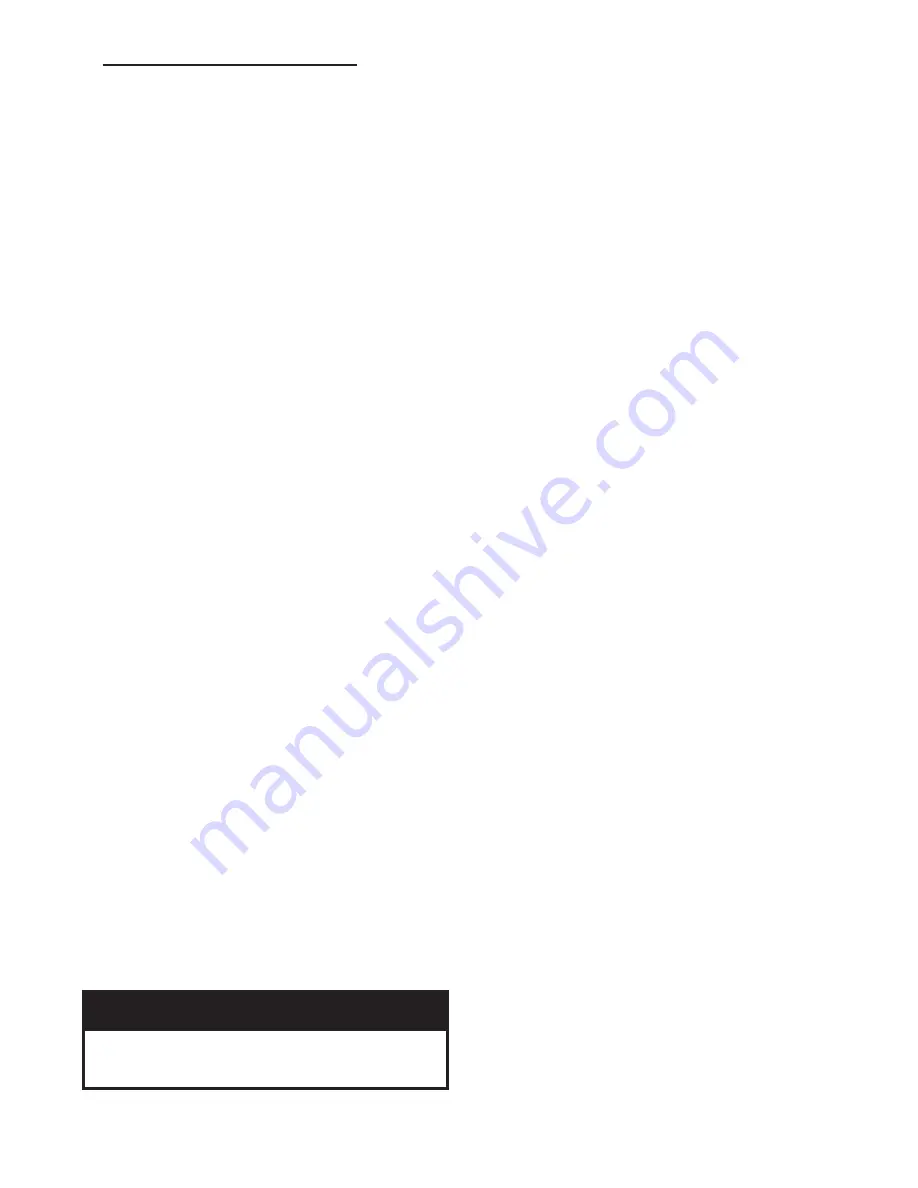
51
D. Inspection and Cleaning Procedures
Air Filter:
A. Perform a visual inspection of air filter and
replace as necessary.
1. Remove upper front panel.
2. Remove red tube from nipple on filter assembly.
3. Remove wing nut.
4. Remove filter assembly from boiler. Remove the
blower filter front plate, if necessary.
5. Remove foam pre-filter and wash with soap and
water.
6. Replace primary filter as necessary.
Pilot Flame:
A. Perform a visual inspection of pilot burner
flame.
1. Refer to the flame safeguard instruction manual
and conduct a pilot turndown test.
2. Observe pilot operation and record pilot signal.
Flame should be steady medium hard blue
clearly visible through sight glass.
B. Pilot Cleaning and Maintenance
1. Shut off gas supply and disconnect electrical
service.
2. Disconnect scanner, ignition electrode, loosen
and remove pilot gas line and combustion air line
from fan.
3. Remove mounting fasteners and pull pilot
assembly from heat exchanger.
4. Examine pilot electrode and set gap to 1/8” if
needed. Clean as required.
5. Reassemble in reverse order using a new gasket
available from Thermal Solutions.
Burner Flame:
A. Perform a visual inspection of main burner flame.
1. Observe main flame and record flame signal.
Flame should be steady deep orange in color
with dark blue checkerboard pattern throughout.
2. Main burner requires no cleaning or annual
maintenance
Main Burner:
A. When properly maintained and operated the burner
does not require servicing.
CAUTION
Do not attempt to remove or service burner.
Damage to the burner may result. Consult boiler
manufacturer.
B. When the air filter is not properly maintained, the
burner is susceptible of clogging. Check manifold
pressure during the purge cycle to test for clogging.
1. Install a pressure fitting in the tapping on the gas
manifold valve inside the boiler.
2. Attach a pressure monitoring device to the
pressure fitting.
3. Check the pressure while the boiler is in the
purge sequence.
4. If the measured pressure is considerably higher
than expected, consult factory.
Check Combustion and Safety Controls:
A. Check flame failure detection system with system
operating.
1. Pilot
a. Refer to the flame safeguard instruction
manual.
b. Manually close pilot fuel supply and
verify lock out of primary control.
2. Main Flame
a. Refer to the flame safeguard instruction.
b. Close manual main fuel shut off valve
and verify lockout of primary control.
Check Heat Exchanger:
A. Remove lower front jacket panel and check for any
signs of corrosion and leaks.
B. Remove pipe plugs in header and inspect inside of
copper tubes and header.
C. Flush boiler and mechanically remove any scale.
Summary of Contents for EVO-1000
Page 13: ...13 Figure 4 Vertical Pressurized Venting...
Page 15: ...15 Figure 5 Typical Negative Pressure Conventional Venting...
Page 17: ...17 Figure 7 Vertical Air Intake Piping...
Page 26: ...26 Figure 9a Standard UL FM CSD 1 Wiring Diagram on off EVO 500 2000...
Page 27: ...27 Figure 9b Standard UL FM CSD 1 Wiring Diagram Modulation EVO 500 2000...
Page 30: ...30 Figure 11 Modular System Horizontal Air Intake Piping...
Page 31: ...31 Figure 12 Modular System Vertical Air Intake Piping...
Page 32: ...32 Figure 13 Modular System Typical One Pipe Water Piping...
Page 33: ...33 Figure 14 Modular System Typical Primary Secondary Water Piping...
Page 34: ...34 Figure 15 Modular System Typical Primary Secondary without System Pump...
Page 35: ...35 Figure 16 Modular System Typical Reverse Return Water Piping...
Page 36: ...36 Figure 17 Modular System Reverse Return with System Pump Only...
Page 37: ...37 Figure 18 Modular System Typical Primary Secondary with Reverse Return...
Page 47: ...47 This Page Intentionally Left Blank...
Page 48: ...48 Troubleshooting Guide B Troubleshooting Guide...
Page 49: ...49 Troubleshooting Guide...
Page 53: ...53 This Page Intentionally Left Blank...
Page 54: ...54 Figure 19 Combustion Chamber Assembly...
Page 56: ...56 Figure 20 Burner Assembly FRONT VIEW TOP VIEW...
Page 58: ...58 Figure 21 UL FM CSD 1 Main Gas Train Assembly...
Page 60: ...60 Figure 22a DB B DB B w POC Gas Train 500 750 Figure 22b DB B DB B w POC Gas Train 1000 2000...
Page 62: ...62 Figure 23 Jacket Panels 4D 4J 4C 4B 4F 4I 4G 4E 4R 4K 4H 4J 4N 4M 4L 4Q 4A 4P 4P...
Page 64: ...64 Figure 24a Control Panel Assembly On Off...
Page 66: ...66 Figure 24b Control Panel Assembly Modulation...
Page 68: ...68 Figure 25 Bishop Pilot Assembly...
Page 72: ...72 NOTES...
Page 73: ...73 NOTES...
Page 74: ...74 NOTES...
Page 75: ...75 NOTES...