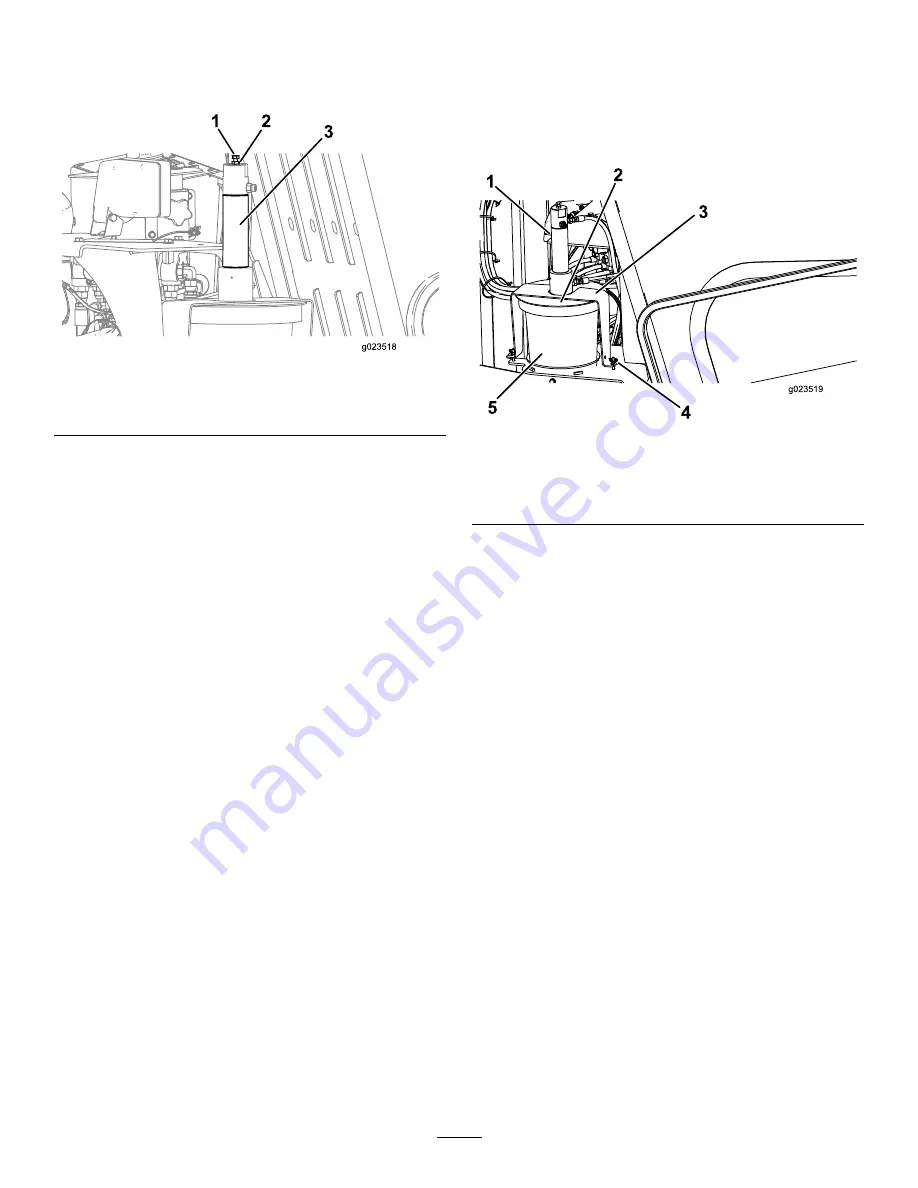
Adjusting the TJC-spray Volume
1.
Loosen the jam nut on the adjustment bolt located on
top of the TJC-applicator piston (
Figure 88
1.
Adjustment bolt
3.
TJC-applicator piston
2.
Jam nut
2.
Adjust the bolts as follows:
•
To increase the applied volume of compound,
thread the bolt out (up).
•
To decrease the applied volume of compound,
thread the bolt in (down).
3.
When you have attained the desired application volume,
tighten the jam nut to secure the adjustment.
Filling the TJC Applicator
1.
Stop the machine and stop the engine.
2.
Open the stake-down-guard door.
3.
Loosen the wing nuts securing the cover straps to the
machine (
).
Figure 89
1.
TJC-applicator piston
4.
Wingnut
2.
Cover
5.
TJC bucket
3.
Strap
4.
Rotate the cover and pull the cover straps off the
retaining bolts (
5.
Lift the cover assembly off and out of the empty
thread-joint-compound bucket (
6.
Replace the empty bucket with a new full bucket.
7.
Place the plunger into the new bucket and lower the
cover assembly onto the bucket (
).
8.
Slide the cover straps over the retaining bolts, and
rotate the cover to seat the straps on the bolts (
9.
Tighten the wing nuts.
75