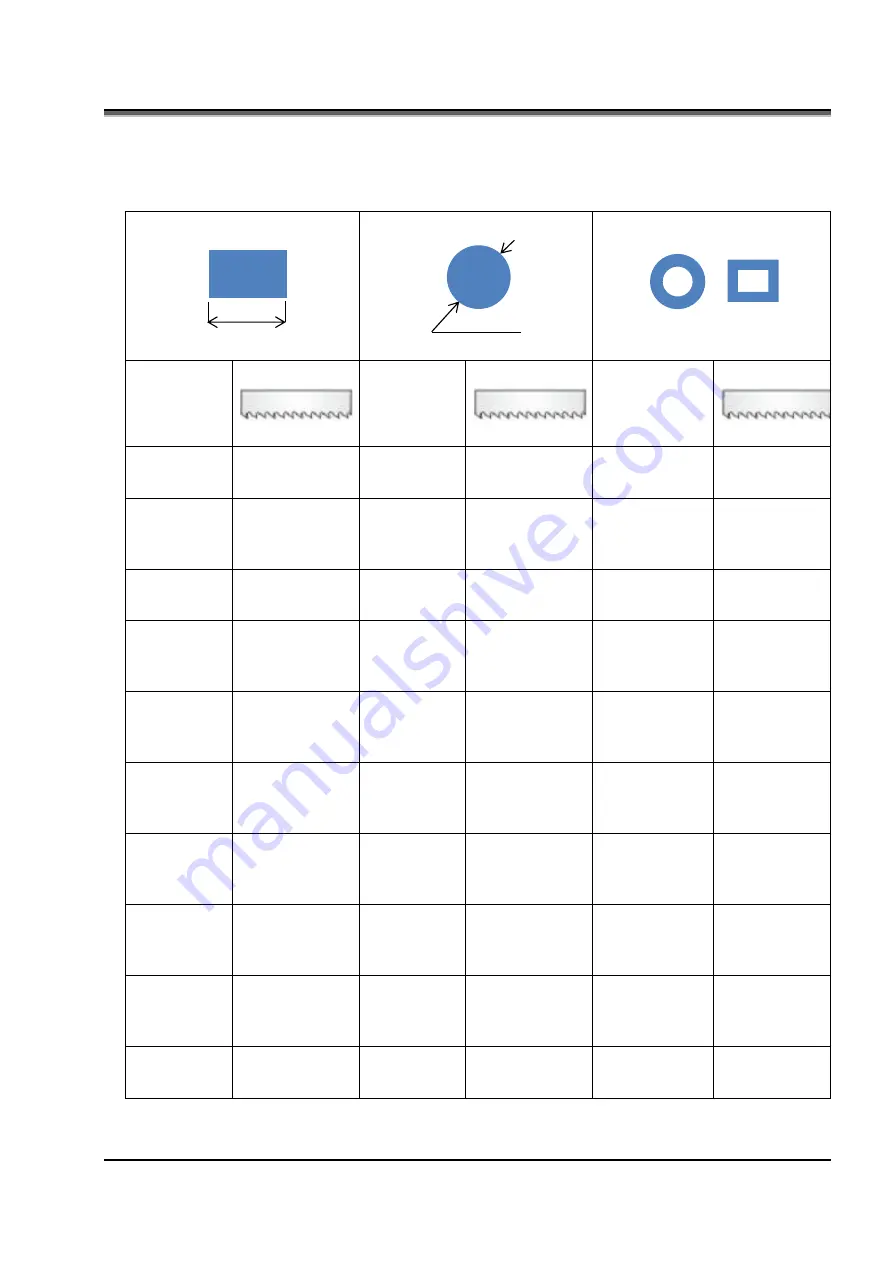
6
、
Saw Band
44
6.1 Selecting the tooth of Saw Band
WT
wide
(
mm/in
)
Φ
(
mm/in
)
Wall thickness
(
mm/in
)
1
~
5/
3/64~13/64
14/18T
1
~
5/
3/64~13/64
14/18T
1
~
3/
3/64~1/8
10/14T
6
~
7/
15/64~9/32
10/14T
6
~
10/
15/64~25/6
4
10/14T
4/ 5/32
8/12T
8
~
13/
5/16~33/64
8/12T
11
~
16/
7/16~5/8
8/12T
5
~
6/
13/64~15/64
6/10T
14
~
16/
35/64~5/16
6/10T
17
~
21/
43/64~13/1
6
6/10T
7
~
9/
9/32~11/32
5/8T
17
~
25/
43/64~1
5/8T
22
~
30/
55/64~1-
3/16
5/8T
10
~
18/
25/64~45/64
4/6T
26
~
53/ 1-
1/64~2-
5/64
4/6T
31
~
69/ 1-
7/32~223/3
2
4/6T
19
~
33/
3/4~1-19/64
3/4T
54
~
114/
2-1/8~4-
31/64
3/4T
70
~
144/
2-3/4~5-
21/32
3/4T
>34 1-
11/32
2/3T
115
~
205/
4-33/64~8-
1/16
2/3T
145
~
230/
5-45/64~9-
1/16
2/3T
----
----
206
~
381/
8-7/64~15
1.4/2.5T
231
~
381/9-
3/32~15
1.4/2.5T
----
----
>382/15
1/1.5T
>382/15
1/1.5T
----
----
wide
Φ