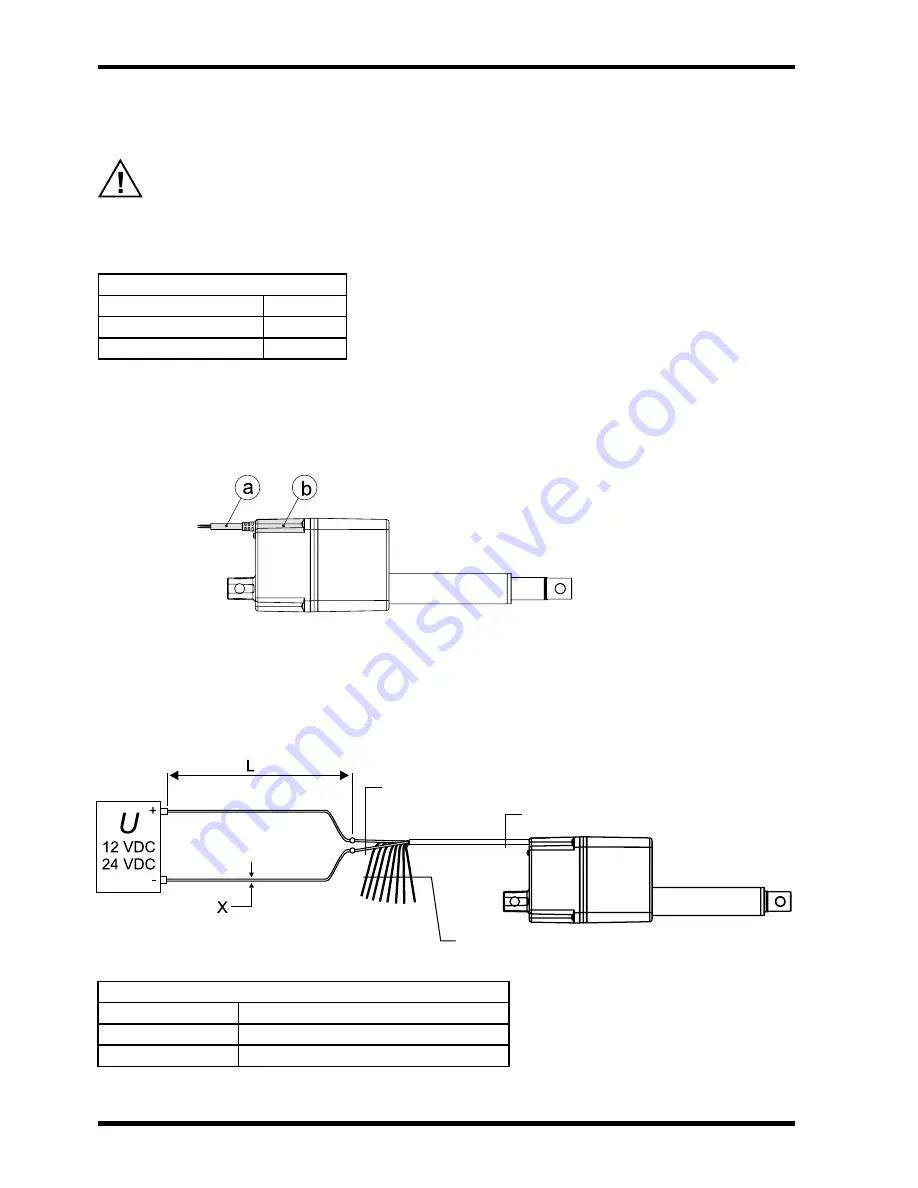
Thomson
Thomson Electrak
®
MD Actuator - Installation Manual - 2020-02
9
4.5 Electrical installation
4.5.1 General notes
• Make sure the leads/cables leading to the motor can handle the maximum motor current.
• An emergency stop is recommended to reduce the chance of a crushing hazard.
• Never work on the actuator or the wiring with the power switched on!
4.5.2 Fuse size
Protect the actuator and the wiring by using a slow blow fuse between the actuator and the power source.
4.5.3 Electrical connections
The actuator is supplied with a cable (a) to which all connections are done. The cable has flying leads in
one end for customer connections. In the other end the cable is integrated in to the cable connector cover
plate (b) (section 4.4.4). The plug in connector allows replacing the actuator without disconnecting the flying
leads.
4.5.4 Lead cross sections
To avoid malfunction due to voltage drop the cross section of the leads between the actuator power
leads and the power source must be of sufficient size. For longer cables than stated in the table,
calculations based on the supply voltage, the current draw, the length of the cables and the ambient
temperature must be done.
Power Lead Cross Sections
Length of cable (L)
Min. allowed cross section (X)
0 - 3 m
1.5 mm
2
[AWG 16]
3 - 6 m
2.5 mm
2
[AWG 14]
Recommended Fuse Size
Actuator supply voltage
Fuse size
12 VDC
10 A
24 VDC
5 A
Power leads
0.75 mm
2
[AWG 18]
Cable
X
Signal leads
0.35 mm
2
[AWG 22]