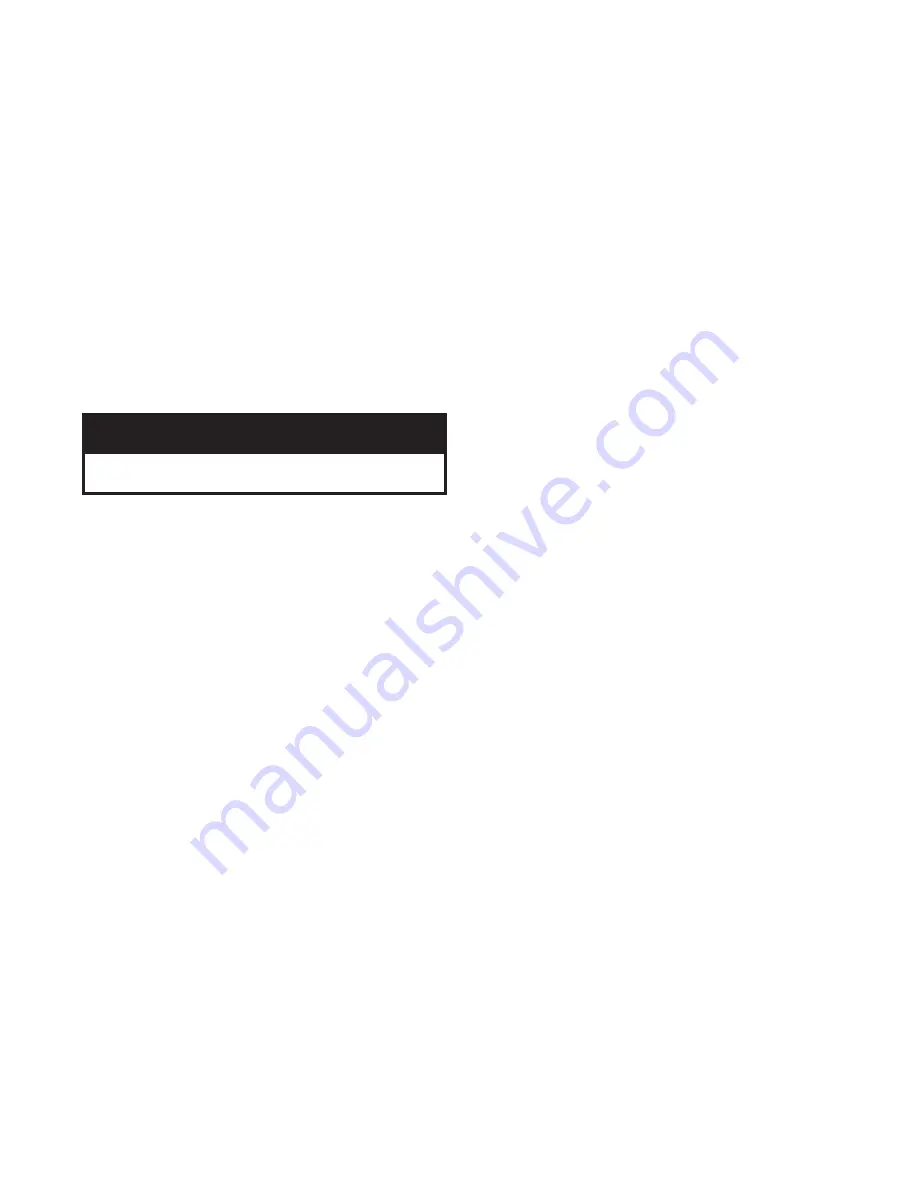
11
p. Locate vent terminal above combustion air intake
terminal (if used) and no closer than one (1) foot
horizontally.
q. Vertical venting requires flashing and a storm collar to
prevent moisture from entering the structure.
r. Vertical vent termination must be at least two (2)
feet plus the expected snow accumulation above roof
penetration height.
s. This boiler’s venting may be Category IV (positive
vent pressure, flue condensing) or Category II (non-
positive vent pressure, flue condensing), with regards to
National Fuel Gas Code/NFPA 54 ANSI Z223.1.
2. Positive Pressure Venting Requirements
a. Vent pipe system must be fully sealed.
WARNING
Do not use vent dampers or barometric dampers
with positive pressure vent systems.
b.
Direct vent applications:
For direct vent (ducted
combustion air) installations, the maximum vent length
is 50 equivalent feet. The vent length is equal to the
total length of straight pipe plus the equivalent length of
vent fittings.
c.
Non-direct vent applications:
For non-direct vent
installations (those without ducted combustion air),
design the vent system so that the pressure measured at
the outlet of the boiler is between 0”w.c. and 0.3”w.c. at
high fire.
d. For sidewall venting, slope pipe toward vent
termination, if possible.
e. See Figures 2, 3 and 4 for examples of positive pressure
venting arrangements.
3. Negative Pressure (Conventional) Venting
Requirements
This section outlines requirements for conventional
venting installations, where a negative pressure at
the boiler flue outlet is achieved by means of natural
convection through a vertical length of vent pipe or
lined chimney.
a. Refer to Figure 5 for an example of a typical
conventional venting arrangement.
b. A lined chimney or vertical length of vent pipe may be
used. Chimney lining must be acceptable for use with
condensing flue gas.
c. The minimum chimney/vertical vent height is 15 feet.
d. Install a condensate drain to collect any condensate that
may form in the lined chimney/vertical vent.
e. Install a double acting barometric damper with integral
flue spillage interlock.
f. The chimney/vertical vent and flue connector must be
sized and configured to provide a minimum - 0.04 inch
w.c. pressure (draft) at the boiler flue outlet.
g. The chimney must be protected from down drafts, rain
and debris by using a chimney cap or star.
4. General Guidelines
a. This boiler has been certified with AL29-4C® venting.
Select a vent material that is approved for use with
condensing flue gasses.
b. Install vent system before installing air intake, water,
gas or electrical connections.
c. For instances where the vent system manufacturer’s
instructions do not make a specification, refer to the
below points.
i. Make sure pipe and fittings are clean by swabbing
with alcohol. Use Dow Corning 736 or 732 RTV,
Polybar #500 RTV or Sil-bond 4500 or 6500 to seal
vent pipe.
ii. Refer to the appropriate drawings in this section
of this manual to determine common acceptable
configurations of venting system.
5. IMPORTANT
The
Commonwealth of Massachusetts
requires
compliance with regulation 248 CMR 4.00 and 5.00
for installation of side-wall vented gas appliances as
follows:
a. For all side wall horizontally vented gas fueled
equipment installed in every dwelling, building or
structure used in whole or in part for residential
purposes, including those owned or operated by the
Commonwealth and where the side wall exhaust
vent termination is less than seven (7) feet above
finished grade in the area of the venting, including
but not limited to decks and porches, the following
requirements shall be satisfied:
1. INSTALLATION OF CARBON MONOXIDE
DETECTORS. At the time of installation of the side
wall horizontal vented gas fueled equipment, the
installing plumber or gasfitter shall observe that
Summary of Contents for EVO-1000
Page 13: ...13 Figure 4 Vertical Pressurized Venting...
Page 15: ...15 Figure 5 Typical Negative Pressure Conventional Venting...
Page 17: ...17 Figure 7 Vertical Air Intake Piping...
Page 26: ...26 Figure 9a Standard UL FM CSD 1 Wiring Diagram on off EVO 500 2000...
Page 27: ...27 Figure 9b Standard UL FM CSD 1 Wiring Diagram Modulation EVO 500 2000...
Page 30: ...30 Figure 11 Modular System Horizontal Air Intake Piping...
Page 31: ...31 Figure 12 Modular System Vertical Air Intake Piping...
Page 32: ...32 Figure 13 Modular System Typical One Pipe Water Piping...
Page 33: ...33 Figure 14 Modular System Typical Primary Secondary Water Piping...
Page 34: ...34 Figure 15 Modular System Typical Primary Secondary without System Pump...
Page 35: ...35 Figure 16 Modular System Typical Reverse Return Water Piping...
Page 36: ...36 Figure 17 Modular System Reverse Return with System Pump Only...
Page 37: ...37 Figure 18 Modular System Typical Primary Secondary with Reverse Return...
Page 47: ...47 This Page Intentionally Left Blank...
Page 48: ...48 Troubleshooting Guide B Troubleshooting Guide...
Page 49: ...49 Troubleshooting Guide...
Page 53: ...53 This Page Intentionally Left Blank...
Page 54: ...54 Figure 19 Combustion Chamber Assembly...
Page 56: ...56 Figure 20 Burner Assembly FRONT VIEW TOP VIEW...
Page 58: ...58 Figure 21 UL FM CSD 1 Main Gas Train Assembly...
Page 60: ...60 Figure 22a DB B DB B w POC Gas Train 500 750 Figure 22b DB B DB B w POC Gas Train 1000 2000...
Page 62: ...62 Figure 23 Jacket Panels 4D 4J 4C 4B 4F 4I 4G 4E 4R 4K 4H 4J 4N 4M 4L 4Q 4A 4P 4P...
Page 64: ...64 Figure 24a Control Panel Assembly On Off...
Page 66: ...66 Figure 24b Control Panel Assembly Modulation...
Page 68: ...68 Figure 25 Bishop Pilot Assembly...
Page 72: ...72 NOTES...
Page 73: ...73 NOTES...
Page 74: ...74 NOTES...
Page 75: ...75 NOTES...