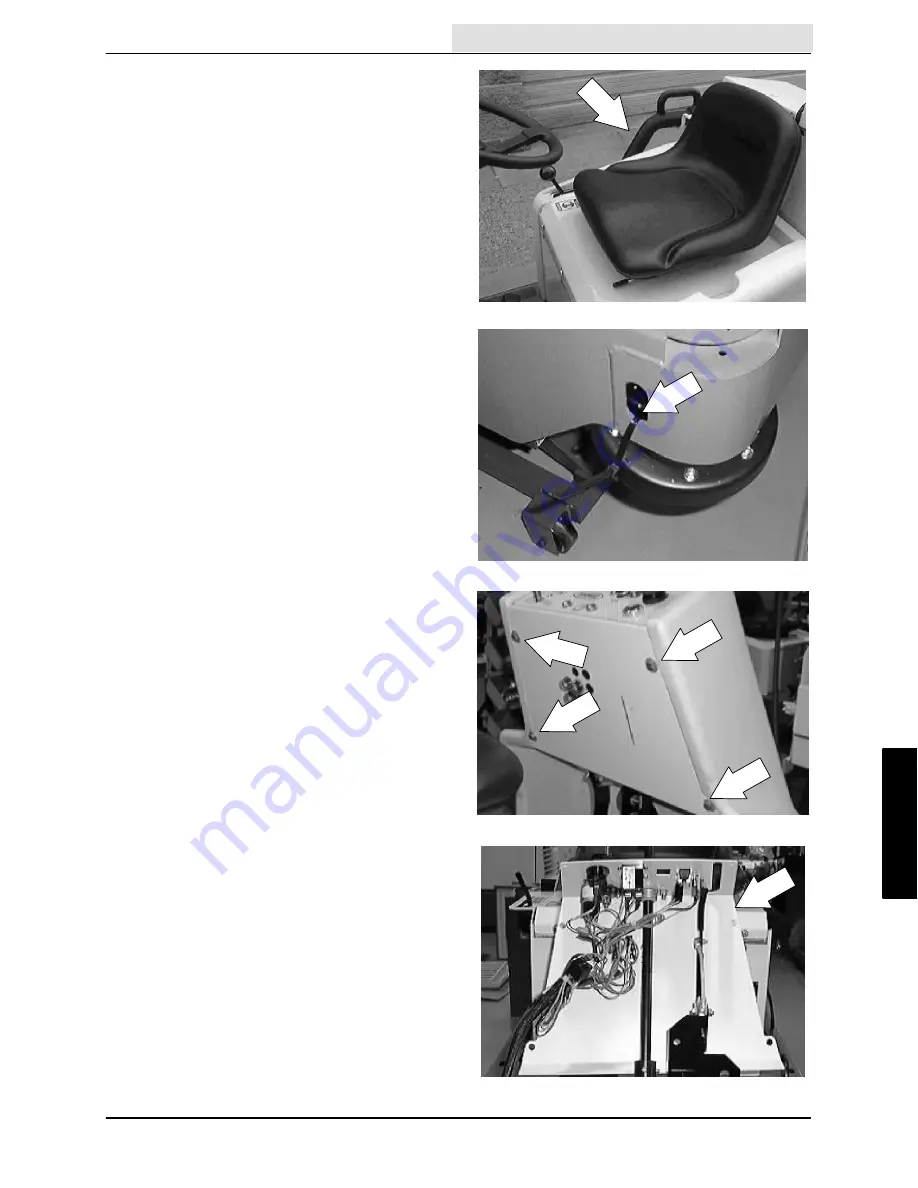
ELECTRICAL
4--13
6100E 330255 (9--00)
3. Disengage the prop rod and lower the seat
support.
4. Tie the side brush in the up position.
5. Remove the four hex screws and two pan
screws holding the instrument panel to the
front shroud.
6. Pull the instrument panel back away from
the front shroud for better access to the
circuit breakers.
Summary of Contents for 6100E
Page 1: ...330255 Rev 02 6 01 Service Manual 6100E ...
Page 4: ...GENERAL INFORMATION 1 2 6100E 330255 6 01 ...
Page 18: ...CHASSIS 2 2 6100E 330255 9 00 ...
Page 27: ...CHASSIS 2 11 6100E 330255 9 00 7 Remove the hub assembly from the tire assembly ...
Page 82: ...CHASSIS 2 66 6100E 330255 9 00 ...
Page 144: ...ELECTRICAL 4 2 6100E 330255 9 00 ...
Page 210: ...ELECTRICAL 4 68 6100E 330255 6 01 ELECTRICAL SCHEMATIC 1 2 3 ...
Page 211: ...ELECTRICAL 4 69 6100E 330255 6 01 ELECTRICAL SCHEMATIC 1 2 3 ...
Page 212: ...ELECTRICAL 4 70 6100E 330255 6 01 WIRE HARNESS ...
Page 213: ...ELECTRICAL 4 71 6100E 330255 6 01 WIRE HARNESS ...
Page 214: ...ELECTRICAL 4 72 6100E 330255 6 01 WIRE HARNESS ...