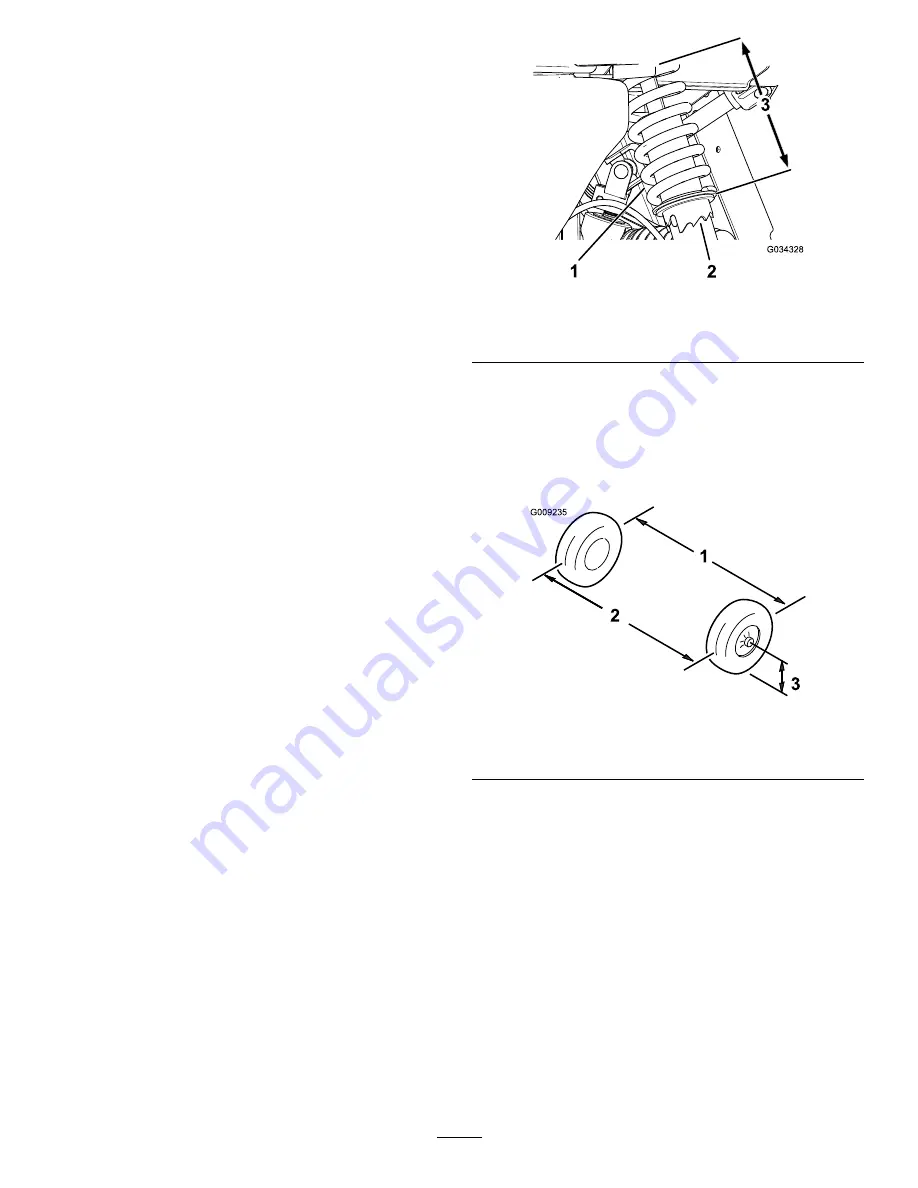
Drive System
Maintenance
Maintaining the Tires
Service Interval:
Every 100 hours—Check the condition of
the tires and rims.
Every 100 hours—Torque the wheel-lug nuts.
1.
Inspect the tires an rims for signs of wear and damage.
Note:
Operating accidents, such as hitting curbs, can
damage a tire or rim and also disrupt wheel alignment,
so inspect tire condition after an accident.
2.
Torque the wheel-lug nuts to 108 to 122 N∙m (80 to
90 ft-lb).
Adjusting the Front Wheel
Toe-in
Service Interval:
Every 100 hours/Yearly (whichever comes
first)—Check the front wheel toe-in.
Important:
You need Toro Tool No. 6010 from your
Toro Distributor to perform this procedure.
The toe-in should be 0 +/– 3 mm (0 +/– 1/8 inch).
•
Check the tire pressure to ensure that the front tires are
inflated to 165 to 207 kPa (24 to 30 psi).
•
Either, add weight to the driver's seat equal to the average
operator who will run the machine, or have an operator
sit on the seat. The weight or operator must remain on
the seat for the duration of the procedure.
•
On a level surface, roll the machine straight back 2 to 3
m (6 to 10 ft) and then straight forward to the original
starting position. This allows the suspension to settle into
the operating position.
•
Measure the toe-in with the wheels facing straight ahead.
Adjust the riding height to the desired position by performing
the following procedure:
1.
Using Toro Tool No. 6010, rotate the collar on the
shock absorber to change the length of the spring
(
).
Figure 43
1.
Shock-absorber spring
3.
Spring length
2.
Collar
2.
On a level surface, roll the machine straight back 2 to 3
m (6 to 10 ft) and then straight forward to the original
starting position.
3.
Measure the distance between both of the front tires at
the axle height at both the front and rear of the front
tires (
G009235
1
2
3
Figure 44
1.
Tire center line—back
3.
Axle center line
2.
Tire center line—front
4.
If the measurement does not fall within 0 +/– 3 mm
(0 +/– 1/8 inch), loosen the jam nuts at the outer end
of the tie rods (
39
Summary of Contents for WORKMAN GTX 07131
Page 46: ...Notes...