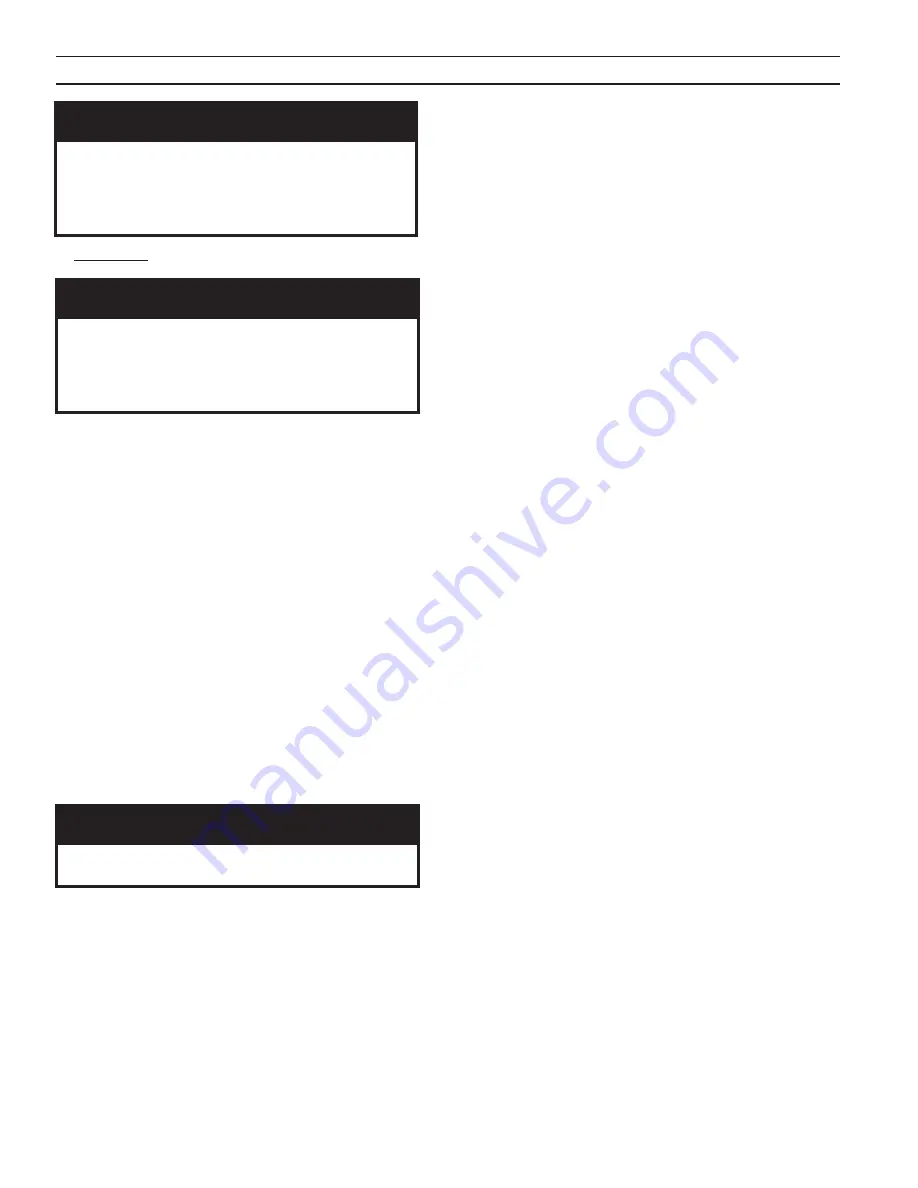
10
A.
VENTING
WARNING
Improper venting may result in property damage
and the release of flue gasses which contain
deadly carbon monoxide (CO) into the building,
which can cause severe personal injury and/or
death.
1. General Venting Requirements
In order to properly vent this boiler, the installer
must select and install a vent system that meets all
requirements specified in this section (VENTING) as
well as following the instructions provided by the vent
system manufacturer.
a. The vent system shall be designed and constructed in
accordance with the National Fuel Gas Code/NFPA 54
ANSI Z223.1 and applicable local building codes to
develop a positive flow adequate to convey flue or vent
gasses to the outdoors.
b. If this boiler is being installed in Massachusetts, follow
the Massachusetts Code instructions printed later in this
section.
c. Consult the vent pipe manufacturer’s instructions for
vent system assembly and system specific installation
requirements.
WARNING
Vent pipe system must be made of materials
approved for use with condensing flue gasses.
d. Vent pipe system shall be acceptable for use with boiler
fuel type.
e. Vent pipe system shall be compatible either by directly
connecting, or by use of an adapter, to the boiler vent
connection.
i. This boiler is shipped with an AL 29-4C® Heat-
Fab Saf-T-Vent connection and a screened 90° vent
termination. These items are not a complete flue ducting
system.
ii. Alteration of the boiler vent connection is
prohibited.
f. Do not reduce the diameter of the vent pipe. The vent
pipe must not be smaller than the vent connector on the
boiler.
g. Vent pipe system must be adequately supported at
intervals no less than five (5) feet apart. The completed
vent system must be rigid and able to withstand impacts
without collapse.
h. If any point of the vent pipe system is higher than the
boiler flue collar, the vent system must have adequate
condensate drain loop(s) to prevent condensate from
running back into the boiler.
i. It is permissible to run vent pipe through a vertical
or horizontal chase provided minimum clearances to
combustible materials are maintained.
j. The minimum clearance to combustible material is
six (6) inches, unless otherwise specified by the vent
system manufacturer.
k. Horizontal vent pipe must slope no less than one (1)
inch in four (4) feet of run.
l. The vent termination location is restricted as follows:
i. Minimum twelve (12) inches above grade plus
normally expected snow accumulation or seven (7) feet
above grade if located adjacent to public walkways.
DO NOT INSTALL over public walkway where local
experience indicates condensation or vapor from the
boiler creates a nuisance or hazard.
ii. Minimum three (3) feet above any forced air inlet
located within ten (10) feet of the vent termination.
iii. Minimum four (4) feet below, four (4) feet
horizontally or one (1) foot above any door, window or
gravity air inlet.
iv. Minimum four (4) feet horizontally from electric
meters, gas meters, regulators and relief valves. This
distance may be reduced if equipment is protected from
damage due to condensation or vapor by enclosure,
overhangs, etc.
v. Minimum twelve (12) inches from corners of
building.
m. Use appropriately designed thimbles when passing
through combustible walls or roofs.
n. Install fire-stops where vent passes through floors,
ceilings or framed walls. The fire-stop must close the
opening between the vent pipe and the structure.
o. Enclose vent passing through occupied or unoccupied
spaces above the boiler with materials having a fire
resistance rating at least equal to the rating of the
adjoining floor or ceiling. Maintain minimum clearance
to combustible materials.
III. Installation
NOTICE
Although details for indoor installation may be
rarely applicable, Thermal Solutions recognizes
that instances may exist where such details are
required and have been included within this
manual for this purpose.
Summary of Contents for EVO-1000
Page 13: ...13 Figure 4 Vertical Pressurized Venting...
Page 15: ...15 Figure 5 Typical Negative Pressure Conventional Venting...
Page 17: ...17 Figure 7 Vertical Air Intake Piping...
Page 26: ...26 Figure 9a Standard UL FM CSD 1 Wiring Diagram on off EVO 500 2000...
Page 27: ...27 Figure 9b Standard UL FM CSD 1 Wiring Diagram Modulation EVO 500 2000...
Page 30: ...30 Figure 11 Modular System Horizontal Air Intake Piping...
Page 31: ...31 Figure 12 Modular System Vertical Air Intake Piping...
Page 32: ...32 Figure 13 Modular System Typical One Pipe Water Piping...
Page 33: ...33 Figure 14 Modular System Typical Primary Secondary Water Piping...
Page 34: ...34 Figure 15 Modular System Typical Primary Secondary without System Pump...
Page 35: ...35 Figure 16 Modular System Typical Reverse Return Water Piping...
Page 36: ...36 Figure 17 Modular System Reverse Return with System Pump Only...
Page 37: ...37 Figure 18 Modular System Typical Primary Secondary with Reverse Return...
Page 47: ...47 This Page Intentionally Left Blank...
Page 48: ...48 Troubleshooting Guide B Troubleshooting Guide...
Page 49: ...49 Troubleshooting Guide...
Page 53: ...53 This Page Intentionally Left Blank...
Page 54: ...54 Figure 19 Combustion Chamber Assembly...
Page 56: ...56 Figure 20 Burner Assembly FRONT VIEW TOP VIEW...
Page 58: ...58 Figure 21 UL FM CSD 1 Main Gas Train Assembly...
Page 60: ...60 Figure 22a DB B DB B w POC Gas Train 500 750 Figure 22b DB B DB B w POC Gas Train 1000 2000...
Page 62: ...62 Figure 23 Jacket Panels 4D 4J 4C 4B 4F 4I 4G 4E 4R 4K 4H 4J 4N 4M 4L 4Q 4A 4P 4P...
Page 64: ...64 Figure 24a Control Panel Assembly On Off...
Page 66: ...66 Figure 24b Control Panel Assembly Modulation...
Page 68: ...68 Figure 25 Bishop Pilot Assembly...
Page 72: ...72 NOTES...
Page 73: ...73 NOTES...
Page 74: ...74 NOTES...
Page 75: ...75 NOTES...