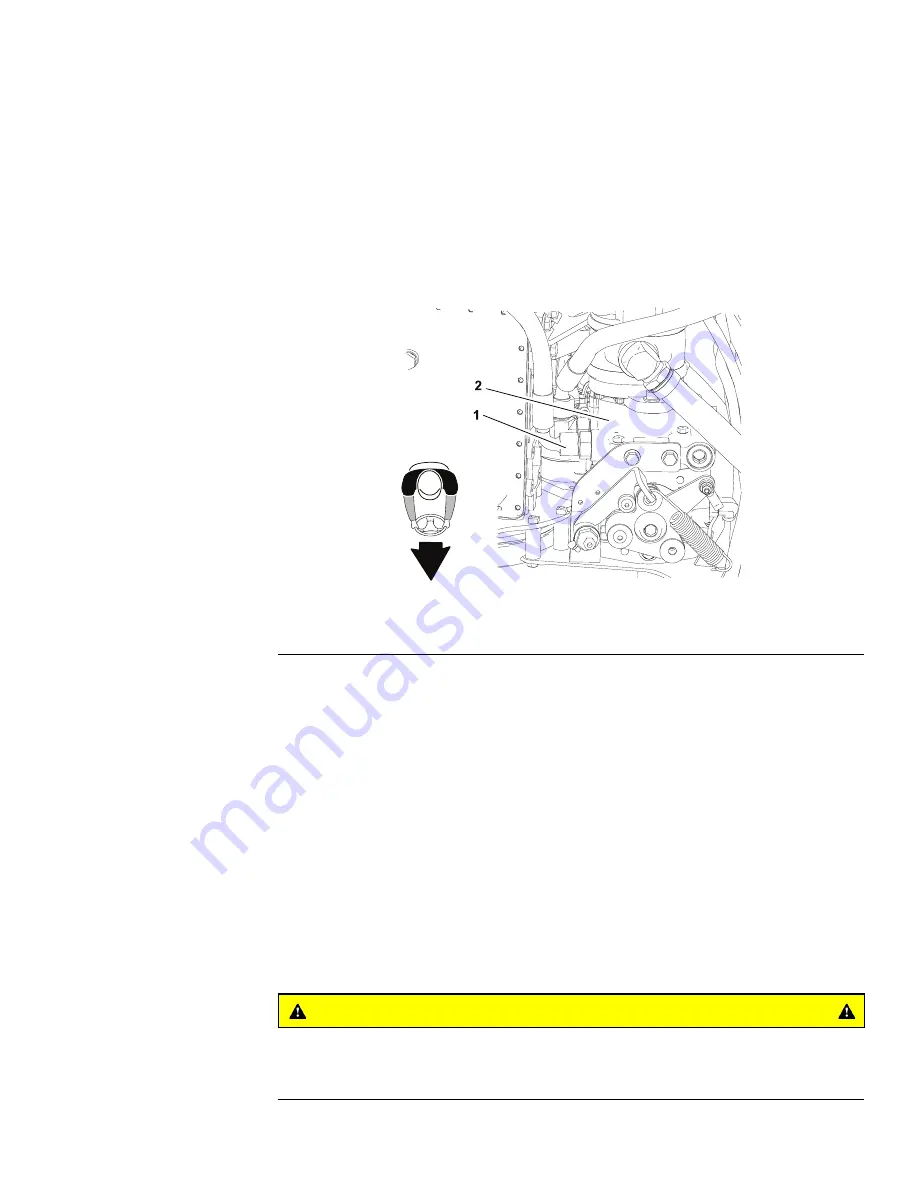
1. Park machine on a level surface with the cutting units lowered and the reel
engage/disengage switch is in the disengage position. The engine should be
off and the parking brake engaged.
2. Read
Precautions for Hydraulic Testing (page 5–27)
.
3. Make sure that the traction pedal is adjusted to the neutral position.
4. Attach a heavy chain to the rear of the machine frame and an immovable
object to prevent the machine from moving during testing.
Front Wheel Motor Tests
Hydraulic fluid flows through both front wheel motors (in parallel) before passing
through the rear wheel motor (in series). To accurately test the front wheel
motors, the rear wheel motor must be removed from the traction circuit.
g344857
Figure 40
1.
Lower hydraulic fitting
2.
Piston pump
1. Disconnect the hose from the lower hydraulic fitting on the bottom of the
hydrostat (
Note:
An alternate testing location would be at the hydraulic tube supplying
the front wheel motors under the left floor plate.
2. Install the flow tester between the hydrostat and the disconnected hydraulic
line. Make sure that the tester flow control valve is fully open.
3. Disconnect both hydraulic lines from the rear wheel motor, then reconnect the
lines to each other. Plug ports in the wheel motor to prevent contamination.
4. Chock the front wheels to prevent wheel rotation.
5. Start the engine. Move throttle to full speed (2650 ± 50 RPM).
6. Make sure that the hydraulic fluid is at normal operating temperature by
operating the machine for approximately 10 minutes. Make sure that the
hydraulic tank is full.
7. Verify with a phototach that the pump speed is approximately 3100 RPM.
CAUTION
Use extreme caution when performing wheel motor tests. The wheel
motors will be trying to move the machine forward.
Reelmaster
®
3100-D/3105-D
Page 5–33
Hydraulic System: Testing
20252SL Rev A
Summary of Contents for 03200 Reelmaster 3100-D
Page 4: ...NOTES NOTES Page 4 Reelmaster 3100 D 3105 D 20252SL Rev A ...
Page 6: ...g341979 Figure 1 Preface Page 6 Reelmaster 3100 D 3105 D 20252SL Rev A ...
Page 10: ...Preface Page 10 Reelmaster 3100 D 3105 D 20252SL Rev A ...
Page 20: ...Safety Safety and Instructional Decals Page 1 10 Reelmaster 3100 D 3105 D 20252SL Rev A ...
Page 44: ...Specifications and Maintenance Special Tools Page 2 24 Reelmaster 3100 D 3105 D 20252SL Rev A ...
Page 224: ...Hydraulic System Service and Repairs Page 5 148 Reelmaster 3100 D 3105 D 20252SL Rev A ...
Page 385: ......