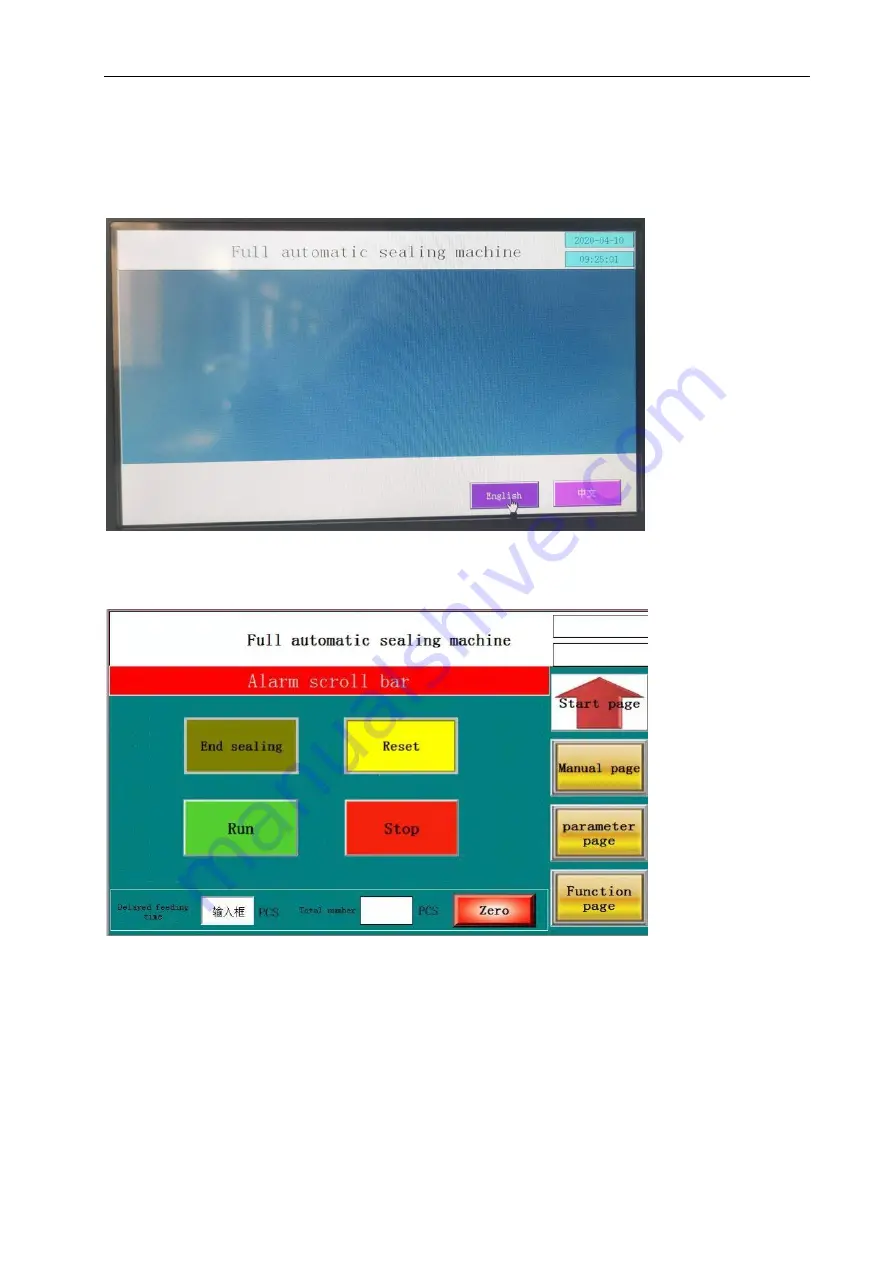
ZF-A5645-MANUAL
2, touch screen operation and its function explanation
(1) to open the main power switch, touch screen display the home page as shown
Select the “automatic page” and the submenu appears as shown in Figure 5.3
A. Run: click the "Run" button, and then the device enters the running state
B. Stop: click the “stop” button, and the device stops
C. Reset: when the device alarm, click the "reset" button to clear the alarm and the
device enters the normal preparation state.
D. Manual sealing: click it to manual seal
5.2
Summary of Contents for ZF-A5645
Page 6: ...ZF A5645 MANUAL 1515 750 1 7 9 5 1570 880 400 C C 2 Machine Size Unit mm...
Page 7: ...ZF A5645 MANUAL 3 Operate Panel...
Page 38: ...ZF A5645 MANUAL Nine Circuit Diagram...
Page 39: ...ZF A5645 MANUAL Ten The explosion figure 1 Overall part diagram...
Page 40: ...ZF A5645 MANUAL 2 Control electric box components...
Page 41: ...ZF A5645 MANUAL 3 Safe cover components...
Page 42: ...ZF A5645 MANUAL 4 Sealing components...
Page 43: ...ZF A5645 MANUAL 5 Behind conveyor components...
Page 44: ...ZF A5645 MANUAL 6 Frame components...
Page 45: ...ZF A5645 MANUAL 7 Pull film components...
Page 46: ...ZF A5645 MANUAL 8 Recycle feeding components...
Page 47: ...ZF A5645 MANUAL 9 Electric box components...
Page 48: ...ZF A5645 MANUAL 10 Sending feeding components...
Page 49: ...ZF A5645 MANUAL...
Page 50: ...ZF A5645 MANUAL 11 Front conveyor components...
Page 51: ...ZF A5645 MANUAL...