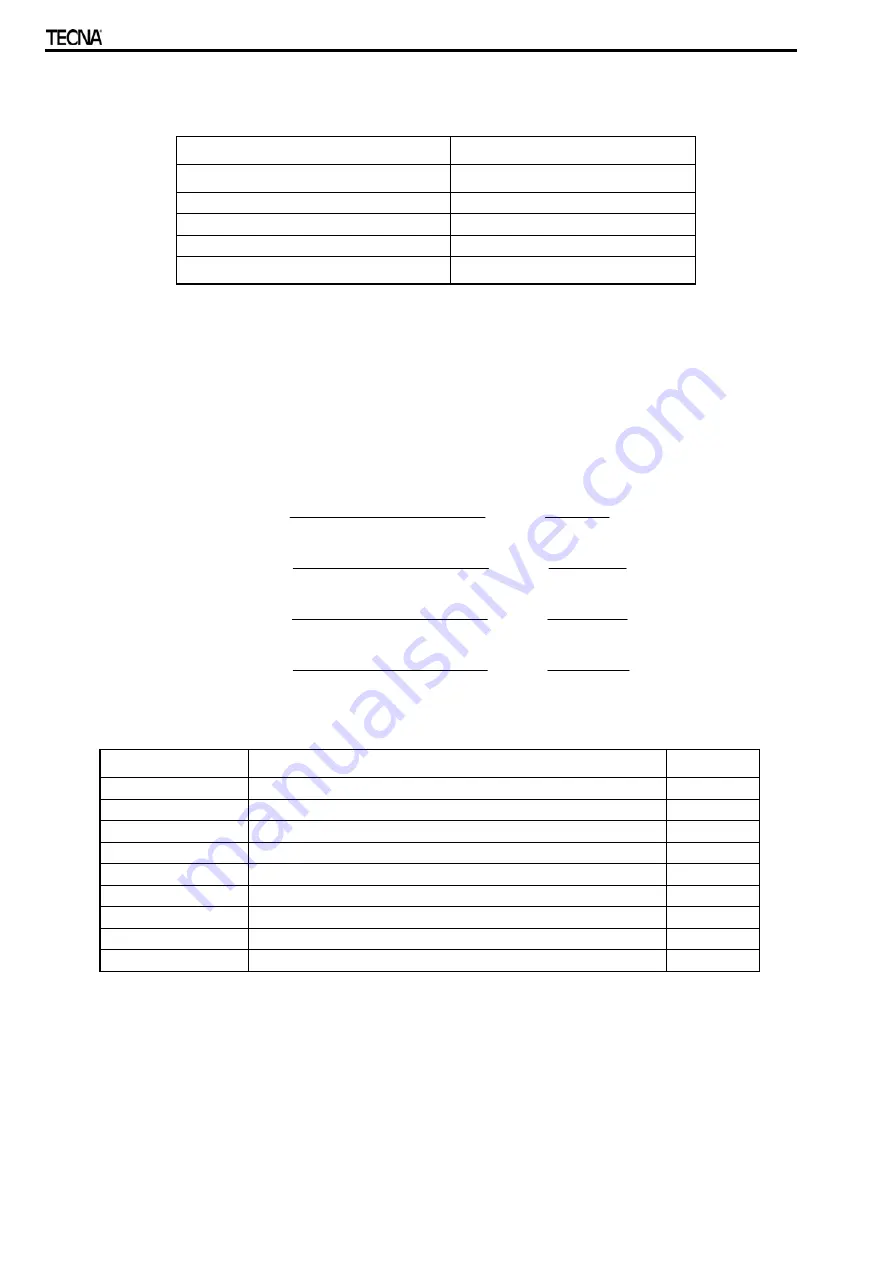
S.p.A.
TE470/TE480 Instruction
Manual
Example:
Welding tests have determined that the electrode life corresponds to 4000 welding spots, and that the following
currents values are necessary at different moments of the electrodes life
SPOTS PERFORMED
REQUIRED CURRENT
0 (initial electrodes diameter)
15 kA
700 17.8
kA
1800 19.5
kA
3000 20.2
kA
4000 (end electrodes diameter)
20.7 kA
For each segment, it is then possible to calculate both the duration (expressed in welding spots) and the percent
increment.
Please, notice that the percent increment must always be calculated referring to the beginning of the considered
segment.
spots
700
=
0
-
700
=
1
segment
of
Duration
spots
1100
=
700
-
1800
=
2
segment
of
Duration
spots
1200
=
1800
-
3000
=
3
segment
of
Duration
spots
1000
=
3000
-
4000
=
4
segment
of
Duration
%
19
100
15
15
8
.
17
100
1
%
rent
initialcur
rent
initialcur
endcurrent
segment
Change
%
10
100
8
.
17
8
.
17
5
.
19
100
2
%
rent
initialcur
rent
initialcur
endcurrent
segment
Change
%
4
100
5
.
19
5
.
19
2
.
20
100
3
%
rent
initialcur
rent
initialcur
endcurrent
segment
Change
%
3
100
2
.
20
2
.
20
8
.
20
100
4
%
rent
initialcur
rent
initialcur
enecurrent
segment
Change
The following parameters are set in the
SETUP MENU
:
PARAMETER PARAMETER
DESCRIPTION
VALUE
TOTAL STEPS
Number of segments per stepper function
4
SPOTS 1
Number of spots of the first segment
700
INCREMENT 1
Increment percent of first segment
19%
SPOTS 2
Number of spots of the second segment
1100
INCREMENT 2
Increment percent of second segment
10%
SPOTS 3
Number of spots of the third segment
1200
INCREMENT 3
Increment percent of third segment
4%
SPOTS 4
Number of spots of the fourth segment
1000
INCREMENT 4
Increment percent of fourth segment
3%
The welding program must be set in order to carry out the first welding spot, that is with an adjustment enabling
to obtain the necessary current with the starting electrodes diameter: 15 kA.
28/52