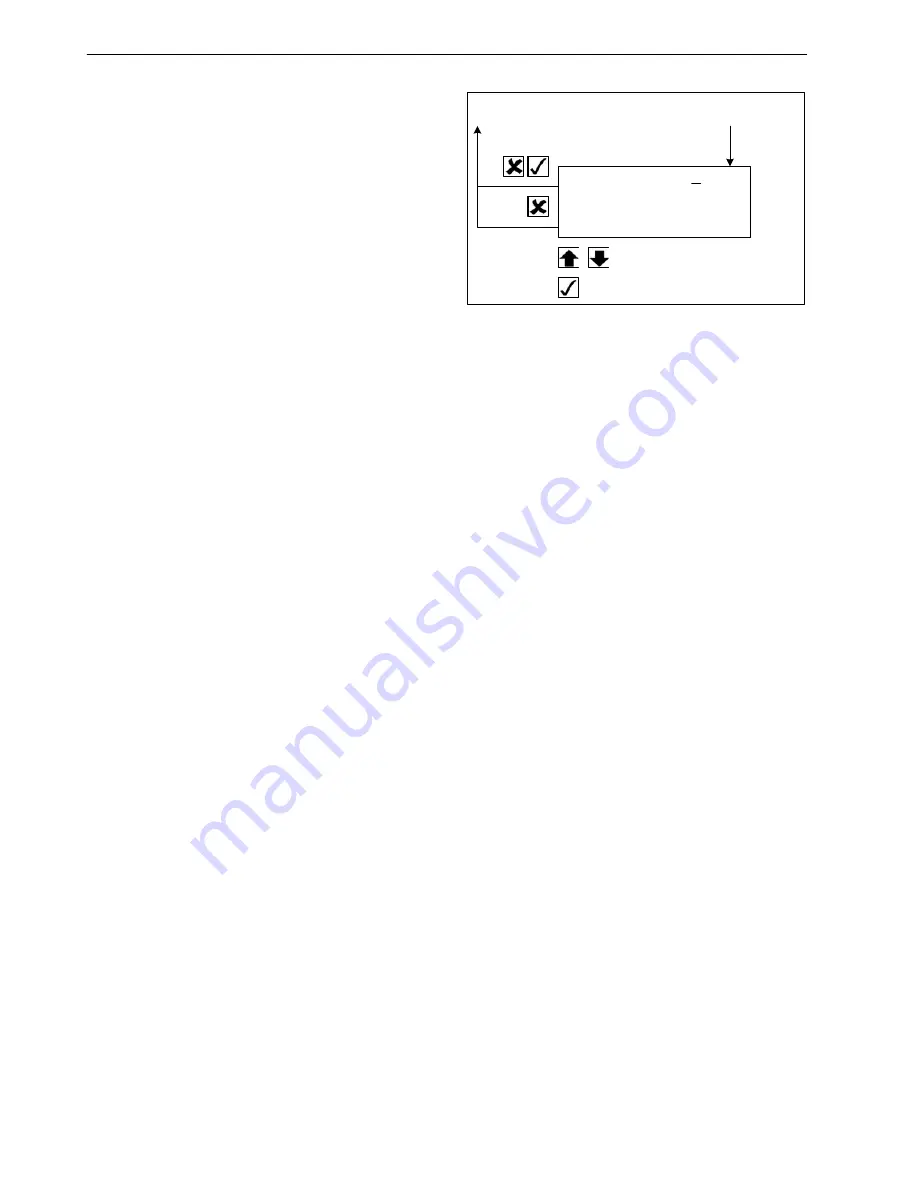
Operating Instructions
64
Date/Time
The Date/Time submenu is used to set the clock in
the controller. To enter the Date/Time submenu
and set the clock complete the following steps:
1. Place the On/Off switch in the “ON” position.
2. Press the
E
NTER
key or the
E
SCAPE
key to enter
the Main Menu, if necessary.
3. Press the
U
P
or
D
OWN
key to scroll up or down
through the Main Menu to the Commands
Menu.
4. Press the
E
NTER
key to enter the Commands
Menu.
5. The PTI submenu will be displayed.
6. Press the
U
P
or
D
OWN
key to scroll up or down
through the Commands Menu to the System
Setup submenu.
7. Press the
E
NTER
key to enter the System Setup
submenu.
8. Press the
U
P
or
D
OWN
key to scroll up or down
through the System Setup submenu to the
Date/Time submenu.
9. Press the
E
NTER
key to enter the Date/Time
submenu to set the clock.
10. Press the
E
NTER
key to move the cursor (to the
right or down at the end of a row) to select the
value you want to change.
NOTE: The
E
NTER
key does not move the
cursor to the right in the Time value. You
must use the
U
P
or
D
OWN
keys to scroll the
total Time value up or down.
11. Press the
U
P
or
D
OWN
key to scroll the selected
value up or down to the new setting.
12. Repeat steps 10 and 11 until you have changed
all the values to the new settings.
13. Press the
E
SCAPE
key and the
E
NTER
key at the
same time to save the new settings and return
to the System Setup submenu.
NOTE: Press the
E
SCAPE
key to return to the
System Setup submenu without saving the
new settings.
Figure 28: Date/Time
YEAR: 200
6
MONTH: 03
DATE: 22
TIME: 14.08
Save changes and return to
"DATE/TIME" prompt of
"MISC. FUNCTIONS" menu
ESC
From "DATE/TIME" prompt of
"MISC. FUNCTIONS" menu.
Scrolls values up/down
Moves cursor right
ARA736
Summary of Contents for SGCO 3000
Page 4: ......
Page 12: ...SGCO 3000 Genset Addendum 12...
Page 14: ...Genset Model Features 14...
Page 22: ...Service Guide 22...
Page 32: ...Unit Description Features Options 32...
Page 78: ...Operating Instructions 78...
Page 86: ...Electrical Maintenance 86...
Page 114: ...Engine Maintenance 114...
Page 124: ...Alternator Operation and Diagnosis 124...
Page 130: ...Structural Accessory Maintenance 130...
Page 138: ...Index 138...
Page 140: ...Electrical and SG Menu Flow Diagrams 140...
Page 141: ...141 SGCO 3000 Wiring Diagram Page 1 of 1...