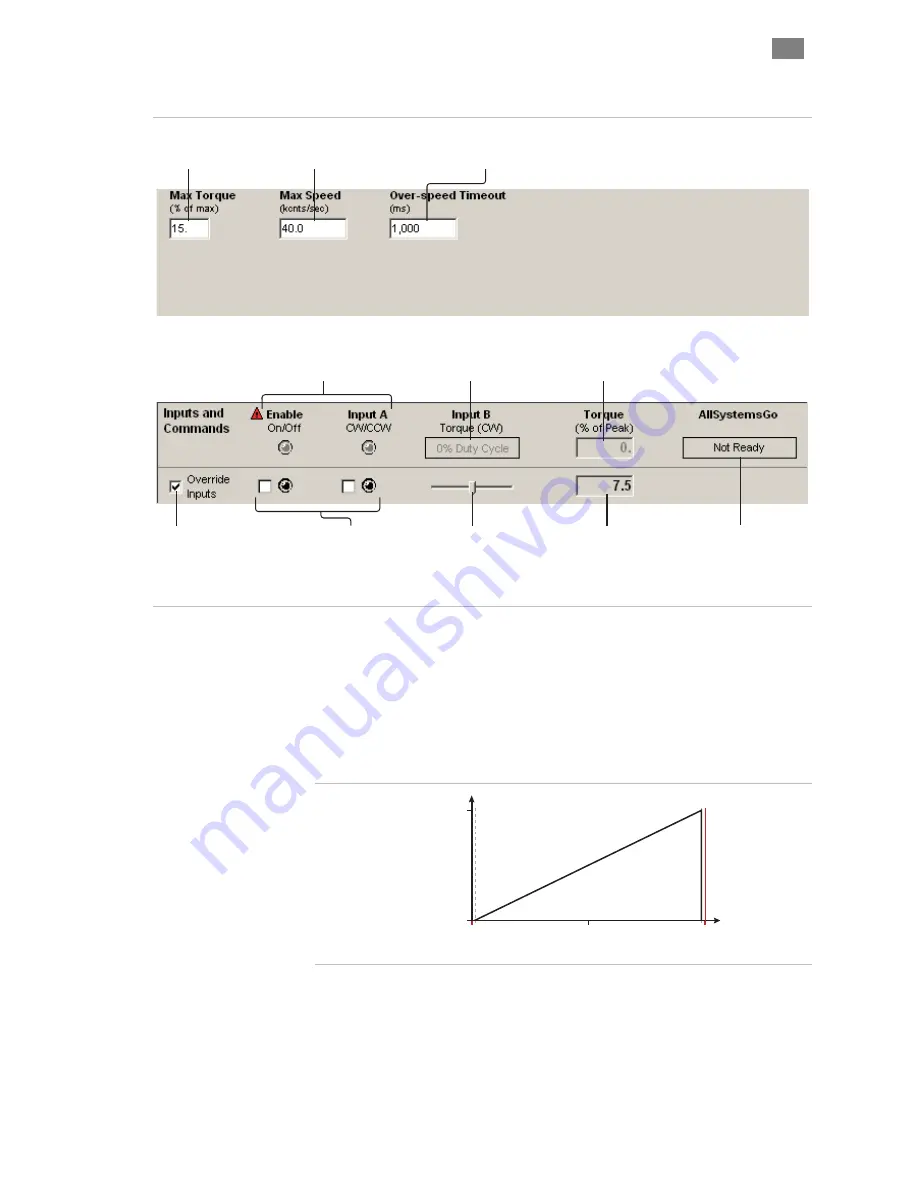
C
L E A R
P
A T H
U
S E R
M
A N U A L
R
E V
.
1 . 9 7
6 3
M
ODE
C
ONTROLS
Enter maximum speed.
ClearPath will shut down if
this speed limit is exceeded.
Enter maximum
motor torque (i.e. full
scale torque).
Soft Inputs and LEDs
Emulate hardware inputs. For
use only when Soft Controls
are active.
Caution: motor
may spin when enabled.
Displays commanded
torque (when using
Soft Controls).
Displays commanded
torque (when using
hard controls).
Hardware Input Status LEDs
Light = Input asserted (on)
Dark = Input de-asserted (off)
PWM Meter -
Displays
duty cycle of PWM source
connected to Input B.
PWM Soft Slider
Emulates PWM
input (for use with
Soft Controls).
Displays output status
HLFB modes supported:
>Servo On
>AllSystemsGo
>Speed Output
Check to turn on Soft
Controls. Override cannot
be activated when ClearPath
is hardware enabled.
Enter value in mS. Determines
how long ClearPath can spin at
max speed before shutting down.
Motor torque vs. PWM duty cycle:
e (i.e. torque
low.
•
0% and 100% duty cycle signals (static low and static high
respectively) are invalid PWM states, interpreted by ClearPath
zero-torque
•
Motor torque is proportional to PWM duty cycl
increases as duty cycle increases). See figure be
as “PWM turned off”. This is the equivalent of a
command.
0
50
100
PWM Duty Cycle (%)
Torque
Max. Torque
(user set)
0
PWM duty cycle vs. torque
•
For CW torque, set Input A high. For CCW torque, set Input A
low.
•
PWM minimum on time and minimum off time = 300nS
T
EKNIC
,
I
NC
.
F
AX
(585)784-7460
V
OICE
(585)784-7454