the pneumatic system
The drawing shows the recommended manner of connection of the tool
to the pneumatic system. The presented connection guarantees the most
e
ff
ective operation of the tool and will prolong its durability.
Place a couple of drops of oil (of viscosity SAE 10) to the air inlet.
Into the thread of the air inlet, turn strongly an appropriate terminal that
makes it possible to connect an air supply hose. (II)
Install an appropriate terminal on the collector of the tool.
During work
with pneumatic tools, use solely the equipment approved for work
with percussive tools.
Adjust a correct direction of rotation. „F” indicates clockwise rotation, „R”
– anticlockwise rotation.
Where it is possible, adjust the pressure (turning moment).
Connect the tool to the pneumatic system using a hose of internal diameter
1/2”. Make sure the resistance of the hose is at least 1.38MPa. (III)
Work with thimble percussive wrenches
Before screwing with a wrench starts, place the screw or the nut on the
thread manually (at least two turns).
Make sure the size of the wrench is correct for the screwed element. A
wrong size may be a cause of damage to the wrench, the screw or the nut.
Unscrewing and tightening
Adjust the pressure in the pneumatic system so as it does not exceed the
maximum value for the given tool.
Set up the appropriate direction of rotation for the tool (F – tightening, R –
unscrewing).
Install an appropriate thimble wrench on the collector of the tool. (IV)
Connect the key to the pneumatic system.
Place the key with the thimble installed on the element to be unscrewed
or tightened.
Gradually release the trigger of the tool.
Once the work has been concluded, dismantle the pneumatic system and
perform appropriate maintenance of the tool.
MAINTENANCE
Never use gasoline, solvents or another in
fl
ammable liquid to clean the tool.